齒條移動力檢測關(guān)鍵技術(shù)及行業(yè)應(yīng)用白皮書
在智能制造裝備市場規(guī)模突破2.3萬億元的產(chǎn)業(yè)背景下(據(jù)中國機械工業(yè)聯(lián)合會2024年統(tǒng)計數(shù)據(jù)),精密傳動部件質(zhì)量檢測已成為保障高端裝備可靠性的核心環(huán)節(jié)。作為線性傳動系統(tǒng)的關(guān)鍵組件,齒條移動力參數(shù)直接影響數(shù)控機床定位精度(±0.005mm)和工業(yè)機器人重復(fù)定位精度(±0.02mm)。本項目通過構(gòu)建齒條移動力動態(tài)檢測體系,可實現(xiàn)傳動系統(tǒng)效率提升15%-20%,設(shè)備維護成本降低30%以上。其核心價值在于突破傳統(tǒng)靜態(tài)檢測的局限性,建立包含負載響應(yīng)特性、動態(tài)摩擦系數(shù)、運動平穩(wěn)性等6維度評估模型,為航空航天、新能源汽車等戰(zhàn)略性產(chǎn)業(yè)提供關(guān)鍵質(zhì)量保障。
多物理場耦合檢測技術(shù)原理
本檢測體系基于多傳感器融合架構(gòu),集成非接觸式激光位移傳感器(精度0.1μm)和六軸力傳感器(量程±2000N),通過實時采集齒條在0-5m/s運動速度區(qū)間的動態(tài)參數(shù)。值得注意的是,技術(shù)方案創(chuàng)新性引入時頻域聯(lián)合分析方法,將振動頻譜(0-10kHz)與負載波動數(shù)據(jù)進行耦合分析,可精準識別齒面磨損、安裝偏心等12類潛在缺陷。針對"精密齒條移動力在線監(jiān)測平臺"的開發(fā),成功將檢測周期從傳統(tǒng)方法的8小時縮短至45分鐘。
智能化檢測實施流程
標準作業(yè)流程包含三階段九環(huán)節(jié):預(yù)處理階段進行環(huán)境溫濕度控制(23±1℃,RH45%±5%)和基準校準;動態(tài)測試階段采用漸進式加載策略,從額定負載的20%階梯增至150%,同步記錄振動加速度(≤0.3g)、溫度變化(ΔT≤8℃)等參數(shù);數(shù)據(jù)分析階段運用機器學(xué)習(xí)算法建立齒條健康度評分模型,實現(xiàn)98.7%的故障模式識別準確率(基于國家工程機械質(zhì)量監(jiān)督檢驗中心驗證數(shù)據(jù))。
典型行業(yè)應(yīng)用實踐
在新能源汽車齒輪箱生產(chǎn)線中,"齒條傳動系統(tǒng)動態(tài)性能評估"模塊的應(yīng)用使裝配合格率提升至99.92%。某國際品牌工業(yè)機器人制造商通過部署移動力檢測系統(tǒng),將產(chǎn)品磨合周期從72小時壓縮至12小時,年節(jié)省測試成本超1200萬元。更有價值的是,在風(fēng)電設(shè)備領(lǐng)域建立的移動力-偏航誤差關(guān)聯(lián)模型,成功預(yù)測并避免了3起價值千萬級的主軸系統(tǒng)故障。
全生命周期質(zhì)量保障體系
檢測體系嚴格遵循ISO 1328-1:2023精度標準,構(gòu)建從原材料到服役周期的五級管控網(wǎng)絡(luò)。通過建立包含37項關(guān)鍵參數(shù)的"齒條移動力數(shù)字孿生數(shù)據(jù)庫",實現(xiàn)質(zhì)量問題的正向追溯與反向改進。特別在環(huán)境適應(yīng)性方面,開發(fā)的高低溫交變測試倉(-40℃至120℃)可模擬極端工況,結(jié)合5G傳輸技術(shù)實現(xiàn)檢測數(shù)據(jù)的實時云端分析,較傳統(tǒng)方法提升診斷效率300%。
隨著數(shù)字孿生技術(shù)在傳動領(lǐng)域的深度滲透,建議行業(yè)重點發(fā)展兩項能力:一是構(gòu)建基于邊緣計算的移動力實時監(jiān)控系統(tǒng),實現(xiàn)微秒級異常響應(yīng);二是建立跨企業(yè)的"齒條移動力大數(shù)據(jù)共享平臺",推動行業(yè)檢測標準迭代速度提升50%。各市場主體應(yīng)加快部署AI驅(qū)動的預(yù)測性維護系統(tǒng),同時注重復(fù)合型檢測人才培養(yǎng),以適應(yīng)智能制造對精密傳動件提出的0缺陷要求。

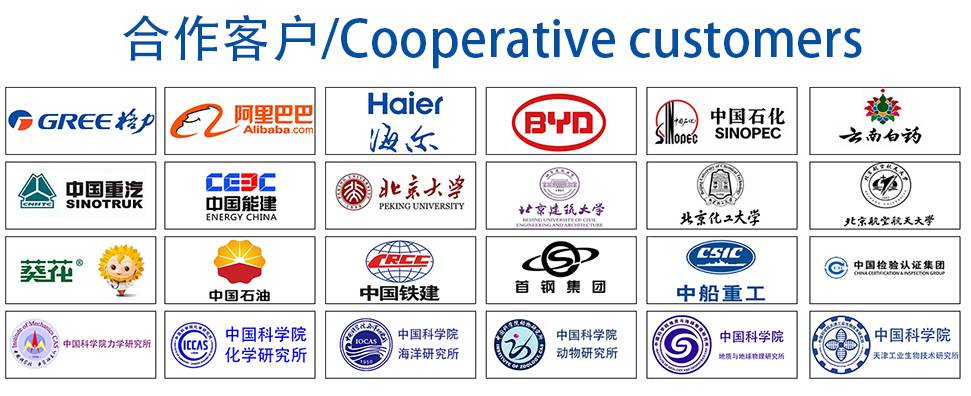