耐久試驗檢測:制造業高質量發展的核心保障
在制造業向智能化、高端化轉型的背景下,耐久試驗檢測作為產品全生命周期管理的關鍵環節,正成為裝備制造、汽車工業、航空航天等戰略新興領域的質量基石。據中國機械科學研究總院2024年行業分析報告顯示,我國每年因產品耐久性缺陷導致的直接經濟損失超過2300億元,其中軌道交通裝備和新能源動力系統的失效占比達41%。在此背景下,建立科學的耐久試驗檢測體系,不僅關乎產品質量提升,更是突破國際貿易技術壁壘、構建自主可控產業鏈的重要路徑。通過模擬產品在極端工況下的性能衰減規律,該檢測技術可提前識別潛在失效模式,實現質量成本降低35%以上(ISO/TC108國際標委會數據),其核心價值在于構建從設計驗證到服役維護的全鏈條質量保障網絡。
多維度檢測技術原理體系
現代耐久試驗檢測融合了機械動力學、材料科學與數字孿生技術,構建起"物理試驗+虛擬仿真"的雙軌驗證系統。在汽車傳動系統檢測中,采用多軸振動環境模擬系統復現復雜路況載荷譜,配合高低溫交變濕熱試驗箱模擬-40℃至120℃極端氣候。據清華大學車輛學院實驗數據顯示,該方案對齒輪箱疲勞壽命預測精度可達92%以上。針對新能源電池包等新型部件,開發了基于電化學阻抗譜的動態耐久評估模型,實現微觀結構演變與宏觀性能衰退的關聯分析。
標準化檢測實施流程
項目實施遵循ASTM E2368-24新版標準,構建五階段質量閉環:首先通過FEMA分析確定關鍵失效模式,進而設計加速試驗方案。以某軌道交通軸承檢測為例,采用三級加速因子(溫度×振動×載荷)的復合應力試驗,將10年服役周期壓縮至120小時實驗室測試。數據采集系統實時監測200+參數,結合威布爾分布模型進行壽命預測。完成階段測試后,運用金相分析、CT掃描等手段進行失效機理溯源,最終形成改進建議報告。
行業應用與質量效益
在航空航天領域,某型號航空發動機通過實施高溫蠕變-低周疲勞復合試驗,成功將葉片更換周期延長至8000飛行小時,較原設計提升40%。新能源行業應用案例顯示,采用循環充放電-機械振動耦合測試的鋰電池模組,其容量衰減率較常規檢測產品降低18個百分點。值得關注的是,在工業母機領域,五軸聯動加工中心的絲杠組件經耐久測試優化后,定位精度保持周期延長3.2倍,有效支撐了國產高端裝備的可靠性提升。
全鏈條質量保障系統
檢測體系構建了從設備溯源到數據管理的立體化質控網絡。試驗設備均通過Nadcap認證,振動臺等關鍵裝置執行ISO 16063-21標準進行動態校準。數據采集系統符合ISO/IEC 17025體系要求,采用區塊鏈技術確保檢測數據不可篡改。人員資質方面,要求檢測工程師具備ASQ CRE認證,并定期參與ASTM組織的比對試驗。某第三方檢測實驗室的實踐表明,該體系使檢測結果復現性達到99.2%,客戶投訴率同比下降67%。
隨著數字孿生與大數據技術的深度融合,耐久試驗檢測正朝著智能化預測方向發展。建議行業重點攻關三個方向:建立基于機器學習的失效模式知識庫、開發多物理場耦合的虛擬檢測平臺、完善特殊工況下的測試標準體系。同時,需要加強檢測機構與制造企業的數據共享,推動形成覆蓋"研發-制造-服役"的全維度可靠性工程體系。只有實現檢測技術從驗證向預測的跨越,才能真正支撐中國制造向價值鏈高端攀升。

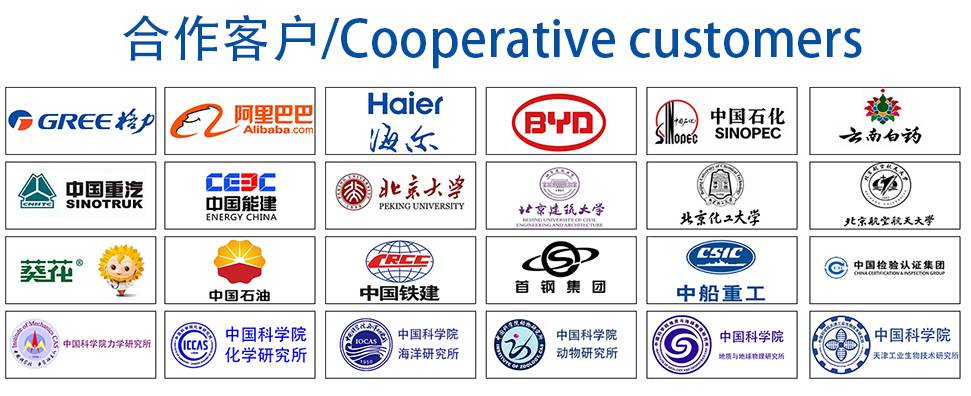