高溫外部短路檢測:核心檢測項目解析
一、檢測目標與意義
- 電氣系統的穩定性:是否能在短路瞬間觸發保護機制(如熔斷器、斷路器等)。
- 熱失控風險:短路產生的熱量是否會導致材料分解、氣體釋放或熱蔓延。
- 結構完整性:短路沖擊是否導致機械形變、密封失效或部件熔融。
二、核心檢測項目
1. 外觀與結構檢查
- 檢測內容:
- 檢查設備外殼、連接端子、導線絕緣層在高溫下的老化、變形或破損情況。
- 確認短路路徑是否因材料軟化或結構松動導致意外導通。
- 標準參考: IEC 62619(工業儲能電池)、GB/T 31485(電動汽車電池安全要求)。
2. 短路電流與溫升測試
- 檢測方法:
- 在高溫環境(如60°C~85°C)下,人為制造外部短路(正負極直接連接),測量短路電流峰值、持續時間及溫升速率。
- 使用紅外熱成像儀監測熱點分布。
- 關鍵參數:
- 最大短路電流(I_max)、溫升速率(ΔT/Δt)、最高表面溫度(T_max)。
- 判定標準:溫度是否符合UL 9540A(儲能系統熱失控評估)中的限值。
3. 絕緣性能評估
- 步驟:
- 短路測試后,立即測量設備內部絕緣電阻(如電池模組極間絕緣電阻)。
- 驗證高溫是否導致絕緣材料碳化或擊穿。
- 設備要求: 使用高壓絕緣測試儀(如500V DC或1000V DC檔位)。
4. 保護裝置響應驗證
- 測試重點:
- 熔斷器、斷路器或BMS(電池管理系統)的響應時間是否在設定閾值內(如<5ms)。
- 保護動作后,是否有效切斷電流回路,防止復通。
- 失效模式分析: 若保護裝置未及時觸發,需排查過流檢測精度或高溫下的器件性能漂移。
5. 氣體排放與化學穩定性分析
- 適用場景: 針對鋰離子電池等化學儲能系統,檢測短路時電解液分解產生的氣體(如CO、H?、CH?)。
- 檢測手段: 使用氣相色譜儀(GC)分析氣體成分,評估熱失控風險等級。
6. 機械結構耐受性測試
- 內容:
- 短路沖擊后檢查殼體是否開裂、密封圈是否失效。
- 評估內部連接件(如匯流排、焊接點)的機械強度是否下降。
- 量化指標: 通過CT掃描或X射線檢測內部結構損傷。
7. 多次循環短路測試
- 目的: 驗證設備在多次輕微短路累積效應下的耐久性(如電網設備在雷擊浪涌后的潛在損傷)。
- 方法: 在高溫環境中重復施加短時(<1s)短路脈沖,記錄性能衰減趨勢。
三、測試設備與環境要求
- 高溫試驗箱:控溫精度±2°C,支持快速升降溫。
- 數據采集系統:同步記錄電流、電壓、溫度信號(采樣率≥1kHz)。
- 安全防護設施:防爆箱、廢氣排放系統、緊急斷電裝置。
四、風險控制與結果判定
- 合格標準:
- 無起火、爆炸、泄漏等不可逆故障。
- 保護裝置及時動作,溫升控制在安全閾值內。
- 風險等級劃分: 根據測試結果劃分風險等級(如低風險、需改進、高風險),指導設計優化。
五、應用案例
- 鋰離子電池模組測試: 某型號儲能電池在85°C下進行外部短路測試,BMS在2ms內觸發斷路,模組表面溫度由60°C升至110°C后趨于穩定,判定為合格。
- 工業連接器失效分析: 高溫導致絕緣層軟化,短路電流引發連接器熔融,改進陶瓷絕緣材料后通過驗證。
六、總結
轉成精致網頁

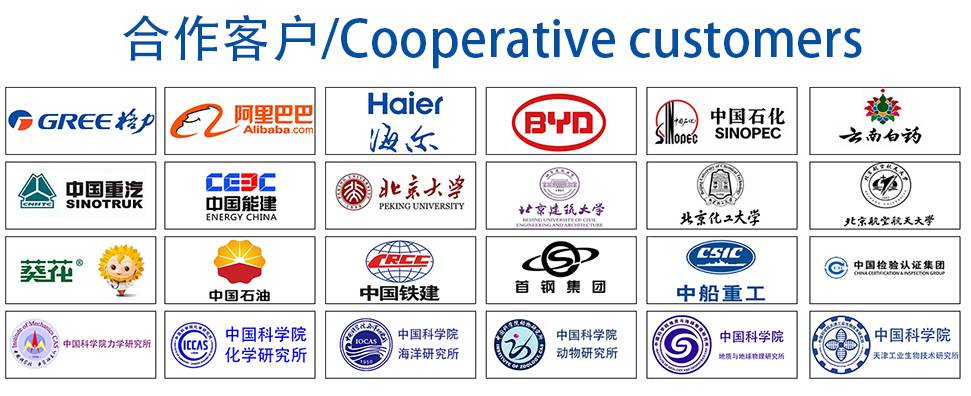
材料實驗室
熱門檢測
推薦檢測
聯系電話
400-635-0567