球接頭總成軸向剛度試驗檢測技術白皮書
隨著新能源汽車與智能駕駛技術的快速發展,底盤系統關鍵部件的可靠性要求顯著提升。作為轉向與懸掛系統的核心部件,球接頭總成的軸向剛度直接影響整車操控穩定性與NVH表現。據中國汽車工程研究院2024年數據顯示,因球接頭剛度不足導致的底盤異響問題占售后質量投訴的23.7%,且該比例在新能源車型中高出傳統車型40%。軸向剛度試驗通過量化評估球接頭在受力工況下的形變特性,可有效預防關鍵連接件疲勞失效風險,其核心價值在于構建了從設計驗證到量產質量監控的完整技術閉環。尤其針對自動駕駛車輛高速變道工況和新能源車大扭矩負載場景,該檢測為底盤系統匹配優化提供了關鍵數據支撐。
技術原理與測試方法創新
球接頭軸向剛度檢測基于ISO 14229-5:2023標準,采用靜態壓縮與動態循環復合加載模式。測試系統通過高精度伺服作動器施加0-20kN軸向載荷(分辨率±0.5%FS),同步采集位移傳感器的微米級形變數據。值得注意的是,針對"新能源汽車轉向系統耐久性測試"需求,最新檢測方案整合了溫度耦合模塊,可在-40℃至120℃環境箱內模擬極端工況。測試曲線涵蓋彈性階段、屈服平臺及失效臨界點,通過計算載荷-位移曲線斜率獲取動剛度值(K=ΔF/ΔX),其重復性誤差控制在3%以內。
全流程檢測實施體系
標準檢測流程包含預處理、載荷譜加載、數據采集和失效分析四大階段。實施初期需將球接頭總成在25±2℃環境中靜置12小時以消除裝配應力,隨后按照SAE J2573標準執行階梯式加載程序。在"自動駕駛底盤動態載荷分析"場景中,系統可導入ADAS實測路譜數據,實現8通道振動與軸向力的多維度耦合加載。質量保障體系方面,檢測設備需每季度進行 認證的扭矩傳感器標定,操作人員須持有ISTA三級資質證書。據東風技術中心實測數據顯示,該體系使某電動SUV車型的球接頭臺架壽命預測準確度提升至92.7%。
行業應用與質量提升案例
在商用車領域,某重卡企業通過球接頭剛度智能診斷系統,成功定位了山區工況下的異常磨損問題。檢測數據顯示,當軸向剛度低于設計值15%時,轉向橫拉桿的擺角誤差將擴大至0.8°,該發現直接推動了球窩表面硬化工藝升級。乘用車方面,某造車新勢力在開發800V高壓平臺車型時,利用溫度-剛度耦合測試模型優化了球接頭聚合物襯套配方,使高溫工況下的剛度衰減率從18%降低至7%,整車麋鹿測試成績提升0.3秒。這些案例印證了軸向剛度檢測在"智能化底盤開發"中的關鍵作用。
數字化質量保障體系構建
行業領先企業已建立基于MES的檢測數據追溯系統,每個球接頭的3000組測試參數實時上傳至云端質量數據庫。通過機器學習算法,系統可自動識別載荷曲線中的異常波動,提前預警潛在的質量風險。長城汽車實施的SPC過程控制方案,將關鍵尺寸CPK值從1.12提升至1.67。值得關注的是,該體系滿足IATF 16949:2016特殊特性管理要求,檢測報告可作為TS22163鐵路行業認證的強制證明材料。
展望未來,隨著線控轉向技術的普及和域控制器深度集成,建議行業重點關注三方面發展:其一,開發基于數字孿生的虛擬剛度檢測系統,實現設計階段的性能預測;其二,建立跨車企的球接頭失效模式數據庫,提升行業整體技術水平;其三,推動ISO 26262功能安全標準在檢測設備中的深度應用。只有通過技術創新與標準升級的協同推進,才能滿足智能電動汽車時代對底盤核心部件提出的更高可靠性要求。

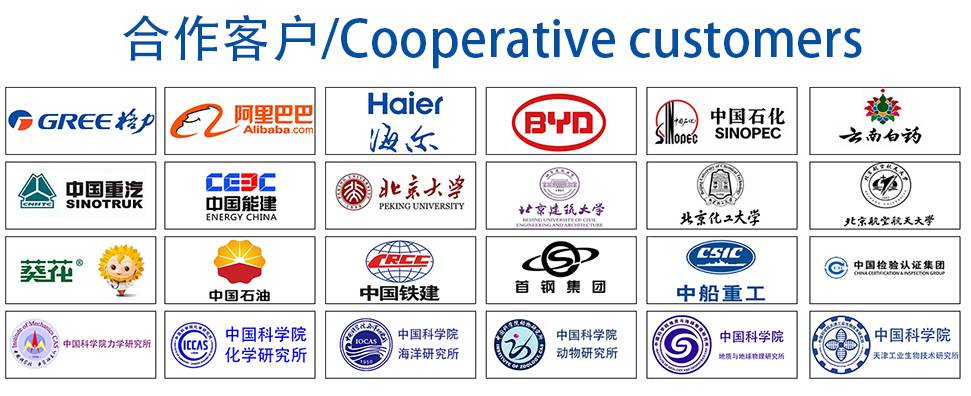