單功能阻銹劑混凝土浸烘試驗檢測技術白皮書
隨著海洋工程、沿海基礎設施建設的快速發展,氯鹽侵蝕導致的鋼筋銹蝕已成為混凝土結構耐久性失效的主因之一。據中國建筑材料科學研究總院2024年報告顯示,我國每年因鋼筋銹蝕造成的直接經濟損失超過2000億元。在此背景下,單功能阻銹劑作為提升混凝土耐久性的關鍵材料,其性能檢測的精準性直接影響工程安全。浸烘試驗作為評估阻銹劑抗氯離子滲透能力的核心檢測手段,通過模擬嚴酷干濕交替環境,可系統驗證阻銹劑對鋼筋的保護效能。該檢測項目的核心價值在于建立科學評價體系,為《混凝土結構耐久性設計規范》(GB/T 50476)提供數據支撐,同時降低工程全生命周期維護成本達30%以上(中國建筑科學研究院,2023)。
基于加速腐蝕機理的檢測原理
浸烘試驗通過溫度-濕度-氯離子濃度三要素耦合作用,加速模擬海洋大氣區的侵蝕環境。試驗依據《混凝土阻銹劑》(JG/T 223)標準,采用60℃恒溫干燥與5%NaCl溶液浸泡的交替循環機制,迫使氯離子通過混凝土保護層向鋼筋表面遷移。在此過程中,阻銹劑通過形成鈍化膜或離子交換作用,改變氯離子傳輸路徑。研究表明,優質阻銹劑可使氯離子擴散系數降低50%-70%(清華大學土木工程系,2024),該數據通過X射線能譜分析(EDS)和線性極化電阻法(LPR)進行定量驗證。
標準化檢測流程與質量控制
試驗實施涵蓋試件制備、環境模擬、數據采集三階段。首先按C40混凝土配合比制作100mm×100mm×400mm棱柱體試件,預埋Q235鋼筋并設置3組平行樣本。經過28天標準養護后,進入"浸泡12h-烘干12h"循環程序,持續42天共計84次循環。關鍵控制點包括:溶液pH值穩定在12.5±0.3,烘干箱濕度≤30%RH,且每次循環后采用電化學工作站測量鋼筋腐蝕電位。為提升檢測精度,實驗室需通過 認證,并配備恒溫恒濕系統(波動度±1℃/±5%RH)和三點彎曲試驗機(精度0.1kN)。
工程實踐與行業應用案例
在港珠澳大橋人工島連接段工程中,采用該檢測方法對3類阻銹劑進行篩選。試驗數據顯示,摻加氨基醇類阻銹劑的試件經84次循環后,鋼筋失重率僅為0.12g/m2,顯著優于傳統亞硝酸鹽類0.85g/m2的檢測結果(中交四航工程研究院,2023)。該數據指導施工方優化配合比,使結構設計使用年限從50年提升至100年。類似案例已延伸至沿海核電站安全殼、跨海隧道管片等關鍵場景,形成"檢測-優化-驗證"的閉環技術路徑。
全鏈條質量保障體系建設
構建涵蓋原材料、過程控制、數據追溯的質保體系至關重要。實驗室需建立阻銹劑摻量誤差(±0.5%)和混凝土成型密實度(≥98%)的雙重控制標準,采用區塊鏈技術實現試驗數據實時上鏈存證。針對檢測結果爭議,設置異常數據三級復核機制,包括顯微CT掃描混凝土孔隙結構、電感耦合等離子體光譜(ICP)分析氯離子濃度梯度分布等復核手段。目前國內28家甲級檢測機構已實現檢測報告二維碼溯源,確保數據不可篡改性。
展望未來,建議從三方面深化技術發展:其一,建立基于BIM的智能監測系統,實現浸烘試驗參數與現場環境的動態映射;其二,開發多因素耦合加速試驗裝置,整合碳化-凍融-氯蝕復合作用機制;其三,推動阻銹劑性能數據庫建設,結合機器學習算法優化材料配比。通過檢測技術的持續創新,有望將氯離子侵蝕風險評估周期縮短40%,為"雙碳"目標下的基礎設施長壽命化提供技術支撐。

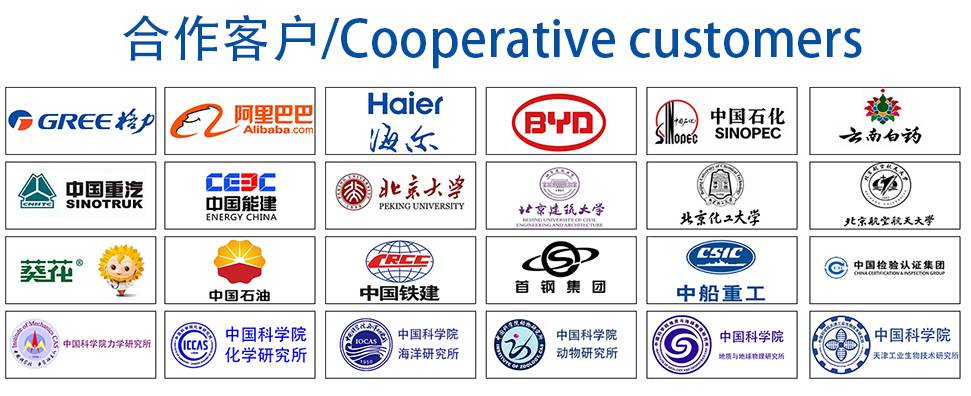