工業窯爐用型煤檢測技術及關鍵檢測項目
一、物理性能檢測
-
- 定義:型煤在受壓狀態下抵抗破碎的能力,反映其在運輸和投料過程中的耐久性。
- 檢測方法:使用萬能試驗機或壓力試驗機,測定單顆型煤在垂直方向的最大破碎載荷(單位:N/個或MPa)。
- 標準要求:多數工業窯爐要求抗壓強度≥600 N/個,重型窯爐可能需≥1000 N/個。
-
- 定義:模擬型煤從高處跌落時的抗碎裂能力。
- 檢測方法:將型煤從2米高度自由落體至鋼板,重復多次后測定破碎率。
- 指標意義:跌落破碎率需≤10%,否則會導致燃燒過程中粉塵增多,影響窯爐效率。
-
- 定義:型煤在高溫下的結構穩定性,避免燃燒時因熱應力開裂。
- 檢測方法:將樣品置于高溫爐中(通常900~1000℃)加熱30分鐘,冷卻后測定殘存完整顆粒的比例。
- 關鍵參數:熱穩定性合格率應≥80%,否則易導致窯內通風不暢或結渣。
-
- 檢測內容:直徑、長度、孔隙率等幾何參數,直接影響燃燒時的透氣性和傳熱效率。
- 方法:隨機抽樣測量,結合圖像分析技術評估成型工藝的一致性。
二、化學性能檢測
-
- 項目:水分(M)、灰分(A)、揮發分(V)、固定碳(FC)。
- 檢測標準:依據GB/T 212-2008《煤的工業分析方法》。
- 控制范圍:
- 水分:窯爐用型煤水分需≤5%(過高會降低燃燒溫度);
- 灰分:灰分≤20%(過高導致熱值下降、結渣風險增加);
- 揮發分:根據窯爐類型調整,一般控制在10%~30%。
-
- 項目:碳(C)、氫(H)、氧(O)、氮(N)、硫(S)含量。
- 儀器:元素分析儀、紅外測硫儀。
- 環保重點:
- 全硫(St,d)≤1.0%(滿足GB 13271-2014煙氣排放標準);
- 氮含量影響NOx生成,需結合脫硝工藝控制。
-
- 定義:單位質量型煤完全燃燒釋放的熱值,直接影響窯爐能耗。
- 檢測方法:氧彈量熱儀(GB/T 213-2008)。
- 典型值:優質工業型煤的發熱量應≥23 MJ/kg。
三、燃燒性能檢測
-
- 測試方法:熱重分析(TGA)結合差示掃描量熱法(DSC),測定型煤在不同溫度下的燃燒曲線。
- 優化目標:降低著火點(縮短點火時間),延長燃盡時間(提高能量利用率)。
-
- 殘炭率測定:燃燒后殘余未燃碳的比例需≤5%,否則表明燃燒不充分。
- 燃燒效率計算:通過煙氣中CO和CO?的比例評估,目標值≥95%。
-
- 檢測意義:灰分在高溫下的熔融特性影響窯內結渣傾向。
- 指標:軟化溫度(ST)需>1200℃,避免堵塞窯爐風道。
四、環保性能檢測
-
- 檢測重點:全硫含量及形態(有機硫、硫酸鹽硫)。
- 減排措施:添加固硫劑(如CaO)降低SOx生成。
-
- 方法:利用管式爐燃燒系統模擬窯爐條件,檢測煙氣中顆粒物(PM)、NOx、SO?濃度。
- 標準參考:GB 13271-2014《鍋爐大氣污染物排放標準》。
-
- 項目:砷(As)、汞(Hg)、鉛(Pb)等痕量元素。
- 檢測手段:原子吸收光譜(AAS)或電感耦合等離子體質譜(ICP-MS)。
五、特殊性能檢測(根據窯爐類型定制)
- 氣化型煤:增加反應活性、孔隙率與氣化效率測試。
- 高強度耐火窯爐用型煤:需檢測高溫抗壓強度(≥5 MPa,1400℃下)。
- 粘結劑安全性:若使用有機粘結劑,需評估其熱解毒性氣體釋放量。
六、檢測標準與質量控制流程
- 標準依據:
- GB/T 18856-2018《工業型煤技術條件》
- ISO 1928:2020《固體礦物燃料發熱量測定》
- 質控流程:
- 原料煤篩選→成型工藝參數優化→批次抽樣檢測→不合格品追溯。
轉成精致網頁

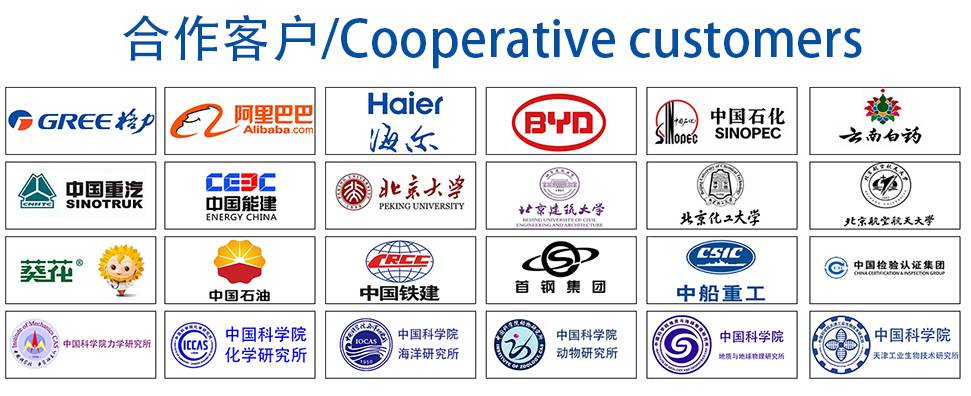
材料實驗室
熱門檢測
18
14
23
20
18
28
24
21
14
24
19
22
18
22
22
22
23
27
22
27
推薦檢測
聯系電話
400-635-0567