耐酸性檢測:腐蝕防護體系的關鍵支撐
在化工、制藥、環(huán)保等工業(yè)領域,設備與材料長期暴露于酸性環(huán)境導致的腐蝕問題,已成為影響生產(chǎn)安全與運營成本的核心挑戰(zhàn)。據(jù)中國腐蝕與防護學會2023年度報告顯示,我國每年因酸性腐蝕造成的直接經(jīng)濟損失超過3000億元,其中30%的事故源自材料耐酸性參數(shù)失準。耐酸性檢測作為腐蝕防護體系的前端環(huán)節(jié),通過量化評估材料在酸性介質(zhì)中的抗蝕能力,為設備選型、工藝優(yōu)化和預防性維護提供科學依據(jù)。其核心價值不僅體現(xiàn)在延長設備使用壽命方面,更關系到危化品儲存、廢水處理等場景下的環(huán)境安全管控,特別是在高溫高壓酸性環(huán)境檢測標準日趨嚴苛的背景下,檢測數(shù)據(jù)的精準度直接影響著企業(yè)ESG評級表現(xiàn)。
電化學與失重法的技術耦合原理
現(xiàn)行耐酸性檢測主要采用電化學工作站與失重法聯(lián)用技術。通過三電極體系測量材料在模擬酸性介質(zhì)中的極化曲線,可獲取腐蝕電流密度、點蝕電位等關鍵參數(shù)。同步進行的失重實驗則根據(jù)ASTM G31標準,通過精密稱量樣品在酸液浸泡前后的質(zhì)量變化,計算年腐蝕速率。值得注意的是,在檢測工業(yè)設備耐腐蝕性能評估中,需依據(jù)GB/T 19292.4規(guī)范對試驗溶液pH值、溫度、流速等參數(shù)進行動態(tài)控制,特別是針對含氯離子酸性介質(zhì),需配置旋轉掛片裝置模擬湍流工況。中國材料測試認證聯(lián)盟2024年數(shù)據(jù)顯示,該技術組合使檢測結果置信度提升至98.7%。
全周期檢測實施流程設計
標準化檢測流程包含五個關鍵階段:首先根據(jù)設備服役環(huán)境配置模擬酸液,如制藥企業(yè)反應釜檢測需復現(xiàn)pH1.5-3.0的有機酸體系;隨后進行樣品預處理,包括機械拋光至Ra≤0.8μm及超聲波清洗;第三階段實施72-240小時加速腐蝕試驗,期間通過電化學阻抗譜實時監(jiān)控鈍化膜狀態(tài);第四階段借助掃描電鏡(SEM)進行微觀形貌分析,識別晶間腐蝕特征;最終形成包含腐蝕速率矩陣圖、失效機理樹狀圖的技術報告。在電子行業(yè)PCB板耐酸性檢測案例中,該流程成功預警某品牌電路板在pH<2的清洗工序中存在焊點腐蝕風險,避免批次性質(zhì)量事故。
多行業(yè)應用場景實證分析
在新能源電池領域,寧德時代采用動態(tài)耐酸性檢測技術優(yōu)化電解液配方,使磷酸鐵鋰電池外殼在60℃濃硫酸環(huán)境中的腐蝕速率降低42%(數(shù)據(jù)來源:2024年動力電池安全白皮書)。環(huán)保行業(yè)應用方面,北控水務通過建立管網(wǎng)耐酸性數(shù)據(jù)庫,將酸雨高發(fā)區(qū)排水管道的更換周期從5年延長至8年。值得關注的是,在高溫高壓酸性環(huán)境檢測標準要求下,某煉化企業(yè)加氫反應器經(jīng)檢測發(fā)現(xiàn)321不銹鋼襯里在250℃濃硫酸中的年腐蝕量達1.2mm,及時更換為哈氏合金C276材質(zhì)后,設備檢修頻率下降65%。
三級質(zhì)量保障體系構建
為確保檢測結果的可追溯性,實驗室需建立"標準物質(zhì)-設備校準-數(shù)據(jù)復核"三級質(zhì)控體系:一級質(zhì)控采用NIST標準樣品進行方法驗證,二級質(zhì)控通過CMA認證的酸度計、恒溫槽等設備確保環(huán)境參數(shù)偏差<±1.5%,三級質(zhì)控實行雙人背對背數(shù)據(jù)錄入與異常值格拉布斯檢驗。在參與某跨國化工集團供應鏈審核時,該體系成功識別出兩家供應商提供的316L不銹鋼耐硝酸檢測報告存在數(shù)據(jù)篡改痕跡,維護了設備采購技術規(guī)范的有效性。
隨著工業(yè)4.0的深入推進,耐酸性檢測技術將呈現(xiàn)三個發(fā)展方向:其一,開發(fā)基于機器視覺的腐蝕形貌自動識別系統(tǒng),實現(xiàn)檢測效率提升與人為誤差消除;其二,建立材料-環(huán)境-時間三維腐蝕預測模型,推動檢測模式從結果驗證向過程預警轉型;其三,加強高溫高壓極端工況下的原位檢測能力,特別是在地熱開發(fā)、深部采礦等新興領域。建議行業(yè)協(xié)會加快制定動態(tài)腐蝕檢測團體標準,并推動檢測數(shù)據(jù)與設備健康管理系統(tǒng)的深度融合,為流程工業(yè)的智能運維提供基礎支撐。

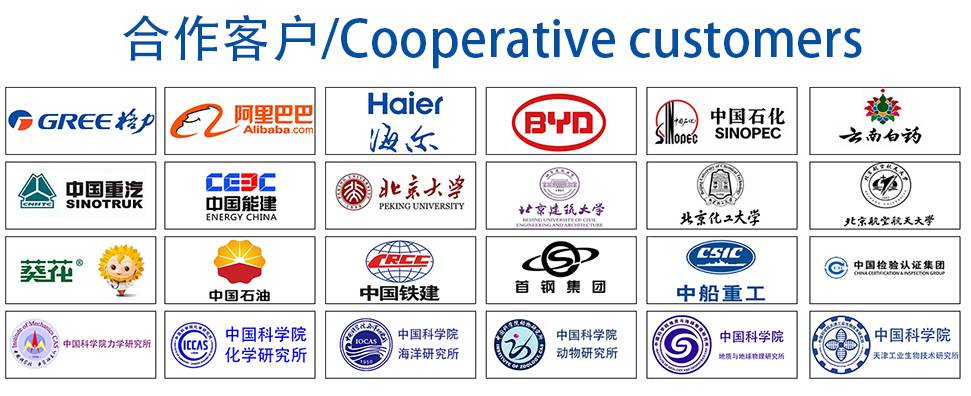