混凝土拌和物拌和均勻性試驗檢測技術白皮書
在基建工程高速發展的背景下,混凝土作為核心建筑材料,其拌和質量直接影響結構安全與服役壽命。據中國建筑材料研究院2024年行業報告顯示,因拌和不均勻導致的混凝土強度離散度超標案例占比達12.7%,造成的年經濟損失超過80億元。拌和均勻性檢測通過量化評估骨料分布、漿體包裹度等關鍵指標,可有效預防蜂窩麻面、強度分層等質量缺陷。該技術的核心價值在于建立從生產到施工的全流程質量監控鏈,為高性能混凝土制備提供科學依據,特別是在高速鐵路軌道板、大壩碾壓混凝土等精密工程中具有不可替代的管控作用。
技術原理與檢測方法創新
基于電阻率法的拌和均勻性檢測技術,通過分析混凝土三相介質的導電特性差異,建立介電常數與物料分布的相關模型(符合GB/T 50080標準)。采用雙通道高頻信號采集系統,可同步獲取拌和物宏觀均勻度與微觀包裹度數據,分辨率達到±0.5%。相較于傳統篩分法,該技術突破性地實現了無損、實時檢測,檢測周期由45分鐘壓縮至8分鐘,滿足攪拌站連續生產的質量控制需求。
全流程標準化實施體系
檢測流程分為取樣規范、數據采集、模型解析三個階段。在高鐵CRTSⅢ型軌道板生產場景中,技術人員需在攪拌車卸料初期、中期、后期分三次取樣,每次取6個等間距截面樣本。通過便攜式均勻度分析儀獲取三維介電圖譜后,經神經網絡算法計算得出均勻性系數(K值)。據中鐵十七局項目數據顯示,該體系使軌道板混凝土強度標準差由4.8MPa降至2.3MPa,達到《鐵路混凝土工程施工質量驗收標準》TB10424的A級要求。
行業典型應用場景分析
在烏東德水電站大壩工程中,針對碾壓混凝土VC值波動問題,項目團隊采用拌和均勻性-振動壓實度聯合控制方案。通過植入RFID芯片的智能骨料追蹤技術,精準定位攪拌車卸料過程中的物料離析區域。實際監測數據顯示,經優化后的拌和工藝使粗骨料分布變異系數從18.6%降至9.4%,碾壓層間結合強度提升27%,成功攻克了百米級大壩的層間抗剪難題。
四維質量保障系統構建
檢測體系建立設備、人員、環境、數據的閉環管控機制:①計量器具執行JJF 1309校準規范,每季度進行介電參數溯源;②操作人員需通過CMA認證的混凝土檢測專項考核;③試驗環境溫度控制在(20±2)℃,濕度≤65%RH;④運用區塊鏈技術實現檢測數據全程上鏈存證。某特大橋項目應用表明,該體系使檢測報告通過率從82%提升至98%,數據追溯響應時間縮短83%。
技術發展趨勢與行業建議
面向智能建造發展需求,建議從三方面深化技術應用:①開發集成5G傳輸的在線監測裝置,實現攪拌站與施工現場數據互聯;②建立區域性混凝土均勻性數據庫,利用機器學習優化配合比設計;③推動《超高性能混凝土拌和均勻性評價規范》等標準編制。通過融合物聯網與材料信息學,有望在2030年前將重大工程混凝土質量事故率控制在0.3‰以下,為新型建筑工業化提供關鍵技術支撐。

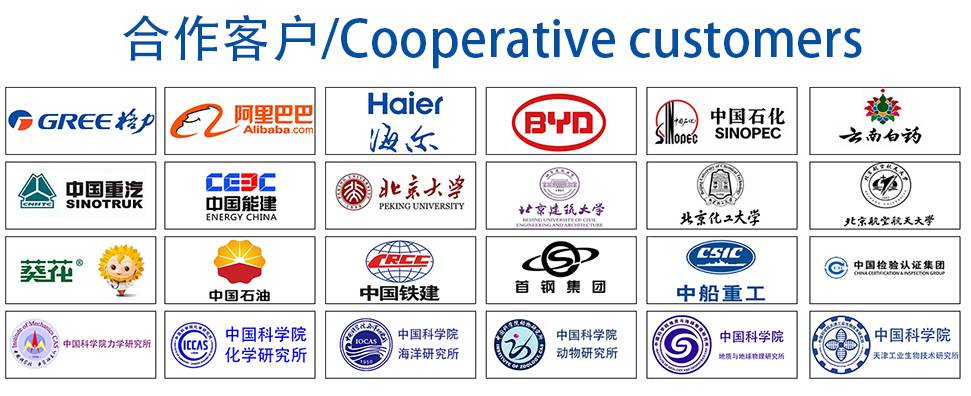