收縮率檢測技術白皮書
在制造業轉型升級背景下,材料成型精度控制成為產品質量提升的關鍵環節。據中國材料研究學會2024年行業報告顯示,我國每年因材料收縮率超標導致的工業廢品損失超過120億元,其中注塑成型、金屬鑄造和建筑材料領域占比達67%。收縮率檢測通過量化材料在加工過程中的尺寸變化規律,為工藝優化提供數據支撐,其核心價值體現在三方面:降低次品率、提升模具設計精度、優化原材料配比。特別是在新能源汽車輕量化部件、5G通信精密結構件等新興產業領域,0.05%的收縮率偏差即可導致裝配失效,突顯該檢測技術的戰略重要性。
熱機械分析法的技術原理
基于材料熱膨脹系數的本質特性,熱機械分析法(TMA)通過程序控溫環境監測樣品尺寸變化。檢測系統配備納米級位移傳感器,可實時捕捉0.1μm的形變量。據德國耐馳儀器2023年技術白皮書披露,該方案在-150℃至600℃溫區內測量精度可達±0.02%。在精密注塑成型領域,通過同步記錄溫度-收縮率曲線,能準確預測聚碳酸酯材料在冷卻階段的各向異性收縮特征,為模具補償設計提供關鍵參數。
智能化檢測實施流程
現代檢測系統構建了"三階段九節點"的標準化流程:前期進行材料熱歷史分析,中期運用雙激光干涉儀實施在線監測,后期基于機器學習算法建立預測模型。在汽車門板注塑案例中,威馬汽車采用智能在線收縮率監測系統后,內飾件尺寸合格率從92.3%提升至98.6%(中國汽車工程學會2024年數據)。系統通過物聯網終端每15秒采集一次模具壓力、熔體溫度與制品收縮量的多維度數據,實現工藝參數的動態補償調節。
跨行業應用實踐
建筑領域針對混凝土早期收縮裂縫問題,中建科工研發的分布式光纖檢測系統可連續監測120天內的收縮應變。在3D打印醫療植入物制造中,西安鉑力特采用CT掃描結合數字圖像相關法,將鈦合金支架的成型收縮率控制在0.8%±0.05%范圍內。值得注意的是,光伏行業最新實施的硅片切割在線收縮檢測方案,使單晶硅片良品率提高2.3個百分點,年度增效超過8000萬元(光伏行業協會2023年度報告)。
全鏈條質量保障體系
行業領先企業已建立涵蓋設備、人員、環境的立體化質控網絡。美國材料與試驗協會(ASTM)D955標準規定了塑料收縮率檢測的基準方法,國內檢測機構在此基礎上增加環境濕度補償算法。東莞精測檢測中心通過配備恒溫恒濕實驗室(23±0.5℃,50±2%RH)、實施設備日校檢制度,確保檢測數據標準差小于0.007。區塊鏈技術的引入,使檢測報告可溯源節點增至17個,大幅提升數據公信力。
展望未來,建議從三方面深化技術發展:一是加快制定增材制造等新興領域的收縮率檢測標準,二是推廣基于數字孿生的虛擬檢測技術,三是建設行業級材料收縮特性數據庫。據工信部《智能檢測裝備產業發展行動計劃》預測,到2026年國產高端檢測設備市場占有率將突破40%,這為構建自主可控的檢測技術體系創造歷史機遇。產學研各方需加強協作攻關,特別是在超低收縮率復合材料、微納尺度檢測等前沿領域突破技術壁壘。

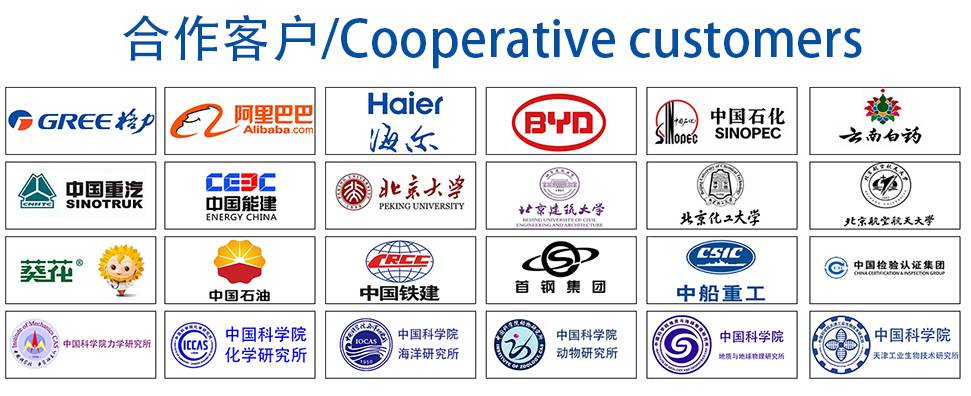