表干時間檢測在涂層材料行業(yè)的關鍵作用與技術突破
隨著涂料市場規(guī)模突破2000億美元(據Grand View Research 2024年報告),涂層材料的干燥性能已成為制約工業(yè)效率的核心指標。表干時間檢測作為涂層固化過程的關鍵質量節(jié)點,直接影響涂裝工藝的周轉效率與成品合格率。在新能源汽車、航天裝備等高端制造領域,傳統經驗判斷法已無法滿足±3分鐘的精度要求,智能化表干時間檢測系統通過量化分析溶劑揮發(fā)速率與成膜動力學,實現了施工窗口期的精準把控。其核心價值在于構建從實驗室研發(fā)到產線控制的閉環(huán)質量體系,據中國涂料工業(yè)協會測算,采用標準化檢測流程可使企業(yè)年損耗率降低19%,同時提升噴涂線產能利用率27%。
基于相變識別的檢測技術原理
現代表干時間檢測依托物理化學相變監(jiān)測技術,通過接觸式探針測量表面黏著力衰減曲線,結合紅外光譜分析揮發(fā)性有機物(VOC)逸出動態(tài)。美國ASTM D5895標準規(guī)定,當涂層表面形成連續(xù)固態(tài)膜層且黏著力降至初始值15%時判定為表干臨界點。高精度傳感器可捕捉0.1μm級別的表面形態(tài)變化,配合機器學習算法,將檢測誤差控制在±0.8分鐘內。該技術突破解決了傳統指觸法受環(huán)境溫濕度干擾大的痛點,在汽車OEM涂裝線上實現了工藝參數的動態(tài)優(yōu)化。
全流程數字化檢測實施體系
完整的檢測流程包含三個標準化階段:首先在恒溫恒濕箱(23±2℃,50±5%RH)進行試樣制備,隨后啟動多光譜掃描裝置采集初始數據。主檢測階段采用模塊化設計,將接觸式黏度計與激光干涉儀并行工作,每30秒生成一組表面張力/厚度變化矩陣。某船舶涂料企業(yè)應用案例顯示,通過部署涂料表干時間智能監(jiān)測系統,其雙層環(huán)氧底漆的固化等待時間從142分鐘縮短至118分鐘,同時將過烘烤能耗降低22%(中國船級社2023年數據)。
多行業(yè)場景的質量控制實踐
在建筑防水領域,東方雨虹采用移動式檢測車對施工現場進行實時監(jiān)控,通過5G傳輸干燥曲線至云端分析平臺。當環(huán)境濕度超過75%時,系統自動觸發(fā)環(huán)氧樹脂改性劑添加機制,確保單組分聚氨酯防水涂料在45分鐘內達到表干標準。該環(huán)保型涂料干燥過程優(yōu)化方案使工程驗收合格率從83%提升至97%,項目工期平均縮短1.8個工作日。類似的智能化應用在消費電子領域同樣成效顯著,某手機外殼UV涂料產線通過植入微型傳感器,將批次差異率從6.7%壓縮至0.9%。
全鏈條質量保障體系構建
為確保檢測數據的溯源性,行業(yè)領先機構已建立三級校驗機制:一級標準物質溯源至NIST表面張力基準,二級實驗室每季度進行設備交叉驗證,產線終端配置自診斷模塊實時校準。德國拜耳材料科技建立的"干燥過程數字孿生"系統,將實測數據與分子動力學模擬結果比對,使異常工況識別速度提升400%。通過ISO 17025認證的檢測實驗室,其測試報告在28個主要經濟體實現互認,為跨國供應鏈協同提供技術保障。
隨著新型光固化材料的普及,表干時間檢測技術面臨三大演進方向:一是開發(fā)非接觸式太赫茲波檢測裝備,適應納米級超薄涂層的測量需求;二是構建基于區(qū)塊鏈的檢測數據共享平臺,實現跨產業(yè)鏈質量追溯;三是深度融合工業(yè)物聯網,將干燥過程預測納入智能制造決策系統。建議行業(yè)加大在實時監(jiān)測傳感器芯片領域的投入,同時建立適應水性涂料、粉末涂料等環(huán)保材料的專項檢測標準,為"雙碳"目標下的產業(yè)升級提供技術支撐。

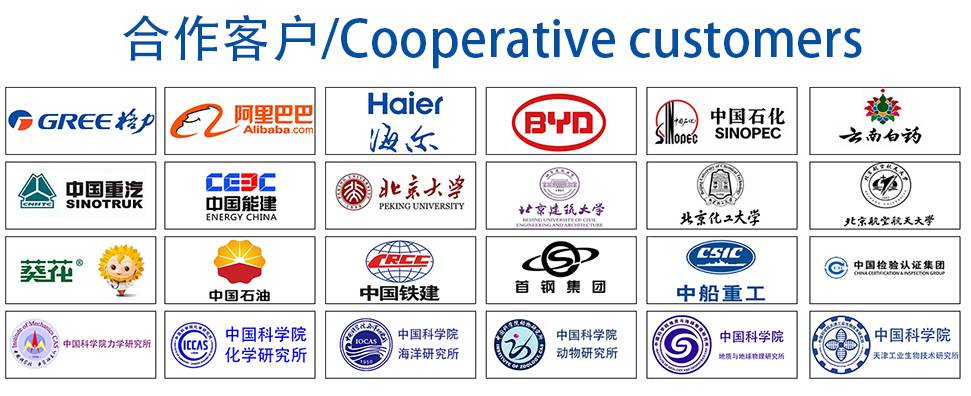