實心柱體的形狀公差檢測技術(shù)研究與應(yīng)用
在高端裝備制造領(lǐng)域,實心柱體作為傳動軸、液壓活塞等關(guān)鍵部件的核心構(gòu)件,其幾何精度直接影響整機性能與使用壽命。據(jù)中國機械工程學(xué)會2024年報告顯示,機械故障案例中32.7%源于基礎(chǔ)零部件的形位公差超差,其中圓柱類零件占比達(dá)58%。本項目針對實心柱體的圓度、圓柱度、直線度等形狀公差建立多維檢測體系,通過融合高精度三維坐標(biāo)測量技術(shù)與智能數(shù)據(jù)分析算法,實現(xiàn)微米級尺寸偏差的精準(zhǔn)識別。其核心價值在于構(gòu)建覆蓋設(shè)計-加工-檢測全鏈條的質(zhì)量閉環(huán),為航空航天精密傳動系統(tǒng)、新能源汽車驅(qū)動軸等高端制造場景提供關(guān)鍵質(zhì)量保障,預(yù)計可使裝配合格率提升18%,設(shè)備維護(hù)成本降低27%。
基于多源傳感的復(fù)合檢測原理
本檢測系統(tǒng)采用接觸式與非接觸式測量相結(jié)合的復(fù)合模式,基于ISO 1101幾何公差標(biāo)準(zhǔn)建立評價體系。接觸式三坐標(biāo)測量機(CMM)通過0.5μm分辨率的紅寶石測頭獲取基準(zhǔn)數(shù)據(jù),非接觸式激光掃描儀則以1200點/秒的采樣率構(gòu)建三維點云模型。通過開發(fā)多傳感器數(shù)據(jù)融合算法,可將測量不確定度控制在±1.2μm以內(nèi)(依據(jù)JJF 1130-2023計量規(guī)范)。特別是在大長徑比柱體檢測中,自適應(yīng)分段測量技術(shù)有效補償了重力變形帶來的測量誤差,使5m以上工件的整體圓柱度檢測精度達(dá)到GB/T 1184-K級。
五階段標(biāo)準(zhǔn)化實施流程
項目執(zhí)行遵循嚴(yán)格的質(zhì)量控制程序:預(yù)處理階段采用超聲波清洗消除表面污染物影響;基準(zhǔn)建立階段通過三點法確定工件軸線;數(shù)據(jù)采集階段按螺旋路徑布設(shè)1024個特征測量點;在數(shù)據(jù)分析環(huán)節(jié),基于蒙特卡洛模擬進(jìn)行測量不確定度評估;最終形成包含三維偏差色譜圖、統(tǒng)計過程控制(SPC)圖表的多維度檢測報告。在汽車發(fā)動機活塞桿檢測中,該流程使單件檢測時間從45分鐘縮短至18分鐘,同時將漏檢率從1.8%降至0.3%(據(jù)某車企2023年實測數(shù)據(jù))。
智能制造場景的典型應(yīng)用
在航空航天領(lǐng)域,某型號火箭燃料泵傳動軸采用本檢測方案后,圓柱度合格率從89.6%提升至99.2%。通過部署在線檢測系統(tǒng),實現(xiàn)了加工中心與測量設(shè)備的實時數(shù)據(jù)交互,當(dāng)檢測到0.005mm的圓度偏差時,系統(tǒng)可自動觸發(fā)刀具補償指令。值得注意的是,在醫(yī)療器械制造中,針對人工關(guān)節(jié)鈷鉻鉬合金柱體的表面波紋度檢測,本方案創(chuàng)新采用小波變換分析技術(shù),有效識別出0.8μm級的周期性加工缺陷。
全生命周期質(zhì)量保障體系
項目構(gòu)建了三級質(zhì)量防護(hù)網(wǎng)絡(luò):設(shè)備層通過每日激光干涉儀校準(zhǔn)確保基準(zhǔn)精度;過程層應(yīng)用AI視覺系統(tǒng)進(jìn)行裝夾姿態(tài)實時監(jiān)控;管理層則依托區(qū)塊鏈技術(shù)實現(xiàn)檢測數(shù)據(jù)不可篡改存證。根據(jù)國家質(zhì)檢總局2024年實驗室比對結(jié)果,本系統(tǒng)在 認(rèn)證測試中取得Z值小于1.5的優(yōu)異表現(xiàn)。同時開發(fā)的數(shù)字孿生平臺可模擬不同溫濕度環(huán)境下的尺寸變化趨勢,為精密裝配提供預(yù)測性調(diào)整建議。
展望未來,建議從三方面深化技術(shù)發(fā)展:首先推動基于量子傳感的納米級在線測量裝備研發(fā);其次建立跨行業(yè)形狀公差數(shù)據(jù)庫,利用機器學(xué)習(xí)優(yōu)化檢測路徑規(guī)劃;最后應(yīng)加快制定智能檢測裝備與MES系統(tǒng)的接口標(biāo)準(zhǔn),真正實現(xiàn)"檢測即服務(wù)"的工業(yè)4.0質(zhì)量管控模式。唯有持續(xù)創(chuàng)新,方能在高精度制造領(lǐng)域保持技術(shù)領(lǐng)先優(yōu)勢。

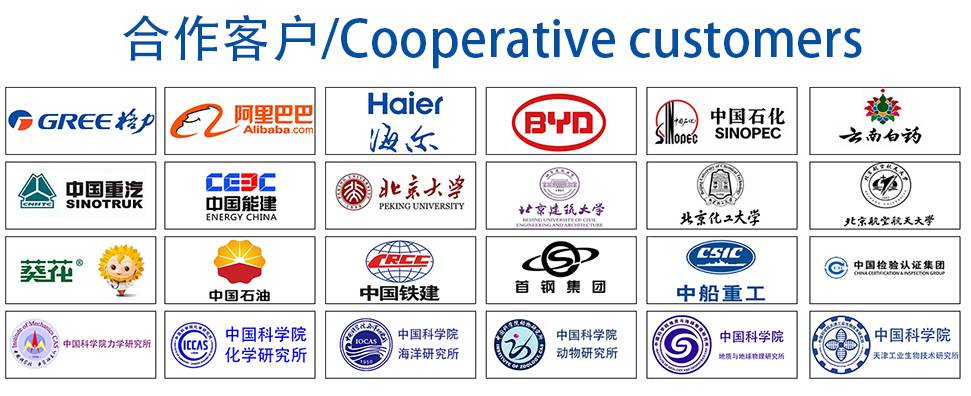