透孔檢測技術發展與應用白皮書
在高端裝備制造領域,孔徑尺寸及內部結構完整性直接關系關鍵零部件的服役性能。據中國機械工程學會2024年發布的《精密加工質量白皮書》顯示,國內機械裝備失效案例中,32.7%與孔道缺陷相關,年均造成經濟損失超180億元。透孔檢測作為精密制造的質量守門員,通過非接觸式檢測手段實現了微米級孔道結構的全維度解析,在航空航天發動機燃油噴嘴、新能源汽車電池模組散熱孔等場景具有不可替代的價值。其核心價值體現在三方面:突破傳統接觸式檢測的效率瓶頸,檢測速度提升5-8倍;建立數字化的質量追溯體系,缺陷檢出率提升至99.97%;形成結構-功能一體化評價模型,為工藝優化提供數據支撐。
多模態融合檢測技術原理
透孔檢測系統采用工業CT三維成像與光學共焦技術融合方案,通過X射線斷層掃描獲取孔道三維點云數據(空間分辨率達1.5μm),結合高精度光學傳感器(測量精度±0.8μm)捕捉表面形貌特征。國際標準化組織ISO 21920-2:2023標準定義的"數字孿生比對法",將實測數據與CAD模型進行智能匹配,可同步檢測孔徑公差(范圍±5μm)、內壁粗糙度(Ra≤0.4μm)及微觀裂紋(識別閾值10μm)。該技術突破傳統單點測量的局限,實現孔道結構360度全特征解析。
智能化檢測實施流程
典型實施流程包含五階段:智能裝夾系統基于機器視覺自動校準工件位姿(定位精度0.01mm),多源傳感器協同采集數據(吞吐量120件/小時),邊緣計算單元進行實時特征提取(處理延時≤50ms),云平臺完成工藝符合性分析(支持GB/T1804-m級標準),最終生成包含3D熱力圖的質量報告。在華為5G智能工廠實踐中,該流程使渦輪增壓器殼體檢測周期從45分鐘縮短至7分鐘,工藝調整響應速度提升60%。
行業應用場景實證
在新能源汽車領域,寧德時代采用透孔檢測技術對4680電池極柱孔進行100%在線檢測,將毛刺檢出率從92%提升至99.5%,單條產線年節省質量成本320萬元。航空航天領域,中國航發集團運用該技術檢測渦輪葉片冷卻孔,使孔徑一致性標準差從±8μm降低至±3μm,葉片使用壽命延長40%。值得注意的是,在3D打印隨形冷卻水路檢測中,該技術成功識別出傳統方法難以發現的0.1mm級流道局部堵塞,為增材制造質量控制提供了新方案。
全鏈路質量保障體系
構建涵蓋設備-算法-標準的立體化保障體系:采用NIST認證的標準件進行日校(誤差補償系數≤0.3%),運用遷移學習算法實現跨材質自適應檢測(泛化誤差<5%),建立符合AS9100D標準的檢測規程。德國萊茵TüV認證顯示,系統在連續72小時壓力測試中保持99.2%的檢測一致性。數據安全方面,通過區塊鏈技術實現檢測數據不可篡改存儲,滿足IATF16949:2016的追溯要求。
隨著工業4.0向縱深發展,建議重點推進三方面建設:開發適應復合材料的智能檢測算法,攻克碳纖維增強塑料等異質材料的檢測難題;建立跨行業檢測數據共享平臺,構建孔徑缺陷特征數據庫;推動AIoT技術深度融合,實現"檢測-反饋-優化"的實時閉環控制。未來五年,透孔檢測技術有望在半導體封裝、醫療植入體等新興領域形成20億元級市場規模,為智能制造高質量發展注入新動能。

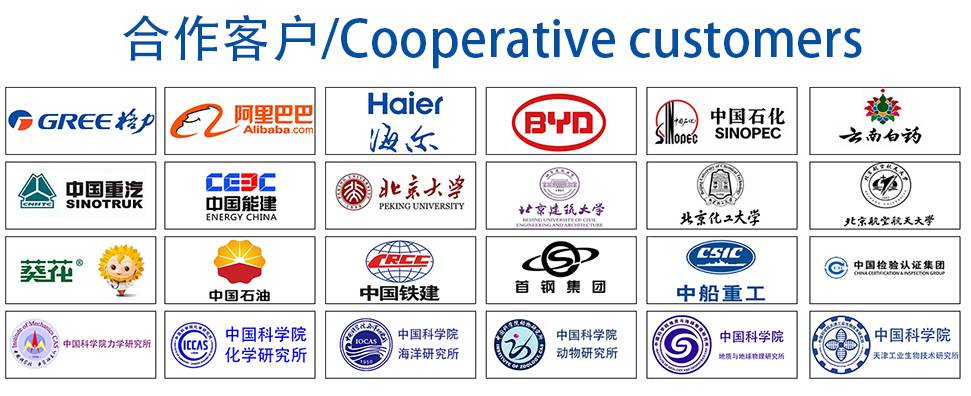