一、原材料及工藝前檢測
-
- 化學成分分析:通過光譜分析(ICP-OES、XRF)驗證粉末成分符合標準(如ASTM F3049),避免雜質元素(如氧、氮)超標。
- 粒度分布及形貌:激光衍射法(ISO 13320)測定粉末粒徑范圍(通常15-45μm),SEM觀測球形度與衛星粉比例,影響流動性與鋪粉均勻性。
- 流動性測試:霍爾流速計(ASTM B213)評估粉末流動能力,確保鋪粉密度一致性。
-
- 能量密度計算:驗證激光功率、掃描速度、層厚等參數的匹配性,以避免欠熔或過燒。
- 基板預處理檢測:表面粗糙度(Ra≤1.6μm)與清潔度(無油污、氧化物)檢查,保障首層結合強度。
二、打印過程在線監控
-
- 高速攝像與紅外熱成像:實時捕捉熔池尺寸、溫度梯度及凝固行為,識別異常飛濺或熱積累。
- 光致等離子體監測:通過光譜分析等離子體信號(如電子溫度、密度),間接判斷熔池穩定性。
-
- 共軸熔池監控(Coaxial Monitoring):集成光電傳感器檢測熔池反射光強度變化,定位未熔合或孔洞。
- 聲發射技術:采集打印過程中的聲波信號,通過機器學習算法識別裂紋萌生特征。
三、后處理及幾何尺寸檢測
-
- 殘余應力檢測:X射線衍射法(XRD)或中子衍射法測量應力分布,優化熱處理工藝參數(如退火溫度、時間)。
- 表面粗糙度測試:接觸式輪廓儀(ISO 4287)或白光干涉儀量化Ra值,評估是否需要后續機加工。
-
- 三維掃描比對:藍光/激光掃描獲取實際模型,與CAD數模對比,分析尺寸偏差(公差通常±0.1mm)。
- 關鍵特征檢測:CMM(三坐標測量機)精確測量孔位、薄壁厚度等關鍵結構尺寸。
四、內部缺陷及力學性能檢測
-
- X射線計算機斷層掃描(CT):分辨率可達微米級,檢測內部孔隙率(目標<0.5%)、裂紋及未熔合缺陷(ASTM E1695)。
- 超聲波檢測(UT):適用于大尺寸零件,通過回波信號定位缺陷深度(需耦合劑與表面平整)。
- 滲透檢測(PT)與磁粉檢測(MT):針對近表面缺陷,快速篩查裂紋與氣孔。
-
- 拉伸/壓縮試驗:測定屈服強度、抗拉強度及延伸率(參照ASTM E8/E9),對比各向異性差異。
- 疲勞與斷裂韌性測試:評估循環載荷下裂紋擴展速率(da/dN)及臨界應力強度因子(KIC)。
- 顯微硬度測試:維氏或努氏硬度計測量不同區域的硬度分布,反映微觀組織均勻性。
五、微觀組織與化學特性分析
-
- 晶粒形貌與取向:SEM-EBSD分析熔池邊界、柱狀晶/等軸晶比例,關聯力學性能。
- 孔隙與裂紋定量:圖像分析軟件(如ImageJ)統計缺陷數量、尺寸及分布。
-
- 能譜分析(EDS):定位元素偏析(如Al/Ti合金中的成分波動)。
- X射線衍射(XRD):識別相組成(如鈦合金中α/β相比例),避免有害相(如σ相)生成。
六、特殊應用場景附加檢測
- 生物相容性測試(醫療植入物):ISO 10993系列標準,檢測金屬離子釋放量及細胞毒性。
- 高溫氧化性能(航空發動機部件):熱重分析(TGA)評估抗氧化涂層有效性。
- 真空環境驗證(航天部件):氦質譜檢漏儀確保零件在低壓下的密封性。
七、檢測技術發展趨勢
- 智能化檢測系統:AI驅動的缺陷自動分類(如卷積神經網絡識別CT圖像中的孔隙)。
- 多傳感器融合監控:集成熱、光、聲等多模態數據實時反饋,實現閉環工藝優化。
- 標準體系完善:針對新型合金(如高熵合金)制定專用檢測規范(如ASTM/ISO增補條款)。
上一篇:增材制造塑料零件檢測下一篇:組織、組織形態、組織狀態檢測

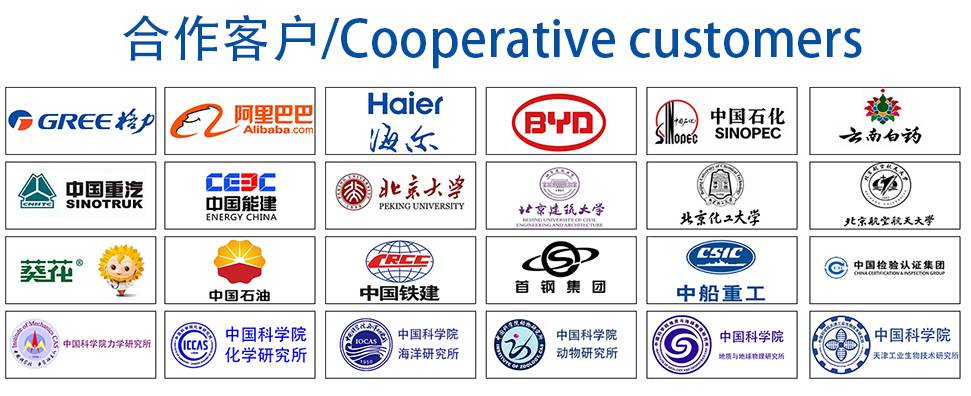
材料實驗室
熱門檢測
22
15
20
22
19
28
21
22
20
24
18
15
19
17
16
15
17
21
18
16
推薦檢測
聯系電話
400-635-0567