汽輪機檢測:關鍵項目與實施方法
一、運行狀態監測
-
- 目的:識別轉子不平衡、軸系對中偏差、軸承磨損等問題。
- 方法:安裝振動傳感器(如加速度計、位移探頭),實時采集軸承座和轉軸振動數據,結合頻譜分析定位故障源。
- 標準:參考ISO 10816,振動幅值超過50μm(峰值)需停機檢查。
-
- 關鍵部位:軸承溫度(正常范圍:40~70℃)、汽缸壁溫、蒸汽進出口溫度。
- 技術手段:熱電偶、紅外熱成像儀;異常溫升可能預示潤滑失效或熱應力變形。
-
- 油質分析:黏度、水分含量(≤0.1%)、顆粒污染度(ISO 4406標準)。
- 油壓與流量:監測供油壓力波動(±5%以內為正常),確保軸承潤滑充足。
二、停機檢修關鍵項目
-
- 動平衡測試:使用動平衡機校正轉子,殘余不平衡量需低于G2.5級標準。
- 葉片檢查:目視+磁粉探傷(MT)檢測裂紋;測量葉根間隙,超差0.1mm需調整。
- 軸頸與軸瓦:檢查磨損量(徑向間隙≤0.15mm),巴氏合金層無剝落。
-
- 汽缸水平度:激光準直儀測量,偏差≤0.05mm/m。
- 汽封間隙:塞尺檢測,徑向間隙控制在0.3~0.5mm,過大導致蒸汽泄漏效率下降。
-
- 高溫螺栓硬度:布氏硬度檢測(HB 200~250),防止應力松弛。
- 法蘭密封面:滲透檢測(PT)排查微觀裂紋,確保氣密性。
三、專項檢測技術應用
-
- 超聲波檢測(UT):用于厚壁汽缸、轉子內部缺陷掃描,可發現≥2mm的夾雜或裂紋。
- 渦流檢測(ET):檢測葉片表面及近表面缺陷,精度達0.1mm。
-
- 方法:測量蒸汽流量、壓力、溫度,計算實際熱效率與設計值偏差(通常允許±3%)。
- 改進方向:優化通流部分間隙、減少級間泄漏損失。
-
- 調速系統響應:階躍信號測試,轉速波動恢復時間應<10秒。
- 保護聯鎖試驗:模擬超速(110%額定轉速)、低油壓等工況,驗證緊急停機可靠性。
四、檢測周期與故障預警
- 日常監測:振動、溫度、油質等參數需實時監控并記錄。
- 定期檢測:每3個月進行潤滑油化驗,每年一次全面停機檢查。
- 大修周期:運行4~6萬小時或累計啟停500次后,需解體大修。
五、未來趨勢:智能化檢測
- AI診斷系統:基于歷史數據訓練模型,實現故障早期預警(如軸承磨損趨勢預測)。
- 無線傳感器網絡:減少布線成本,提升監測密度與實時性。
- 數字孿生技術:構建虛擬汽輪機模型,模擬極端工況下的應力分布,優化檢修策略。
轉成精致網頁

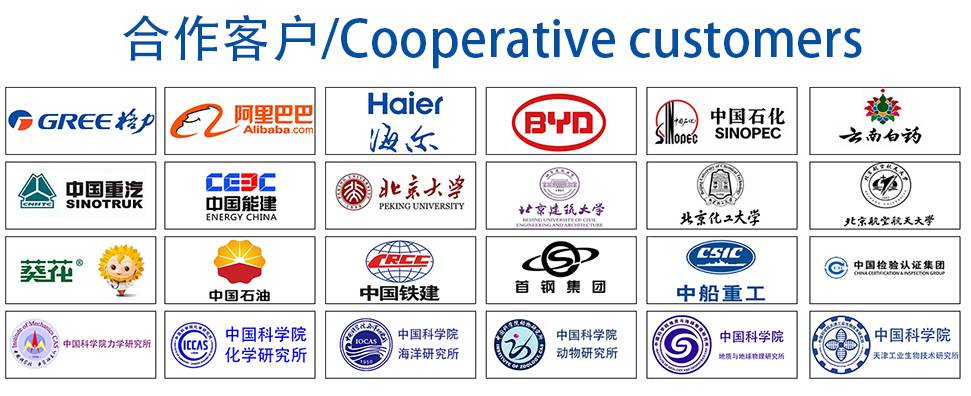
材料實驗室
熱門檢測
18
19
22
19
25
23
22
21
23
16
18
17
18
24
25
22
23
20
24
19
推薦檢測
聯系電話
400-635-0567