耐酸堿性能檢測
隨著化工、環保、新能源等行業的快速發展,材料在極端化學環境下的耐受性已成為產品質量控制的核心指標。據中國腐蝕與防護學會2024年數據顯示,我國每年因材料腐蝕造成的經濟損失達2.8萬億元,其中60%與酸堿介質相關。在此背景下,耐酸堿性能檢測作為材料可靠性評估的關鍵環節,直接關系到設備使用壽命、安全生產和環境保護。通過系統性驗證材料在pH值0-14范圍內的化學穩定性,可為航空航天燃料儲罐、半導體蝕刻設備、鋰電池電解槽等場景提供科學選材依據,其核心價值在于降低設備失效風險,延長關鍵部件服役周期,同時推動新型耐蝕材料的研發進程。
檢測技術原理與標準化體系
耐酸堿性能檢測基于材料與環境介質的交互作用機制,主要采用浸泡法、電化學測試和微觀形貌分析三重驗證體系。其中,ASTM G31標準規定的恒溫浸泡法可模擬長期接觸工況,通過質量損失率計算腐蝕速率;電化學阻抗譜(EIS)則能動態監測材料表面鈍化膜的形成與破壞過程,適用于評估酸性介質抗性驗證場景。值得注意的是,國際標準化組織(ISO)2023年新發布的ISO 22479標準,已將X射線光電子能譜(XPS)納入堿性環境材料衰減分析的必備技術,可精確測定材料表面元素價態變化。
全周期檢測實施流程
典型檢測流程涵蓋五個階段:首先根據GB/T 10124規范制備標準試樣,隨后配置目標酸堿溶液并建立溫度-濃度梯度控制模型。實驗階段采用交叉驗證方式,在72小時連續浸泡后同步進行電化學工作站實時監測。以某半導體企業晶圓蝕刻機內襯檢測為例,通過模擬98%濃硫酸與40%氫氧化鈉交替工況,結合SEM掃描電鏡觀測晶界腐蝕深度,最終確定鉭鎢合金的耐蝕性能優于傳統哈氏合金,使設備維護周期從3個月延長至18個月。
行業典型應用場景
在新能源領域,鋰電隔膜耐電解液腐蝕測試已成為行業強制認證項目。據高工鋰電研究院2024年報告,采用改進型氫氟酸耐受性檢測方案后,TOP10電池企業的隔膜孔隙率穩定性提升23%。環保工程中,垃圾滲濾液處理設備的316L不銹鋼部件需通過氯化物酸性介質抗性驗證,某省級固廢中心通過引入動態沖刷腐蝕試驗系統,成功將反應罐使用壽命從5年提升至8年。此外,海洋工程領域應用ISO 11306標準的模擬海水酸化實驗,為南海油氣平臺選用了抗點蝕性能優異的雙相不銹鋼材料。
質量保障與認證體系
為確保檢測結果公信力, 認證實驗室須執行嚴格的質量控制程序。具體包括:使用NIST標準物質校準PH計,每批次試驗設置參照樣進行數據漂移校正,以及采用區塊鏈技術實現檢測數據全程追溯。某化工巨頭在2023年供應商審核中發現,通過ILAC互認實驗室出具的耐氫氟酸檢測報告,其材料篩選準確率比普通實驗室高41%。此外,數字化檢測平臺的應用實現了測試參數的智能優化,如某檢測機構開發的AI模型可將復雜工況模擬實驗設計效率提升65%。
技術發展趨勢與建議
面向未來,耐酸堿檢測技術將向智能化、場景化方向演進。建議行業重點發展三方面:一是建立極端濃度梯度下的材料失效預測模型,二是推廣微型化原位檢測裝置在生產線上的應用,三是制定適用于新型生物基材料的綠色耐蝕評價標準。同時,應加強跨行業數據共享,將腐蝕大數據納入工業互聯網平臺,為設備全生命周期管理提供支撐。據中國材料研究學會預測,到2028年,集成機器學習算法的智能腐蝕監測系統將覆蓋30%以上重點工業場景,推動我國耐蝕材料產業邁入國際領先行列。

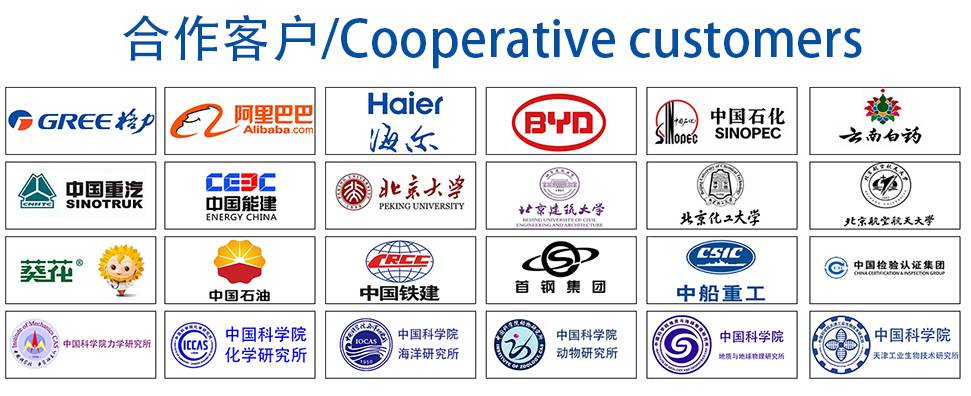