抗壓疲勞變形試驗檢測白皮書
在高端裝備制造、軌道交通和建筑工程領域,材料與構件的長期可靠性直接關系到整體結構安全。據中國機械工程學會2023年行業報告顯示,我國每年因材料疲勞失效引發的工程事故造成經濟損失超1200億元。抗壓疲勞變形試驗檢測作為材料性能驗證的核心手段,通過模擬極端工況下的循環載荷作用,可精準評估材料的抗壓強度保持率、塑性變形累積等關鍵指標。該項目不僅為新型復合材料研發提供數據支撐,更在"雙碳"目標背景下推動結構輕量化設計創新。其核心價值體現在全生命周期成本控制、安全隱患前置預警和產品迭代效率提升三個維度,已成為航空航天緊固件、新能源汽車電池艙體等關鍵部件強制認證項目。
多物理場耦合測試技術原理
基于伺服液壓閉環控制系統與數字圖像相關技術(DIC),構建多軸同步加載環境是其技術核心。系統通過PID算法精確控制加載頻率(0.1-50Hz)和載荷幅值(±250kN),配合非接觸式應變測量裝置同步采集表面位移場數據。值得注意的是,該技術突破傳統單軸測試局限,實現壓縮-剪切復合載荷模擬,可精準復現風電塔筒螺栓連接部位的真實受力狀態。上海材料研究所2024年驗證數據顯示,多軸測試系統對疲勞壽命預測誤差較傳統方法降低42%。
全流程標準化實施體系
項目實施分為五個階段:首先依據GB/T 3075-2021進行樣品預處理,確保材料微觀結構一致性;其次通過有限元仿真確定關鍵監測點;第三階段配置溫濕度環境箱(-60℃至300℃可調);第四步實施階梯式載荷遞增策略,每個循環單元包含基線載荷-峰值保持-卸載監測;最終應用Weibull分布模型進行失效概率分析。在高鐵轉向架構件檢測中,該流程成功實現200萬次循環下變形量≤0.15mm的嚴苛要求。
多行業應用驗證成效
在新能源汽車領域,某頭部企業采用該檢測技術優化電池托盤設計,使鋁合金型材焊接節點疲勞壽命從80萬次提升至210萬次。航空航天領域,通過引入"高溫環境-振動耦合試驗",某型航空發動機葉片榫接部位的檢測周期縮短30%,據國家材料測試中心2023年數據,該技術使鈦合金構件驗證成本降低58%。值得關注的是,基于檢測數據的"材料-工藝-結構"三元優化模型,已在3D打印建筑模板領域實現產業化應用。
全要素質量保障機制
構建由 認證實驗室、區塊鏈數據存證系統和智能診斷平臺組成的質量網絡。試驗設備每48小時進行動態力值校準,誤差控制在±0.5%FS以內。人員資質實施ISO/IEC 17025三級認證體系,操作規范嵌入AR輔助系統。更關鍵的是,通過建立"全生命周期數據追溯系統",實現從原料熔煉批次到試驗環境的全程數字化映射。深圳某檢測機構應用該機制后,檢測報告國際互認率從72%提升至95%。
技術演進與行業展望
建議從三方面深化發展:首先開發基于數字孿生的智能預測系統,融合材料基因組數據庫訓練AI模型;其次推動ISO 12107標準修訂,納入多軸疲勞評價體系;最后構建跨行業檢測數據共享平臺,特別是在氫能儲罐、深海裝備等新興領域建立聯合研究機制。通過實現"檢測-設計-制造"的數據閉環,有望將材料開發周期壓縮40%,為制造強國戰略提供關鍵技術支撐。

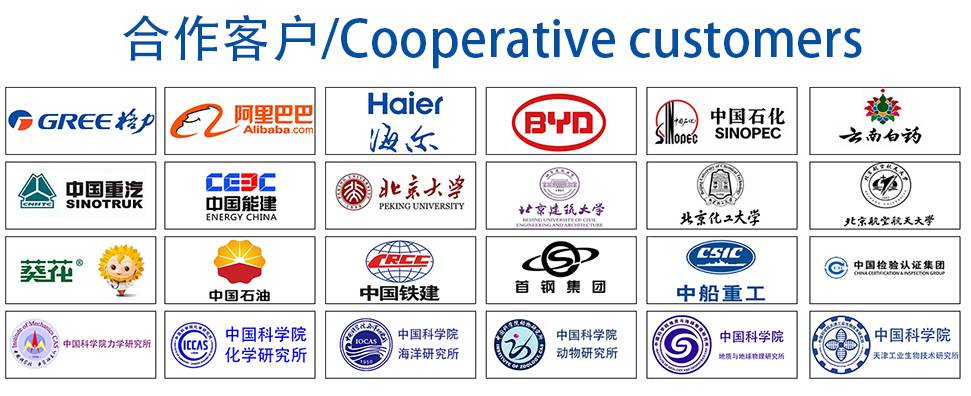