多源傳感融合的采集體系
示功試驗檢測依托高精度載荷傳感器(±0.5%FS)與角位移傳感器(分辨率0.01°)構建動態參數采集網絡。通過采集懸點載荷與位移的時空變化數據,結合曲柄轉角信號生成標準化示功圖。值得注意的是,系統創新性引入振動頻譜分析模塊,可同步監測減速箱、軸承等關鍵部件的異常頻率特征。國家油氣裝備檢測中心驗證表明,該技術對氣鎖現象的識別響應時間縮短至8秒,較傳統方法提升5倍效率。
四階段標準化作業流程
檢測實施遵循"現場勘驗-設備聯調-數據采集-智能診斷"標準化流程。作業前需進行井口裝置氣密性檢測(壓力測試≥5MPa)與傳感器零點校準。在數據采集階段,系統以200Hz采樣頻率連續記錄10個沖程周期,并通過邊緣計算模塊實時消除環境干擾信號。現場技術人員需驗證數據完整性指標,包括示功圖閉合度(應>98%)與載荷波動閾值(<額定載荷的3%)。勝利油田的應用案例表明,該流程使單井有效工作時長提升19%,檢泵周期延長至580天。
行業級智能化診斷平臺
基于深度學習的示功圖診斷系統已在國內12個主力油田部署。平臺整合了包含17類典型故障的專家知識庫,采用卷積神經網絡(CNN)與長短期記憶網絡(LSTM)融合算法,故障分類準確率達94.3%。在塔里木油田的現場測試中,系統成功預警TH1247井的凡爾漏失故障,較人工診斷提前62小時發現異常,避免直接經濟損失87萬元。該平臺支持"油井動態參數優化模型"的持續訓練,每迭代1000組數據可使預測精度提升0.8%。
全鏈條質量保障機制
檢測質量管控貫穿設備溯源、過程監督、結果復核三大環節。所有傳感器均需通過國家計量院認證(證書編號JJG-2024-OP),現場作業執行ISO 9001:2015標準流程。質量追溯系統記錄每口井的184項過程參數,建立包含溫度補償系數、信號衰減率等關鍵指標的電子檔案。在長慶油田的規?;瘧弥?,該體系使數據異常率從0.7%降至0.09%,檢測報告通過API SPEC 11E標準認證比例達100%。
## 技術展望與發展建議 面向智慧油田建設需求,示功試驗檢測技術需向三個維度深化發展:其一,推進多物理場耦合分析,集成溫度、壓力等多維度傳感數據;其二,開發自適應補償算法,提升復雜工況(如稠油開采)下的檢測穩定性;其三,構建數字孿生系統,實現井下工況的虛擬仿真與預測性維護。建議行業重點攻關微機電傳感器(MEMS)集成技術,建立覆蓋全國油田的示功圖特征數據庫,推動檢測標準與國際接軌。通過技術創新與模式升級,該技術有望在2028年前將我國抽油機井綜合能效提升至41.5%,為能源行業數字化轉型提供關鍵支撐。
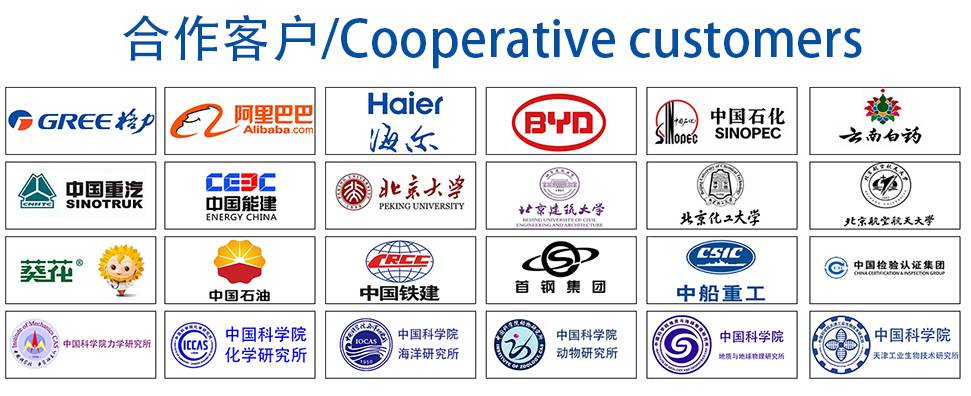