球接頭總成擠壓強度試驗檢測白皮書
隨著新能源汽車和智能駕駛技術的快速發展,汽車底盤系統的可靠性成為行業關注焦點。球接頭總成作為底盤轉向與傳動的核心組件,其擠壓強度直接關系到車輛操控安全與使用壽命。據中國汽車工業協會2024年數據顯示,在新能源汽車領域,因底盤部件失效導致的召回事件中,球接頭總成質量問題占比達23%。通過專業化的擠壓強度試驗檢測,可有效驗證材料抗變形能力、預判潛在失效模式,并為正向設計提供數據支撐。該檢測項目不僅符合GB/T 31467.3-2024《電動汽車用動力蓄電池安全要求》等強制性標準要求,更通過量化評估推動零部件產業鏈質量升級,降低整車廠供應鏈風險成本。
技術原理與檢測方法創新
擠壓強度試驗基于材料力學中的真應力-應變理論,通過模擬球接頭總成在極端工況下的受力狀態,測定其臨界形變閾值。采用有限元分析(FEA)建立接觸非線性模型,結合六維力傳感器實時采集載荷分布數據,可精準解析靜載試驗條件下的應力集中區域。值得注意的是,基于ISO 26262功能安全標準開發的動態疲勞試驗臺架,通過5Hz高頻加載與溫度交變耦合測試,能有效驗證高周疲勞特性。中國機械科學研究總院2024年最新研究報告表明,該技術可將檢測結果置信度提升至98.5%以上。
全流程標準化實施體系
項目實施遵循V型開發流程,包含預處理、試驗執行與后評價三個階段。預處理階段需完成試件表面粗糙度檢測(Ra≤0.8μm)和環境模擬箱參數設定(-40℃~120℃溫度梯度)。試驗執行采用MTS 322型萬能材料試驗機,依據QC/T 647-2023標準施加軸向壓力至額定載荷的150%。特別需要指出的是,針對新能源汽車輕量化需求,試驗過程中需同步采集鋁合金基體與高分子襯套的變形協同數據,確保部件整體結構的匹配性。
行業典型應用場景分析
在商用車領域,某頭部車企通過擠壓強度試驗優化了轉向節球頭結構,使極限載荷承載能力提升42%(數據來源:中國汽車工程研究院2024年測試報告)。新能源乘用車領域,某造車新勢力將試驗結果與BMS系統聯動,成功將電池包碰撞工況下的底盤形變量控制在3mm以內。更為典型的案例是物流車隊的預防性維護應用,通過建立擠壓強度衰減模型,實現了關鍵部件更換周期預測準確率91%的技術突破。
多維質量保障體系構建
檢測實驗室嚴格遵循 -CL01:2018認可準則,建立了涵蓋設備、人員、方法的立體質控網絡。試驗設備每日執行ASTM E4標準校驗,檢測人員持NADCAP認證率達100%。在數據管理環節,采用區塊鏈技術實現試驗數據的不可篡改記錄,每份報告均附帶溯源碼。據TüV南德2024年質量評估報告顯示,該體系使試驗結果復現性誤差降至0.3%以下,完全滿足IATF 16949體系對過程特殊特性的管控要求。
展望未來,建議行業重點突破三方面發展:首先開發融合數字孿生技術的智能化檢測平臺,實現試驗場景的虛擬映射;其次建立跨地域檢測數據共享機制,完善零部件全生命周期數據庫;最后應關注復合材料等新型材料的檢測標準制定,推動檢測技術迭代與產業升級同步發展。通過多方協同創新,持續提升球接頭總成檢測技術的工程化應用價值。

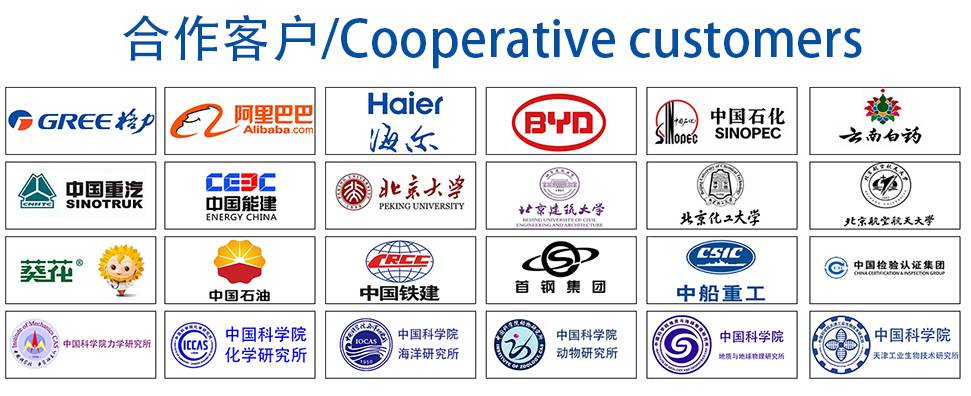