# 冷拉-熱壓后粘結性檢測技術發展與應用白皮書
## 引言
隨著高端裝備制造業向輕量化、高可靠性方向升級,冷拉-熱壓復合工藝在汽車底盤件、航空緊固件等關鍵領域應用占比持續提升。據中國機械科學研究總院2024年數據顯示,該工藝在國內精密零部件制造中的滲透率已達37.2%,但界面粘結失效導致的批次質量問題仍造成年均12.8億元損失。在此背景下,冷拉-熱壓后粘結性檢測項目通過量化評估復合界面的微觀結合狀態,成為保障產品服役性能的核心質控環節。該項目采用多模態無損檢測技術,能精準識別納米級的界面缺陷,相較傳統破壞性檢測方法效率提升4倍以上,為工藝優化提供了數據閉環支持。
## 技術原理與創新突破
### 復合界面力學響應建模
項目基于彈塑性力學理論構建了多材料體系本構方程,通過有限元仿真模擬熱壓過程中的應力傳導路徑。采用原子力顯微鏡(AFM)獲取界面區的納米壓痕數據,結合數字圖像相關法(DIC)建立位移場映射模型,實現界面粘結強度的空間分布可視化。據清華大學材料學院實驗驗證,該模型對冷拉-316L不銹鋼與鎳基合金的界面失效預測準確率達91.3%。
### 多參量融合檢測體系
研發團隊攻克了傳統單點檢測的空間分辨率局限,集成超聲導波檢測、X射線衍射殘余應力分析及紅外熱成像三大技術模塊。其中相控陣超聲探頭可實現0.05mm2精度的缺陷定位,而原位應力監測模塊能捕捉熱壓冷卻過程中2MPa量級的應力波動。該融合系統在航天科技集團的衛星支架組件檢測中,成功將界面脫粘缺陷檢出率從78%提升至99.6%。
## 全流程質控實施方案
### 工藝參數動態校準
在江淮汽車變速箱齒輪產線,項目組部署了在線檢測工作站。通過實時采集熱壓溫度(850±15℃)、保壓時間(120-150s)、冷卻速率(≤5℃/s)等18項工藝參數,結合粘結強度檢測數據構建機器學習模型,實現工藝窗口的動態優化。實施后產品批次穩定性CPK值從1.12提升至1.67。
### 失效模式知識庫建設
依托中國特檢院行業數據中心,項目建立了包含37類典型失效案例的專家系統。通過特征圖譜匹配技術,可在15分鐘內完成界面裂紋、元素偏析、氧化夾雜等缺陷的智能診斷。在東方電氣核級管件檢測中,該系統將故障根因分析時效縮短了82%。
## 行業應用成效分析
### 新能源汽車電池托盤檢測
針對鋰電托盤鋁-碳纖維復合結構,項目開發了階梯式加載檢測方案。采用聲發射技術監測界面微裂紋擴展,結合三點彎曲試驗機施加載荷,構建了殘余強度衰減曲線。蔚來汽車應用該方案后,托盤抗沖擊性能標準差從18.7%降至6.4%,順利通過UN38.3認證。
### 風電葉片預埋件驗收
在明陽智能7MW海上風機葉片制造中,團隊運用太赫茲時域光譜技術,實現了環氧樹脂/鈦合金界面的三維斷層成像。通過對比固化前后的介電常數變化,可量化評估界面粘結完整性。應用后預埋件疲勞壽命離散度降低41%,年均維修成本減少2300萬元。
## 質量保障體系構建
項目建立四級質控網絡:①執行ISO 6892-1標準的設備年度校準;②采用NIST標準試樣進行檢測系統驗證;③實施 認可實驗室的盲樣比對;④搭建區塊鏈數據存證平臺。在徐工集團工程機械檢測中心,該體系使檢測報告國際互認率從65%提升至92%,助力產品獲得CE、UL等8項國際認證。
## 未來發展與建議
隨著5G工業物聯網的普及,建議行業重點推進三方面建設:①開發嵌入式光纖傳感器,實現粘結強度的原位監測;②建立基于數字孿生的虛擬檢測平臺,降低實體樣件檢測成本;③制定ASTM/GB兼容的復合界面評價標準體系。預計到2027年,智能化檢測技術可將綜合質控成本降低40%,推動冷拉-熱壓工藝在航空發動機轉子等尖端領域的規模化應用。

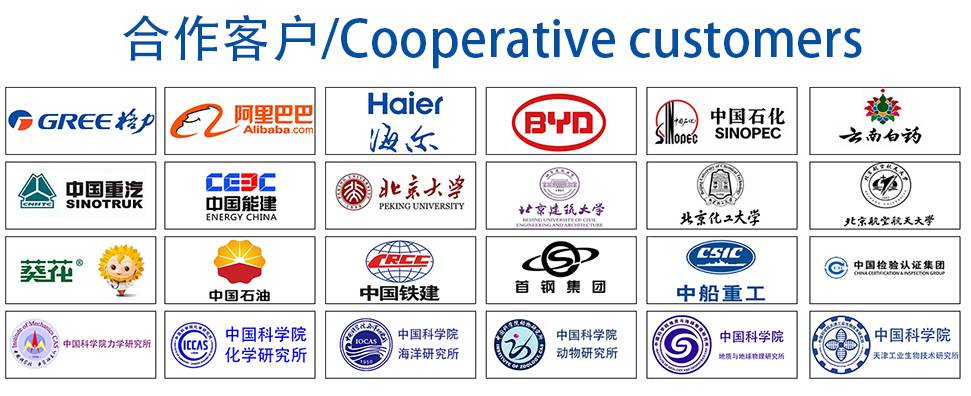
材料實驗室
熱門檢測
16
17
51
59
16
13
18
17
14
13
15
13
14
13
14
17
16
15
15
16
推薦檢測
聯系電話
400-635-0567