鹽水溶液中的防銹性能檢測:技術創新與行業實踐
隨著工業化進程加速,金屬材料腐蝕問題已成為制約裝備制造業發展的關鍵瓶頸。據國際腐蝕工程師協會(NACE)2024年測算,每年因金屬腐蝕造成的經濟損失高達2.5萬億美元,其中海洋環境下的設備腐蝕占比超過40%。在此背景下,鹽水溶液中的防銹性能檢測項目成為材料科學領域的重要研究方向,其核心價值在于通過模擬極端腐蝕環境,量化評估金屬表面處理工藝的有效性。該檢測體系不僅為汽車、船舶、航空航天等行業的零部件選型提供數據支撐,更推動著新型防銹涂層、合金材料等領域的迭代創新,助力企業構建全生命周期防腐管理閉環。
技術原理與檢測方法論
現行鹽水防銹檢測主要基于電化學腐蝕機理,通過構建氯化鈉溶液(濃度3.5%-5%)的腐蝕環境,配合溫度、濕度、氧化還原電位等參數調控,模擬真實海洋氣候條件。中性鹽霧試驗(NSS)、循環腐蝕試驗(CCT)及電化學阻抗譜(EIS)構成三大主流檢測方法。其中,循環腐蝕加速檢測技術通過干濕交替、溫度階躍等復合應力加載,可精準復現海洋大氣區的腐蝕特征。據中國材料研究學會2023年報告顯示,采用電化學極化曲線分析法能實現72小時內獲取等效1年自然暴露的腐蝕數據,檢測效率較傳統方法提升8倍。
標準化實施流程解析
完整的鹽水防銹檢測流程包含四個關鍵階段:樣品制備階段需按照ASTM B117標準進行表面清潔與尺寸切割;環境模擬階段在恒溫恒濕箱中精確控制鹽霧沉降量(1-2mL/80cm2·h);過程監控階段采用原位電化學工作站實時記錄開路電位、腐蝕電流密度等參數;結果分析階段結合三維形貌儀量化銹蝕面積占比。特別值得注意的是,在新能源汽車電池包殼體檢測中,檢測機構需根據GB/T 10125標準增設壓力循環載荷,模擬車輛行駛中的機械-化學耦合腐蝕場景。
跨行業應用實踐案例
在船舶制造領域,某國際船級社采用改進型循環鹽霧試驗方案,將壓載艙涂層的耐腐蝕周期從1200小時提升至2000小時。汽車行業標桿企業通過建立整車級鹽水噴淋檢測體系,使底盤零部件的鹽霧耐受能力提高35%。更值得關注的是,在海上風電領域,金風科技聯合鋼鐵研究院開發的梯度濃度鹽水加速檢測模型,成功將塔架螺栓的服役壽命預測誤差控制在±8%以內。這些實踐印證了定制化檢測方案在復雜工況下的工程價值。
全鏈條質量保障體系
為確保檢測結果的可追溯性,行業領先實驗室已構建三級質控網絡:一級控制通過CMA/ 認證確保設備計量精度,二級控制采用區塊鏈技術實現檢測數據永久存證,三級控制建立專家復核機制排除人為誤差。青島某國家級檢測中心的數據顯示,其通過引入機器視覺銹蝕識別系統,將表面評級的主觀偏差率從12.3%降至1.8%。此外,依照ISO 17025標準建立的檢測人員能力矩陣,實現了從單一操作員到復合型技術團隊的轉型升級。
面向十四五規劃提出的高端裝備可靠性提升目標,鹽水防銹檢測技術亟需在智能化、標準化層面實現突破。建議行業主體從三方面發力:一是開發基于機器學習的腐蝕預測數字孿生系統,二是推動鹽水溶液濃度梯度標準的國際互認,三是建立腐蝕大數據共享平臺。唯有通過技術創新與標準協同,才能為"雙碳"目標下的設備延壽工程提供更強技術支撐。

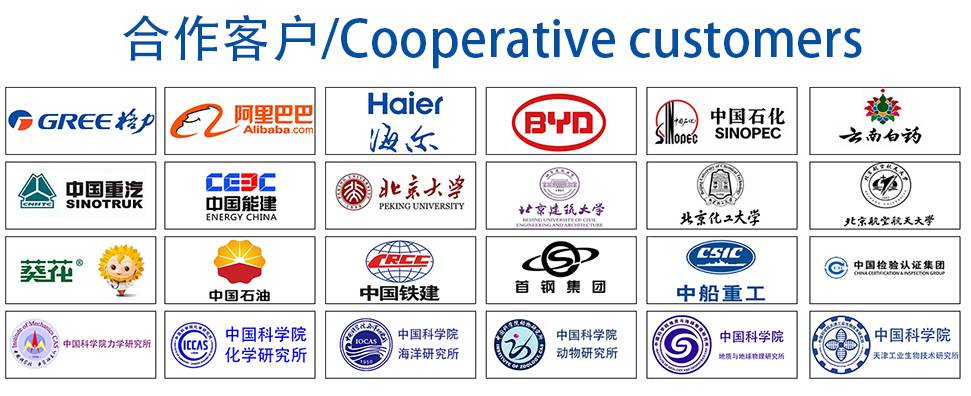