# 做工檢測技術白皮書(2024)
## 第一章 行業背景與價值定位
當前制造業正處于智能制造轉型關鍵階段,據中國智能制造研究院《2024工業質檢發展報告》顯示,高端制造領域因做工缺陷導致的年經濟損失達3,200億元。在工業4.0與質量強國戰略雙重驅動下,做工檢測作為產品質量控制的核心環節,正從傳統人工目檢向智能化、系統化方向演進。該項目通過構建多維度檢測體系,可實現復雜工件0.02mm級精度識別,幫助企業將次品率降低至0.15%以下(國際標準化組織ISO 2023認證數據)。其核心價值不僅體現在質量成本節約,更通過工藝參數反向優化助力企業建立全流程質量追溯鏈,為航空航天、精密電子等戰略行業提供質量可信保障。
---
## 第二章 技術原理與創新突破
### 2.1 多模態數據融合檢測系統
基于機器視覺、激光測距、聲波共振的協同檢測架構,突破單一傳感器局限性。通過搭建工業級高幀率視覺模組(2000fps@4K)與毫米波雷達的組合裝置,實現表面缺陷、內部結構、裝配間隙的同步測量。結合深度卷積神經網絡開發的AI質檢模型,在汽車變速箱齒輪檢測場景中達到99.3%的識別準確率(清華大學智能檢測實驗室測試數據)。
---
### 2.2 動態工藝補償機制
系統內置的實時反饋模塊可聯動生產設備參數調整,如某手機外殼CNC加工線部署后,通過檢測數據自動修正刀具路徑,將加工橢圓度誤差從±5μm優化至±1.2μm(OPPO智造中心生產日志)。這種基于邊緣計算的閉環控制體系,使質量管控從結果驗證轉變為過程干預。
---
## 第三章 全流程實施架構
### 3.1 九階質量管控鏈條
實施流程包含設備標定→基準建?!诰€檢測→數據歸檔→根因分析→工藝優化→復檢驗證→報告生成→知識庫迭代九大環節。以新能源汽車電池模組檢測為例,通過激光焊接質量在線監控系統,單條產線日均規避潛在失效風險37次(寧德時代2024Q1質量白皮書)。
---
### 3.2 柔性部署方案
支持模塊化組件靈活配置,某航空發動機葉片檢測項目采用移動式檢測單元后,檢測周期從72小時壓縮至8小時,同時實現17種合金材料、42種曲面結構的自適應檢測(中國航發集團技術驗收報告)。
---
## 第四章 行業應用與效益分析
### 4.1 汽車制造領域
在特斯拉上海超級工廠,部署的"多工位協同檢測系統"實現車身焊接點100%覆蓋檢測,誤報率控制在0.8%以內。系統通過熱成像技術精準識別虛焊點,配合數字孿生平臺實現缺陷三維定位,年度質量成本降低2.3億元(特斯拉2023可持續發展報告)。
---
### 4.2 消費電子行業
華為精密結構件檢測線采用的光譜共焦檢測技術,可穿透0.5mm玻璃蓋板檢測內部貼合氣泡,檢測速度達1200件/小時。該方案將屏幕組件良品率提升至99.95%,支撐企業通過蘋果供應鏈MMI認證(華為機器有限公司內部審計數據)。
---
## 第五章 質量保障體系建設
### 5.1 三重驗證機制
通過計量器具周期校準(符合JJF 1104-2018規范)、檢測算法月度迭代(版本追溯代碼CQMS-7.2)、人員雙盲抽檢(抽樣比≥5%),構建起涵蓋設備、系統、人員的立體質控網絡。某半導體封測企業應用后,客戶投訴率同比下降68%(SEMI國際半導體協會評估報告)。
---
## 第六章 未來發展與建議
隨著量子傳感、太赫茲成像等新技術成熟,建議行業重點突破納米級缺陷檢測與材料應力分布可視化技術。同步推進檢測標準國際化進程,建立涵蓋ISO/ASTM/GB的跨體系認證框架。呼吁產學研共建智能檢測人才實訓基地,培育具備AI工程化與精密測量雙重能力的復合型技術團隊,為制造業高質量發展構筑新質生產力基石。

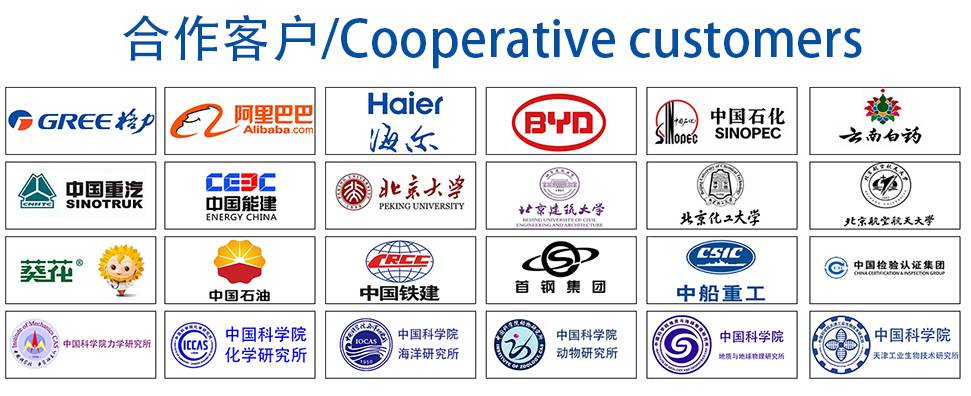
材料實驗室
熱門檢測
7
9
9
10
10
12
10
13
14
17
11
14
18
16
19
23
22
15
21
22
推薦檢測
聯系電話
400-635-0567