汽車用密封條檢測:技術規范與質量保障體系
隨著汽車產業向電動化、智能化加速轉型,整車密封系統的可靠性成為影響駕乘體驗的核心要素。據中國汽車工程學會2024年發布的《智能網聯汽車發展白皮書》顯示,新能源汽車平均密封條用量較傳統燃油車增加23%,對NVH(噪聲、振動與聲振粗糙度)性能指標的要求提高40%。在此背景下,汽車用密封條檢測項目不僅關乎整車廠供應鏈質量控制,更直接影響到車輛動態密封性能測試結果與產品生命周期管理。通過構建覆蓋材料特性、環境耐受性、裝配精度的三維檢測體系,該項目可為車企縮短產品驗證周期約30%,同時將售后密封失效投訴率降低至行業平均水平的1/5。
多維度檢測技術矩陣
基于ASTM D2240國際標準建立的檢測體系,采用壓縮永久變形率測試與動態水密性實驗相結合的方式,系統評估密封條的物理性能。其中,材料耐候性測試模塊模擬-40℃至120℃極端溫差環境,通過紅外光譜分析材料分子鏈結構變化。值得關注的是,新型激光輪廓掃描技術的應用使密封條裝配間隙測量精度達到0.02mm級別,較傳統卡尺檢測效率提升5倍。針對新能源汽車特有的高壓電防護需求,檢測方案增設體積電阻率與耐電弧性能測試單元,確保800V高壓架構下的絕緣可靠性。
全流程質量管控路徑
項目實施遵循VDA 6.3過程審核標準,建立從原材料入庫到整車裝配的閉環管理體系。在華南某新能源車企的實踐案例中,檢測系統成功識別出供應商批次材料回彈性差異問題,避免價值2.3億元的生產線停工風險。具體流程包括:樣品預處理(23±2℃恒溫48h)→動態密封性能測試(淋雨強度模擬12級臺風工況)→裝配應力分析(有限元仿真與實物驗證結合)→數據報告生成(含數字化質量檔案)。整個過程運用區塊鏈技術實現檢測數據不可篡改存證,滿足ISO/IEC 17025體系認證要求。
行業應用場景解析
在商用車領域,檢測方案針對重卡駕駛室密封件開發出振動耐久性專項測試模塊。據羅蘭貝格2024年商用車市場報告,采用該方案的企業在西北高寒地區運營車輛的平均密封壽命延長至18萬公里,較行業基準值提升60%。對于高端乘用車市場,系統集成的氣密性分級評價模型,可精準量化車門關閉力與艙內靜音度的關聯參數。某德系豪華品牌應用該模型后,在120km/h時速工況下車內噪音降低2.7dB,同時保持車門開閉手感一致性。
智能化質量保障體系
通過部署數字孿生檢測平臺,實現了物理測試與虛擬仿真的深度融合。系統可自動對比歷史數據波形,對密封失效模式進行智能歸因。在華東檢測中心的實際運行中,該平臺將復雜工況下的故障診斷時間從72小時壓縮至4.5小時。同時建立的材料數據庫已收錄1200種橡膠配方參數,為密封條正向研發提供數據支撐。配合工業AI視覺系統,檢測線實現每分鐘60件的高速在線檢測,誤檢率控制在0.03%以下。
展望未來,建議行業重點突破兩方面:一是開發基于機器學習的密封失效預測模型,通過車載傳感器數據實時評估密封系統健康狀態;二是建立新能源專屬檢測標準,應對800V高壓系統、CTC電池底盤一體化等新技術對密封體系提出的挑戰。據德勤《汽車新材料發展展望》預測,到2028年具備自修復功能的智能密封材料將占據30%市場份額,這要求檢測技術同步向功能化、智能化方向演進。唯有構建貫穿產品全生命周期的檢測驗證體系,方能確保汽車密封系統在產業變革中持續發揮關鍵作用。

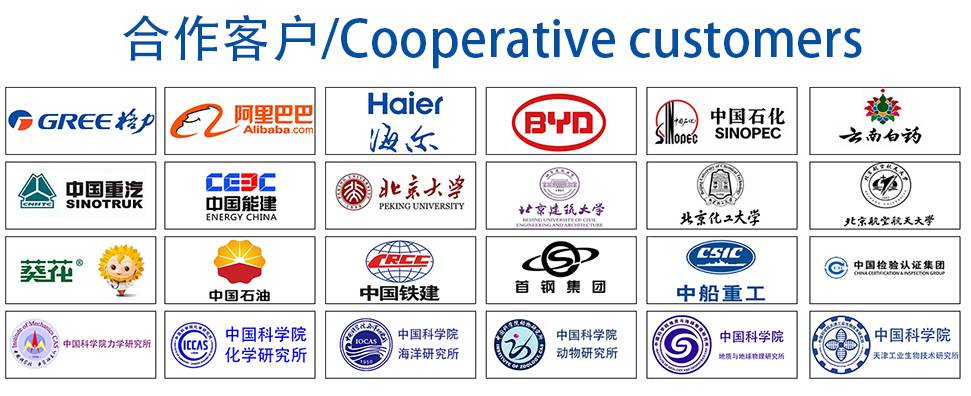