一、目視檢查與外觀損傷評估
-
- 檢查內容:輪轂裂紋、腐蝕、凹痕;剎車盤表面燒蝕、劃痕、涂層剝落;輪胎磨損、鼓包、異物刺穿等。
- 方法:高分辨率內窺鏡探查輪轂內部,熒光滲透檢測(FPT)定位微裂紋,3D光學掃描記錄輪胎胎面形貌。
- 標準:依據FAA AC 43.13-1B判定損傷是否超出允許極限。
-
- 重點關注剎車組件緊固螺栓的變形、松動跡象,以及剎車作動筒的液壓油滲漏。
二、尺寸與公差測量
-
- 剎車盤厚度:使用激光測厚儀多點測量,確保均勻磨損(允許偏差通常≤0.05mm)。
- 輪轂軸承游隙:通過千分表檢測軸向/徑向間隙,防止過熱卡滯。
- 輪胎胎面溝槽深度:低于制造商規定值(如<1.6mm)需強制更換。
-
- 檢查剎車盤端面跳動量(一般要求≤0.1mm),超差會導致制動抖動。
三、材料性能測試
-
- 渦流檢測(ECT):快速篩查輪轂鋁合金疲勞裂紋。
- 超聲波檢測(UT):探測剎車鋼盤內部分層缺陷。
-
- 碳碳(C/C)剎車盤需進行密度測試(確保≥1.7g/cm³)和孔隙率檢測(防止熱衰退)。
四、功能與性能測試
-
- 模擬著陸載荷,通過慣性試驗臺測量剎車力矩曲線,驗證制動效率是否衰減。
-
- 檢測剎車作動筒壓力上升時間(標準常為<0.3秒),防止響應延遲。
-
- 注入模擬滑水信號,驗證剎車壓力調節頻率(通常≥10Hz)與控制邏輯。
五、熱力學性能驗證
-
- 紅外熱成像儀捕捉剎車過程溫度場,識別局部過熱區域(單點溫差>150℃為異常)。
-
- 連續多次重載剎車后,測試摩擦系數下降率(行業要求≤15%)。
六、密封性與耐壓試驗
-
- 充氮氣至1.5倍工作壓力(如300psi),保壓30分鐘泄漏率需<5%。
-
- 施加2倍額定壓力驗證管路耐壓能力,防止飛行中爆裂。
七、特殊環境適應性檢測
-
- -55℃環境下測試剎車啟動扭矩,驗證材料低溫脆性。
-
- 按ASTM B117標準進行72小時鹽霧暴露,評估防腐涂層耐久性。
八、數據管理與適航合規
-
- 采用區塊鏈技術記錄檢測結果,確保可追溯性與不可篡改性。
-
- 核對AD/SB(適航指令/服務通告)執行情況,確認部件維修履歷完整。
結語

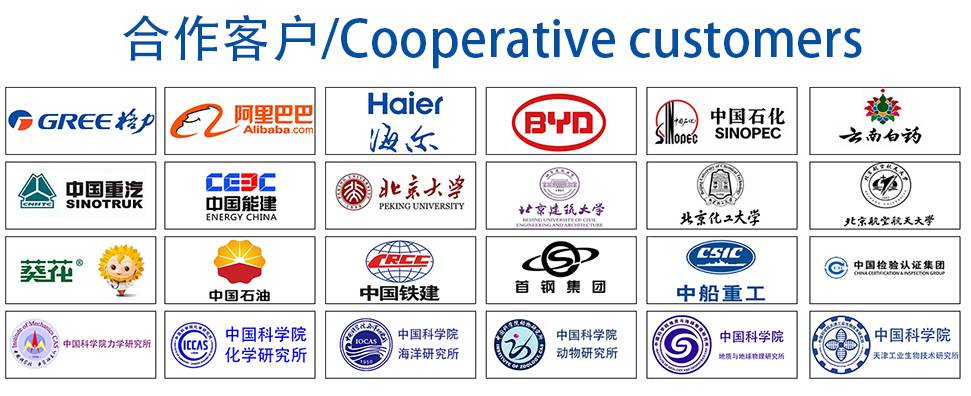
材料實驗室
熱門檢測
18
17
18
23
21
17
19
19
18
24
20
21
18
20
20
25
15
17
20
22
推薦檢測
聯系電話
400-635-0567