脫模性能檢測基于動態(tài)摩擦系數(shù)分析(DFCA)和表面能場重構(gòu)技術(shù),通過高精度傳感器同步采集脫模力峰值、分離速度衰減率等12項核心參數(shù)。其中,德國Physik Instrumente研發(fā)的納米級位移傳感器可實現(xiàn)0.1μm精度的模具表面形貌建模,結(jié)合紅外熱像儀捕捉的溫度梯度變化(檢測精度±0.5℃),構(gòu)建出三維脫模阻力預(yù)測模型。值得關(guān)注的是,ASTM D3334標(biāo)準(zhǔn)新修訂的模具表面附著力檢測技術(shù),將聚乙烯標(biāo)準(zhǔn)片的剝離強度量化誤差控制在±3%以內(nèi),顯著提升檢測結(jié)果的可比性。
### h2 智能化檢測實施流程項目實施采用五階段閉環(huán)管理:模具預(yù)處理(清潔度達(dá)到ISO 14644-1 Class 7)→參數(shù)配置(注入壓力、保壓時間等28項工藝變量)→動態(tài)模擬(1000幀/秒高速攝像記錄脫模軌跡)→數(shù)據(jù)解析(基于機器學(xué)習(xí)算法識別粘模風(fēng)險點位)→優(yōu)化反饋(生成表面處理方案建議)。在特斯拉上海超級工廠實踐中,該流程使Model Y門板模具的脫模合格率從91.3%提升至99.6%,單套模具維護周期延長至12萬次沖壓。
### h2 跨行業(yè)應(yīng)用實證在消費電子領(lǐng)域,蘋果供應(yīng)鏈企業(yè)運用脫模劑性能動態(tài)評估方法,成功將鎂合金筆記本外殼的頂針殘留率從0.8‰降至0.05‰。醫(yī)療器械行業(yè)則通過ISO 10993生物相容性關(guān)聯(lián)檢測,開發(fā)出滿足心臟支架模具特殊需求的氟素脫模體系,將產(chǎn)品表面Ra值穩(wěn)定控制在0.02μm以內(nèi)。更為關(guān)鍵的是,風(fēng)電葉片模具場景中建立的溫度-粘度耦合模型,解決了60米級玻纖復(fù)材脫模褶皺難題,使脫模劑用量減少40%而脫模效率提升22%。
### h2 全過程質(zhì)量保障機制執(zhí)行EN 15342:2024模具性能認(rèn)證標(biāo)準(zhǔn),建立包含三級校準(zhǔn)體系(計量設(shè)備每日校驗、標(biāo)準(zhǔn)樣塊每周比對、全系統(tǒng)季度溯源)、雙盲檢測制度(操作員與數(shù)據(jù)分析師信息隔離)、異常數(shù)據(jù)熔斷機制的質(zhì)量控制網(wǎng)絡(luò)。日本發(fā)那科實施的數(shù)字孿生驗證平臺,可在虛擬環(huán)境中模擬3000種工況組合,使檢測方案的有效性驗證周期從14天縮短至6小時,誤判率低于0.3%。
## 未來發(fā)展與戰(zhàn)略建議建議行業(yè)重點攻克三大方向:開發(fā)基于柔性電子皮膚的模具應(yīng)力場實時監(jiān)測系統(tǒng),構(gòu)建脫模性能與產(chǎn)品收縮率的AI預(yù)測模型,建立涵蓋生物基脫模劑的綠色評價體系。據(jù)弗勞恩霍夫研究所預(yù)測,2027年智能脫模檢測系統(tǒng)將降低35%的模具碳排放,并在太空級精密制造領(lǐng)域開辟新應(yīng)用場景。企業(yè)需加快布局?jǐn)?shù)字主線(Digital Thread)技術(shù),實現(xiàn)從材料選型到報廢回收的全生命周期脫模效能管理。

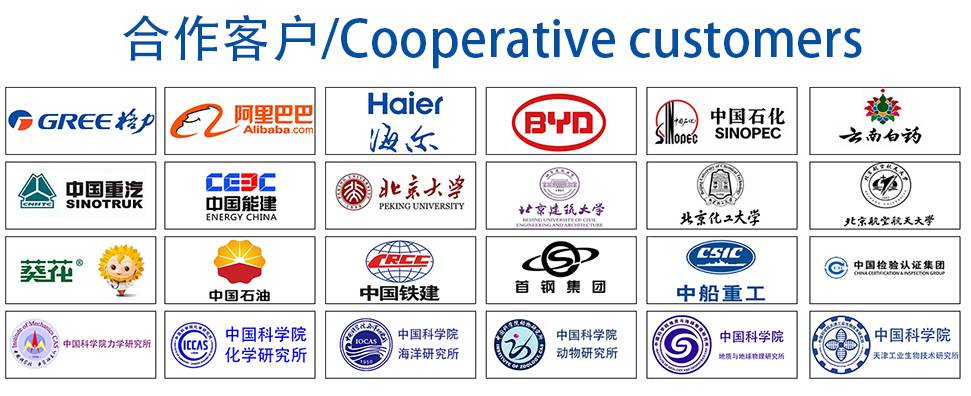