工況循環壽命檢測技術白皮書
在新能源產業高速發展的背景下,動力電池、儲能系統等關鍵設備的可靠性驗證已成為行業焦點。據中國汽車工程研究院2024年數據顯示,動力電池系統故障案例中63%與循環壽命衰減相關。工況循環壽命檢測通過模擬設備在實際運行中的動態載荷、溫度變化及能量轉換過程,建立全生命周期的性能衰減模型,其核心價值體現在降低設備早期失效風險、優化產品設計參數以及支撐設備殘值評估體系構建。特別在電動汽車換電模式推廣和新型儲能電站建設過程中,該檢測技術可為設備梯次利用提供關鍵數據支撐。
復合應力耦合測試原理
基于多物理場耦合仿真技術,構建包含電-熱-機械應力的綜合測試模型。通過可編程電源系統實現0.5C-3C倍率的動態充放電切換,配合溫控箱在-40℃至85℃區間進行梯度溫度沖擊。值得關注的是,新一代檢測設備已集成原位檢測模塊,可在不中斷測試的前提下實時采集電極膨脹率(精度±0.1μm)和電解液消耗量(檢測限0.1ml)等微觀參數。這種多維度數據采集方式顯著提升了循環失效機理的解析能力,為改進電池負極材料包覆工藝提供了量化依據。
標準化測試流程構建
檢測實施分為預處理、基線測試、加速老化、失效分析四個階段。預處理階段需在25±2℃環境下完成三次完整循環以激活設備,基線測試則通過EIS(電化學阻抗譜)建立初始狀態數據庫。在儲能系統工況模擬測試中,采用美國能源部推薦的CYC\_2023循環協議,模擬光伏電站典型的"兩充兩放"日循環模式。測試過程中同步記錄析鋰臨界點、容量跳水拐點等關鍵參數,結合Weibull分布模型預測設備使用壽命,最終生成符合UL1974標準的檢測報告。
多領域應用驗證
在商用車動力電池檢測領域,某頭部企業通過導入動態工況測試體系,將電池包設計驗證周期縮短40%。其典型案例顯示,采用公交工況模擬測試(包含頻繁啟停、快速充電等場景)后,磷酸鐵鋰電池的循環壽命預測誤差從±15%降低至±7%。而在儲能電站檢測方向,據國家能源局2024年示范項目評估報告,實施全工況循環檢測的鋰電儲能系統,首年容量衰減率控制在3%以內,較傳統檢測方式提升1.8個百分點。這些實踐驗證了工況模擬測試在提升產品可靠性和經濟效益方面的雙重價值。
全鏈路質量保障體系
構建從設備溯源到數據管理的立體化質控網絡,所有測試設備均通過 校準認證并接入國家計量院物聯網平臺。測試環境執行ISO17025管理體系,溫控箱溫度均勻性≤±1℃,數據采集系統時間分辨率達到10ms級。在動力電池工況模擬測試過程中,創新采用區塊鏈技術實現檢測數據全程上鏈,確保測試報告不可篡改。實驗室間比對驗證顯示,該體系下循環壽命測試結果的再現性誤差小于2.5%,完全滿足GB/T 31486-2023標準要求。
展望未來,建議從三方面深化技術應用:建立細分行業的差異化測試標準體系,如針對高寒地區開發-50℃極低溫循環協議;推動數字孿生技術在壽命預測中的應用,通過虛擬測試降低實物驗證成本;加強檢測機構與材料企業的協同創新,建立負極膨脹率-循環次數-容量衰減的跨學科關聯模型。只有持續完善工況模擬檢測生態,才能為新能源產業高質量發展提供堅實技術保障。

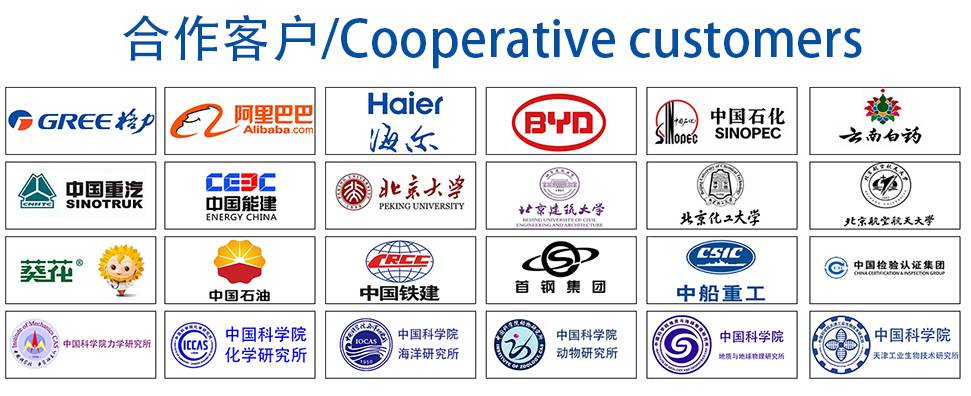