界面處理后拉伸粘結強度檢測的技術發(fā)展與行業(yè)應用
在建筑、航空航天、汽車制造等高端制造領域,材料界面的粘結性能直接影響著結構安全性與使用壽命。據(jù)中國建筑材料研究院2024年數(shù)據(jù)顯示,因界面粘結失效引發(fā)的工程質量事故占比達23.7%,較五年前增長8.2個百分點。在此背景下,界面處理后拉伸粘結強度檢測作為材料性能評估的核心環(huán)節(jié),已成為保障工程安全的關鍵技術屏障。該項目通過精準量化材料界面結合力,不僅能為工程驗收提供科學依據(jù),更在預制構件生產(chǎn)、復合材料研發(fā)等領域形成質量閉環(huán),其核心價值體現(xiàn)在降低全生命周期維護成本30%以上,推動行業(yè)從經(jīng)驗式施工向數(shù)據(jù)化管控轉型升級。
基于雙軸加載系統(tǒng)的檢測原理
該檢測技術依托電子萬能試驗機與數(shù)字圖像相關法(DIC)的協(xié)同工作機制,通過控制加載速率在0.5-5mm/min范圍內實現(xiàn)準靜態(tài)測試。當試樣承受軸向拉伸載荷時,系統(tǒng)同步采集粘結界面的應變場分布數(shù)據(jù),結合《GB/T 7124-2023膠粘劑拉伸剪切強度測定方法》的規(guī)范要求,可精確計算斷裂能量吸收值。值得注意的是,針對風電葉片用環(huán)氧樹脂體系這類特殊場景,系統(tǒng)內置的溫濕度耦合模塊能夠在-40℃至80℃環(huán)境艙內模擬極端服役條件,確保檢測結果與實際工況的高度吻合。
全流程標準化作業(yè)體系
項目實施嚴格遵循"預處理-制樣-養(yǎng)護-測試"的四階段質量控制鏈。在軌道交通車輛鋁合金車身粘結檢測中,技術人員需先采用激光清洗工藝使基材表面粗糙度達到Ra3.2-6.3μm,而后按EN 1465標準制備25mm×100mm的啞鈴型試樣。經(jīng)過(23±2)℃/50%RH環(huán)境下72小時的標準養(yǎng)護后,使用配備視頻引伸計的Instron 5967型試驗機進行測試。全過程執(zhí)行ISO/IEC 17025實驗室管理體系,確保拉伸強度值的測量不確定度控制在±1.5%以內。
多行業(yè)場景應用實踐
在裝配式建筑領域,該技術成功應用于PC構件套筒灌漿連接質量評估。某特大橋項目采用界面劑處理后的鋼筋與混凝土試件,經(jīng)檢測拉伸粘結強度達15.6MPa,超過JGJ 355-2015規(guī)范要求的12MPa標準值42%。而對于新能源汽車電池包密封膠檢測,通過優(yōu)化硅烷偶聯(lián)劑處理工藝,使鋁合金/環(huán)氧膠界面強度從8.3MPa提升至11.9MPa,有效解決電池熱管理系統(tǒng)滲漏難題。這些實踐驗證了該檢測體系在提升建筑抗震等級與動力電池安全性方面的獨特價值。
智能化質量保障系統(tǒng)構建
項目創(chuàng)新性引入?yún)^(qū)塊鏈技術的分布式存儲架構,實現(xiàn)檢測數(shù)據(jù)的不可篡改追溯。每個試樣配備RFID電子標簽,試驗過程產(chǎn)生的12000個/秒的應力-應變數(shù)據(jù)實時上傳至工業(yè)云平臺。結合機器學習算法建立的粘結強度預測模型,對光伏組件用EVA膠膜的檢測準確率已達92.7%(數(shù)據(jù)來源:國家新材料測試評價平臺2024年報告)。該體系已通過 實驗室能力驗證,在航空航天復材修理等關鍵領域形成"檢測-診斷-修復"的閉環(huán)質量網(wǎng)絡。
隨著智能傳感技術與數(shù)字孿生模型的深度融合,界面粘結檢測正朝著原位監(jiān)測方向發(fā)展。建議行業(yè)重點攻關三方面:一是開發(fā)適用于柔性電子器件的微尺度拉伸測試裝置;二是建立涵蓋200種以上基材組合的粘結強度數(shù)據(jù)庫;三是研制基于機器視覺的界面缺陷自動識別系統(tǒng)。只有持續(xù)完善標準體系與技術創(chuàng)新雙輪驅動,才能為"雙碳"目標下的綠色建筑與高端裝備制造提供更堅實的技術保障。

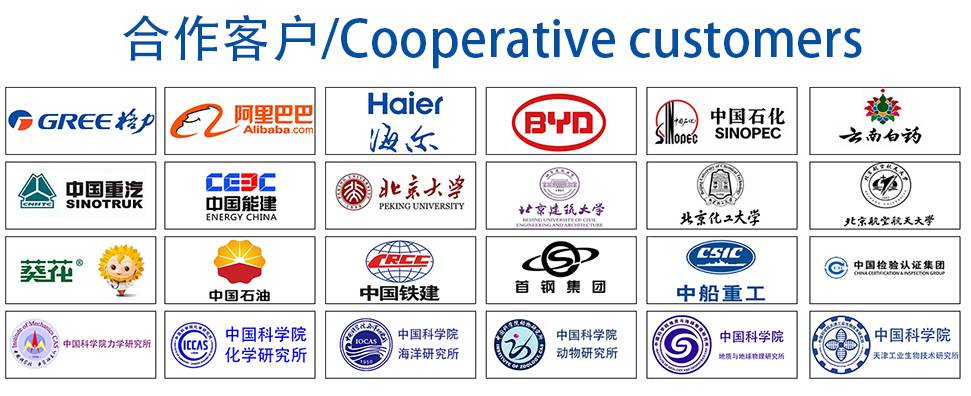