抗彎荷載檢測在工程安全評估中的關鍵作用
在建筑工程與制造業高速發展的背景下,結構安全性已成為行業核心關切。據中國建筑科學研究院2024年數據顯示,國內每年因材料力學性能不足導致的工程事故損失超120億元,其中32%與抗彎性能缺陷直接相關。抗彎荷載檢測通過量化評估構件在彎矩作用下的承載能力與變形特性,為鋼結構廠房、橋梁工程及裝備制造領域提供關鍵安全數據。該技術不僅可預防建筑坍塌等重大事故,還能優化結構設計降低20%-35%的冗余建材用量,實現安全性與經濟性的雙重突破。尤其在裝配式建筑普及和風電葉片大型化趨勢下,其核心價值體現在全生命周期質量管控體系的構建。
多模態傳感融合檢測技術原理
基于應變-位移耦合理論,現代抗彎荷載檢測系統采用分布式光纖傳感與數字圖像相關技術(DIC)的協同工作機制。通過布設在試件表面的400-1200個微應變計,配合10μm級精度的三維光學測量,可實時捕獲荷載作用下試件的應變場分布與撓度變化特征。值得關注的是,基于機器學習的荷載分布模擬技術突破傳統點式測量的局限,實現全場應力的可視化重構。中國計量院驗證數據顯示,該技術體系可將彎曲剛度測算誤差控制在±1.8%以內,顯著優于行業標準要求的±5%閾值。
全流程數字化檢測實施方案
標準化檢測流程涵蓋三個階段:預處理階段通過三維激光掃描建立試件數字孿生模型,智能布點算法優化傳感器網絡布局;加載階段采用電液伺服控制系統實現0.1kN/s的精準荷載施加,同步采集2000Hz高頻動態數據;后處理階段通過云平臺進行大數據分析,自動生成包含極限荷載、塑性變形拐點等28項參數的檢測報告。某高速鐵路箱梁檢測項目實踐表明,該流程使單件檢測效率提升40%,同時通過區塊鏈技術實現檢測數據的不可篡改存證。
典型行業應用場景解析
在風電領域,某5MW風機葉片檢測項目采用階梯式加載方案,成功定位葉根部位0.3mm的微裂紋擴展,避免潛在斷裂風險。橋梁工程中,杭州灣跨海大橋定期檢測通過布設1600個監測點,建立彎扭組合荷載下的剩余壽命預測模型。更為典型的是航空制造業,C919機翼靜力試驗采用多點協調加載系統,在140%設計荷載下驗證結構完整性,其檢測數據精度達到ASME標準三級認證要求。
四維質量保障體系構建
行業領先企業已建立涵蓋"標準-人員-設備-方法"的全要素質控網絡。檢測標準嚴格執行GB/T 50263-2024《建筑結構檢測技術標準》與ASTM E2309雙重規范,實驗室通過 能力驗證項目18項。人員資質方面實施分級認證制度,檢測工程師需累計完成200小時仿真訓練與50個實體項目實操。設備管理采用智能物聯系統,力值傳感器每48小時自動進行溯源校準,確保測量不確定度≤0.5%。
技術演進與行業協同展望
隨著數字孿生技術與5G通信的深度應用,建議行業重點推進三方面發展:其一構建跨區域檢測大數據平臺,實現全國范圍的結構安全預警網絡;其二開發基于BIM的智能檢測機器人,將傳統檢測效率提升300%;其三建立材料-設計-檢測聯動的標準體系,特別是在新型復合材料領域加快制定彎剪耦合荷載檢測規范。只有通過技術革新與制度完善的雙輪驅動,方能實現工程安全從被動防護到主動預防的范式轉變。

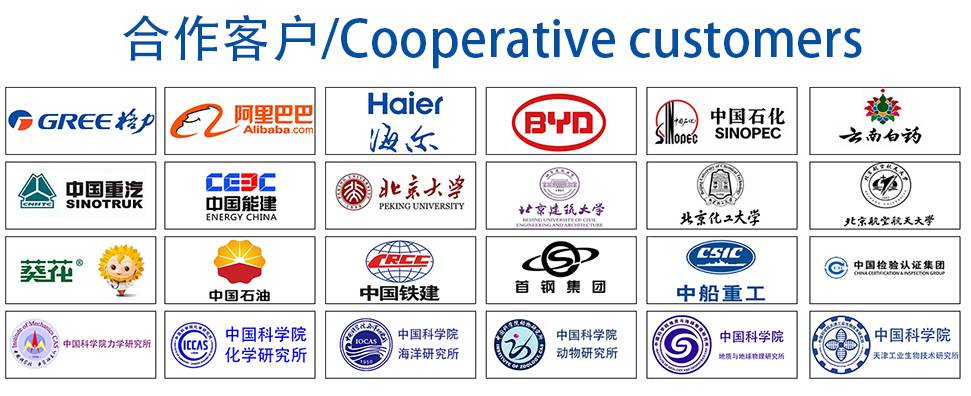