一、剎車系統(tǒng)組成與檢測目標
- 剎車盤組件(碳/碳復合材料或鋼制剎車盤)
- 作動系統(tǒng)(液壓活塞、蓄壓器、閥門)
- 傳感器系統(tǒng)(溫度、壓力、磨損監(jiān)測)
- 防滑控制系統(tǒng)(ABS功能模塊)
二、核心檢測項目分類
1. 目視與基礎檢查
-
- 檢測內(nèi)容:剎車盤表面裂紋、分層、燒蝕痕跡;作動機構(gòu)油液泄漏、腐蝕。
- 工具:高倍放大鏡、內(nèi)窺鏡(針對隱蔽區(qū)域)。
- 標準:依據(jù)AMM(飛機維護手冊)判定缺陷等級。
-
- 檢測內(nèi)容:剎車盤厚度、摩擦材料剩余量(對比初始厚度)。
- 工具:數(shù)顯卡尺、激光測厚儀。
- 標準:磨損超過制造商規(guī)定的最大允許值(通常為原始厚度的50%)需更換。
2. 功能測試
-
- 檢測內(nèi)容:液壓作動壓力穩(wěn)定性、響應時間。
- 方法:模擬剎車指令,記錄壓力上升速率及峰值是否符合手冊閾值(如波音737NG要求液壓壓力≥3000 psi)。
- 工具:壓力傳感器、數(shù)據(jù)采集系統(tǒng)。
-
- 檢測內(nèi)容:防滑控制邏輯、作動頻率。
- 方法:在試驗臺模擬滑移條件,驗證系統(tǒng)能否快速調(diào)整剎車壓力。
- 標準:剎車力矩波動幅度需控制在±5%以內(nèi)。
3. 性能測試
-
- 檢測內(nèi)容:不同壓力下的制動力矩輸出。
- 工具:力矩傳感器、動態(tài)加載裝置。
- 標準:輸出力矩需與手冊曲線匹配,偏差>10%判定為異常。
-
- 檢測內(nèi)容:模擬多次剎車循環(huán)(如起飛中斷時的最高能量剎車)。
- 方法:在臺架試驗中施加高能載荷(如能量密度≥200 MJ/m²),檢測剎車盤是否有熱裂紋或變形。
- 標準:連續(xù)10次循環(huán)后,剎車效率下降不得>15%。
4. 無損檢測(NDT)
-
- 檢測內(nèi)容:剎車盤內(nèi)部微小裂紋、材料缺陷。
- 工具:渦流探傷儀,頻率范圍1-5 MHz。
- 標準:缺陷深度>0.5 mm或長度>3 mm需報廢。
-
- 檢測內(nèi)容:復合材料剎車盤的分層、脫粘。
- 方法:使用縱波探頭,檢測信號衰減情況。
- 標準:分層面積超過5%總表面積需修復或更換。
5. 特殊環(huán)境測試
-
- 檢測內(nèi)容:-40℃環(huán)境下液壓油黏度對剎車響應的影響。
- 方法:環(huán)境艙模擬極寒條件,測量作動延遲時間。
- 標準:延遲時間<1.5秒(參考SAE AS1245)。
-
- 檢測內(nèi)容:金屬部件(如活塞桿)的耐腐蝕性。
- 標準:按ASTM B117進行48小時測試,表面銹蝕面積<0.1%。
三、檢測周期與記錄管理
- 周期要求:
- 日常航線檢查:每次飛行后目視檢查。
- 深度檢測:每500次起落或1年(以先到者為準)。
- 數(shù)據(jù)管理:使用電子履歷系統(tǒng)(如TRUEngine)記錄檢測結(jié)果,關(guān)聯(lián)部件序列號,實現(xiàn)全壽命追溯。
四、案例分析:典型故障與檢測對策
-
- 故障現(xiàn)象:著陸時剎車震顫。
- 檢測手段:渦流檢測發(fā)現(xiàn)深度1.2 mm裂紋。
- 處理措施:更換剎車盤并升級為抗疲勞涂層型號。
-
- 故障原因:低溫下密封圈硬化導致泄漏。
- 解決方案:更換氟橡膠密封件,并通過壓力曲線測試驗證。
五、
上一篇:飛機航空機輪和剎車裝置檢測下一篇:氟苯尼考(氟甲砜霉素)檢測

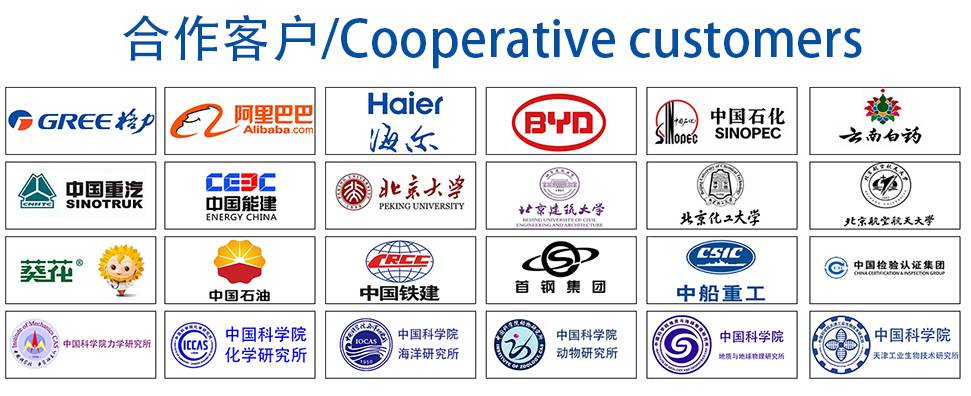
材料實驗室
熱門檢測
16
16
17
21
14
16
23
15
16
13
20
14
17
15
18
24
16
22
24
22
推薦檢測
聯(lián)系電話
400-635-0567