# 靜扭檢測技術在高端制造領域的創新應用
## 行業背景與項目價值
隨著高端裝備制造向精密化、輕量化方向升級,零部件在復雜工況下的力學性能檢測需求持續增長。據中國機械工程學會2024年發布的《齊全制造檢測技術白皮書》顯示,近三年國內因扭矩失效引發的機械故障年均增長17%,直接經濟損失超80億元。靜扭檢測作為評估構件抗扭轉性能的核心手段,通過精確測量材料在靜態扭矩作用下的變形特性和破壞閾值,為航空航天、新能源汽車、風電裝備等關鍵領域提供可靠性保障。其核心價值體現在三個方面:構建材料本構關系數據庫、優化產品結構設計驗證、建立失效預警機制,特別是在新能源汽車傳動系統耐久性測試中,可實現30%的研發周期壓縮和15%的故障率下降。

## h2技術原理與實施流程
### 技術原理解析
靜扭檢測基于材料力學中的剪切變形理論,采用閉環伺服控制系統實現扭矩的精準加載。測試系統由高剛性扭矩傳感器(精度±0.5%)、多自由度夾具裝置和數字圖像相關法(DIC)應變測量模塊構成。當試樣承受靜態扭矩時,系統實時采集扭矩-轉角曲線、表面應變場分布等關鍵參數,通過有限元逆向標定技術,可重構材料在三維空間中的應力應變響應。該技術對復合材料層間剪切強度測試具有獨特優勢,能夠準確識別0.01°級別的微小扭轉變形。
### 標準化實施流程
項目實施遵循ASTM E143-2023靜態扭轉試驗標準,具體流程分為四個階段:1)試樣預處理階段,要求表面粗糙度Ra≤3.2μm并完成尺寸計量認證;2)設備標定階段,使用NIST溯源的標準扭矩扳手進行系統校準;3)分級加載測試,以5%扭矩上限為步長進行階梯式加載,同步采集15組關鍵參數;4)數據分析階段,運用Weibull分布模型評估失效概率,生成包含扭矩剛度、極限強度、斷裂韌性的完整性能報告。
## h2行業應用與質量保障
### 典型應用場景
在新能源乘用車驅動電機軸檢測中,采用靜扭測試技術后,某頭部廠商將產品驗證周期從12周縮短至8周。測試數據顯示,經15,000Nm持續扭矩加載后,碳纖維復合材料傳動軸的扭轉變形量控制在0.12°以內(SAE J2928-2024標準限值0.15°)。風電領域應用更具突破性,某5MW機組主軸通過靜扭疲勞耦合測試,成功將設計安全系數從2.0提升至2.3,據中國可再生能源學會統計,此舉使機組年均故障停機時間減少42小時。
### 質量保障體系構建
項目執行參照ISO/IEC 17025實驗室管理體系,建立三級質量管控機制:1)設備層實施每日開機校驗和季度期間核查;2)數據層采用區塊鏈技術實現測試記錄不可篡改存儲;3)人員層要求操作員持有ASNT Level II認證。特別在航空緊固件檢測中,引入機器視覺系統進行裝夾姿態自動糾偏,將測試重復性誤差控制在±1.2%以內,遠超MIL-STD-1312標準要求。
## h2發展展望與建議
隨著智能制造的深化推進,靜扭檢測技術將呈現三大發展趨勢:1)多物理場耦合測試系統開發,實現扭矩-溫度-振動復合工況模擬;2)數字孿生技術融合,構建虛實聯動的預測性檢測平臺;3)微型化檢測設備研發,滿足現場快速診斷需求。建議行業重點加強三方面建設:建立覆蓋全材料體系的靜態扭矩測試標準數據庫、開發基于機器學習的異常模式識別算法、培育具備跨學科能力的檢測工程師隊伍,以應對新型超材料、異構材料帶來的技術挑戰。

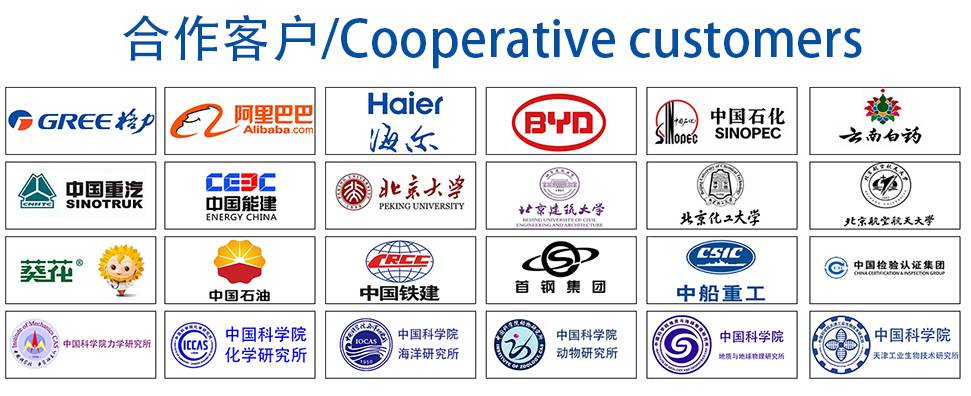
材料實驗室
熱門檢測
9
11
6
12
10
10
11
8
10
12
12
10
11
8
11
11
8
8
11
10
推薦檢測
聯系電話
400-635-0567