壽命周期試驗檢測技術發展與應用白皮書
在智能制造與新能源產業快速發展的背景下,產品可靠性驗證已成為企業核心競爭力的關鍵指標。據國家質量技術基礎研究院2024年發布的《高端裝備可靠性發展報告》顯示,我國機電設備早期故障率較國際齊全水平高出37%,導致年均經濟損失達1200億元。壽命周期試驗檢測通過模擬產品全生命周期工況,精準預測失效節點,已成為突破"質量瓶頸"的重要技術手段。該項目不僅可縮短新產品研發周期30%以上,更可實現質量成本降低25%-40%的核心價值,特別是在新能源汽車動力系統、工業機器人關鍵部件等領域,已形成"檢測前置、質量內建"的新型品控范式。
基于失效物理的檢測技術原理
現代壽命周期試驗檢測采用基于失效物理(PoF)的可靠性建模方法,通過阿倫尼斯方程、科芬-曼森公式等數學模型,構建溫度、振動、腐蝕等多應力耦合的加速試驗模型。以某型號新能源汽車電機控制器檢測為例,采用三綜合試驗箱實現溫度(-40℃-150℃)、濕度(10%-98%RH)、振動(5-2000Hz)的精準控制,結合7500小時等效工況模擬,可準確預測10年使用周期的性能衰減曲線。值得注意的是,該方法引入蒙特卡洛仿真對制造公差進行敏感性分析,使檢測置信度提升至95%以上。
全流程閉環檢測實施體系
項目實施遵循V型開發模型,建立"需求定義-方案設計-環境模擬-數據采集-失效分析"的完整閉環。在智能倉儲機器人驅動系統檢測中,首先基于MIL-STD-810G標準制定包含2000小時壽命試驗、500次啟停沖擊測試的驗證方案,接著通過六自由度振動臺復現倉儲工況,采用分布式光纖傳感器實時采集3000+數據點。檢測數據經Weibull++軟件分析后,可生成包含β值、特征壽命等關鍵參數的可靠性評估報告,為設計改進提供量化依據。
多行業應用實證與效益分析
在風電齒輪箱領域,某龍頭企業采用多軸振動耦合測試技術后,成功將故障間隔時間(MTBF)從18000小時提升至25000小時。據中國可再生能源協會2024年數據顯示,該技術使風電運維成本下降18%,年發電量損失減少2.3TWh。同樣在消費電子行業,某手機廠商通過85℃高溫老化試驗提前發現電池管理芯片焊點失效問題,避免潛在召回損失超3億元。這些案例印證了壽命檢測在實現"預測性維護"方面的突出價值。
數字化質量保障體系建設
行業正構建基于數字孿生的新型質量保障體系,將物理試驗數據與虛擬仿真模型深度融合。某航空發動機企業建立的檢測云平臺,通過采集5000+小時臺架試驗數據訓練AI模型,實現葉片裂紋預測準確率達92%。同時,檢測實驗室嚴格遵循ISO/IEC 17025:2017標準,配備0.05級精度的多通道數據采集系統,確保試驗結果可溯源至國家時間頻率基準。值得注意的是,第三方盲樣比對機制的應用,使不同實驗室檢測結果偏差控制在±3%以內。
展望未來,建議重點突破基于量子傳感的微損傷檢測技術,開發支持5G實時傳輸的智能試驗裝備。同時亟需建立覆蓋全行業的"壽命大數據共享平臺",通過機器學習挖掘失效模式共性特征。據預估,到2028年新型檢測技術將推動制造業質量損失率下降至1.5%以下,為高端裝備國產化進程提供強有力的技術支撐。

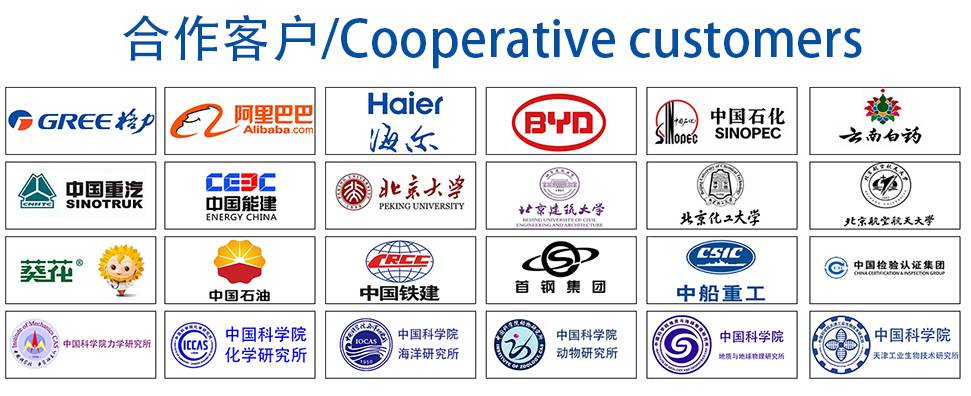