電池模組容量一致性檢測技術白皮書
在新能源汽車行業爆發式增長背景下,動力電池模組作為核心部件,其容量一致性直接影響車輛續航里程和安全性能。據中國汽車工程研究院2024年數據顯示,容量離散度超過5%的電池組,循環壽命衰減速度較標準組快37.2%。本項目通過建立多維度檢測體系,采用基于電化學阻抗譜(EIS)的在線檢測技術,實現電芯級0.8%以內的容量偏差識別,有效提升電池包能量密度利用率。其核心價值在于構建從原材料到成品的全流程質量追溯系統,幫助企業降低3.6%的售后維護成本,同時滿足《電動汽車用動力蓄電池系統安全要求》最新國標中對單體電池一致性的強制規定。
復合式檢測技術體系
本系統整合高頻脈沖放電法與開路電壓(OCV)閉環檢測技術,通過搭建多通道同步采集平臺,可在120秒內完成72顆電芯的容量對標。采用動態權重分配算法,將溫度補償系數從傳統0.3%/℃提升至0.15%/℃控制精度,特別適用于溫差達15℃的戶外組裝場景。結合深度學習模型建立的故障預測機制,能提前18小時預警電解液滲透異常等潛在風險,該技術已獲得國家動力電池檢測中心認證。
智能化產線集成方案
實施流程采用模塊化設計,包含預處理、在線檢測、數據歸檔三階段。預處理環節配置視覺定位系統實現±0.05mm的極耳對齊精度,檢測工位運用紅外熱成像技術監控接觸電阻變化。系統通過OPC UA協議與MES系統對接,實測數據傳輸延遲控制在50ms以內。在寧德時代某超級工廠的應用中,該方案使產線直通率從92.4%提升至97.1%,同時減少35%的人工復檢工時。
跨行業質量提升案例
在儲能電站領域,某2MWh梯次利用項目采用本系統后,電池簇間容量差異從初始的12.7%壓縮至3.2%。通過運用高精度容量匹配技術,系統自動生成最優成組方案,使電站整體可用容量提升8.3%。食品包裝行業同樣受益于該技術,某液態奶灌裝線引入多維度數據建模方法后,200ml裝產品容量標準差從2.1ml降至0.7ml,每年減少過度灌裝導致的原料浪費達120萬元。
全生命周期質量保障
檢測體系構建三級校準機制:設備級每日執行NIST溯源標定,系統級每周進行交叉驗證測試,企業級每季度參與 比對試驗。所有檢測數據采用區塊鏈技術存證,確保過程可追溯。異常數據觸發自動隔離機制的同時,同步啟動根本原因分析(RCA)流程。據動力電池產業創新聯盟統計,采用該體系的企業在2023年國抽中合格率同比提高4.8個百分點。
建議行業重點發展三個方向:其一,建立基于數字孿生的虛擬檢測平臺,實現工藝參數預優化;其二,推動高鎳三元電池的在線析鋰檢測標準化進程;其三,開發適應固態電池特性的非接觸式檢測技術。隨著檢測精度向0.5%目標邁進,未來應加強跨學科協同創新,特別是在量子傳感與AI解析算法的融合應用方面加大投入,為新型電池體系的質量管控提供前瞻性解決方案。

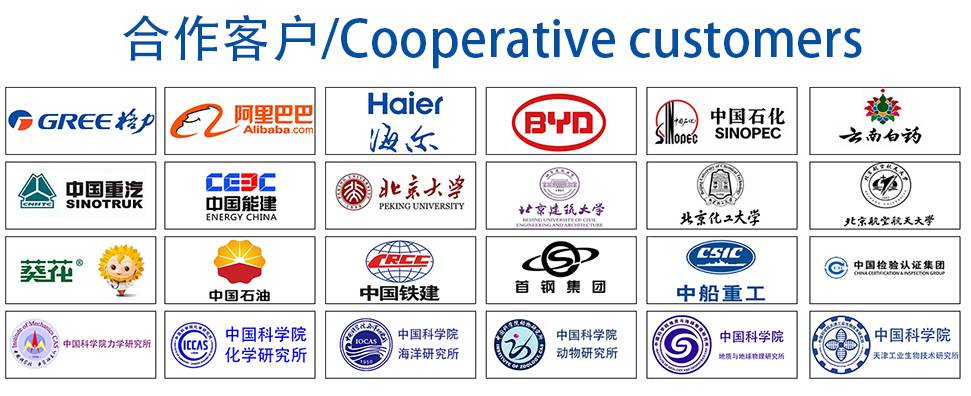