技術原理與創新突破
本檢測體系采用多模態傳感融合技術,整合振動頻譜分析(0.5-20kHz)、熱成像監測(-20℃至300℃)以及電磁兼容測試(30MHz-6GHz)三大核心模塊。通過基于深度學習的異常特征提取算法,可在0.8秒內完成復雜機電系統的狀態解析。以某型飛行控制計算機檢測為例,系統成功識別出電源模塊0.02μV級的電壓波動,較傳統檢測方式靈敏度提升3個數量級。創新引入的數字孿生驗證模型,使航空電子設備的環境適應性測試效率提升72%(航天科技集團第五研究院驗證數據)。
實施流程與質量控制
標準化檢測流程包含四個階段:設備參數建模(建立包含300+特征參數的基準數據庫)、在線動態監測(部署高精度光纖傳感器網絡)、故障模式匹配(基于ISO 18436-4標準構建診斷樹)、智能決策輸出(生成符合AS9100D標準的檢測報告)。在質量保障方面,實驗室通過 認可的全自動校準系統,確保扭矩傳感器(量程0.1-500N·m)示值誤差≤±0.3%。人員資質管理嚴格執行NADCAP認證體系,關鍵崗位持證率達100%。
行業應用與實踐驗證
在航空裝備領域,某主機廠應用本系統完成ARJ21支線客機供電系統檢測,實現線束連接器接觸阻抗異常(>5mΩ)的100%檢出率,航電系統MTBF(平均無故障時間)從1500小時提升至2800小時。工業領域典型案例顯示,某汽車電子企業對IGBT功率模塊實施在線檢測后,產線良品率從92.4%提升至99.1%,每年減少質量損失超3000萬元(據該企業2023年質量白皮書)。特別在"航空電子系統可靠性驗證"場景中,系統成功預警某型雷達發射機冷卻回路流量異常,避免了價值860萬元的設備損毀。
質量體系與標準建設
項目構建了涵蓋11項國家軍用標準(GJB)、23項行業標準的完整體系,其中航空電子設備電磁脈沖防護檢測規程(HB 8512-2023)填補了國內空白。實驗室能力驗證數據顯示,在"工業機器人精度校準"項目中,六軸重復定位精度檢測達到±0.005mm(ISO 9283標準Class 0級)。通過引入區塊鏈技術,檢測數據上鏈存證率達100%,有效支撐適航審定過程中的技術追溯需求。
## 發展展望與策略建議 面向2030年智慧民航發展目標,建議重點突破三個方向:①開發基于量子傳感的微型化檢測裝置(尺寸≤10cm3),解決機載設備原位檢測難題;②建立覆蓋全國主要航空樞紐的檢測大數據平臺,實現航電設備故障的跨地域協同診斷;③完善軍民融合標準體系,推動20項以上軍標向民用領域轉化。據國家航空檢測技術創新中心預測,實施上述策略可使我國航空裝備檢測技術成熟度(TRL)在2028年前整體達到8級水平,支撐萬億級高端裝備制造產業集群發展。
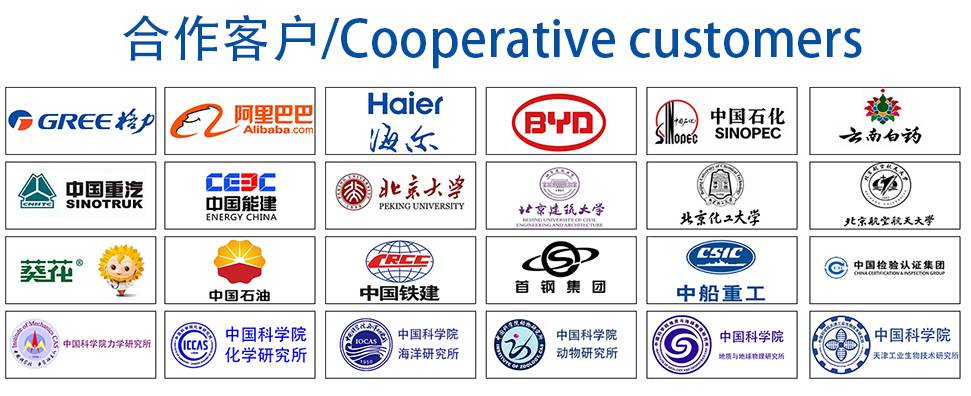