一、目視檢查(Visual Inspection)
-
- 裂紋與變形:重點檢查外筒、活塞桿、扭力臂連接處等應力集中區域的表面裂紋,以及結構彎曲或凹陷。
- 腐蝕與磨損:檢查鋁合金或鋼制部件的電化學腐蝕跡象(如點蝕、剝落),密封圈及軸承的磨損程度。
- 緊固件狀態:確認螺栓、銷釘是否存在松動、剪切痕跡或螺紋損傷。
-
- 管路與接頭:觀察液壓油管是否有滲漏、裂痕,快速接頭密封性是否完好。
- 作動筒檢查:確認收放作動筒外壁無變形,活塞桿表面無劃痕或銹蝕。
-
- 傳感器與線纜:檢查起落架位置傳感器、臨近電門的線路絕緣層是否破損,插頭連接是否牢固。
二、無損檢測(NDT, Non-Destructive Testing)
-
- 適用場景:鐵磁性材料(如鋼制支柱)的表面及近表面裂紋檢測。
- 技術要點:通過施加磁場并在表面噴灑磁懸液,觀察裂紋處磁痕聚集情況。
-
- 適用場景:非磁性材料(如鋁合金輪轂)的表面開口缺陷檢測。
- 操作流程:清潔表面→噴涂滲透劑→顯像劑顯影→熒光或顏色對比判定缺陷。
-
- 深度缺陷探測:用于檢測起落架大梁、支撐結構的內部裂紋或分層。
- 案例參考:波音737NG機型主起落架外筒焊縫的UT檢測需符合BAC 5981規范。
-
- 導電材料檢測:適用于輪軸、連桿表面疲勞裂紋的快速掃查,尤其是應力腐蝕裂紋(SCC)。
三、功能性測試
-
- 地面操作:通過液壓泵模擬空中收放流程,監測作動時間是否符合AMM手冊要求(如空客A320主起收放需≤9秒)。
- 位置鎖定驗證:確認上位鎖和下位鎖嚙合到位,避免空中意外解鎖。
-
- 油液壓力檢測:測量油氣式減震支柱的充氣壓力與油量,確保緩沖效率達標。
- 行程測試:檢查支柱壓縮-回彈行程是否在廠商公差范圍內(如超出5%需檢修)。
-
- 剎車響應:模擬不同壓力下剎車盤摩擦效率,檢測剎車片厚度及偏磨情況。
- 前輪轉向:檢查轉向作動器的響應延遲及最大偏轉角度。
四、特殊環境適應性檢測
-
- 采用涂層測厚儀檢測陽極氧化層或漆膜厚度,若低于60μm需重新噴涂。
- 檢查鈦合金部件的鍍鎘層是否因氫脆導致剝落。
-
- 在-40℃環境艙中驗證密封圈彈性及液壓油流動性,防止冷縮泄漏。
五、維修后復檢與記錄管理
-
- 通過靜力試驗臺對修復后的起落架施加1.2倍設計載荷,持續5分鐘無變形。
-
- 使用維護管理系統(如TRACKER)錄入檢測結果,關聯件號、序號及歷史維修記錄。
- 對發現Ⅲ類缺陷(重大隱患)的部件啟用序列號追蹤,強制更換周期。
六、檢測周期與標準依據
- 例行檢測:每500飛行循環或12個月(以先到者為準)。
- 深度檢測:依據MSG-3分析制定,如C檢中對起落架進行全部分解檢測。
- 合規標準:FAR 25部、EASA Part 145及OEM技術文件(如空客SRM、波音SWPM)。
結語

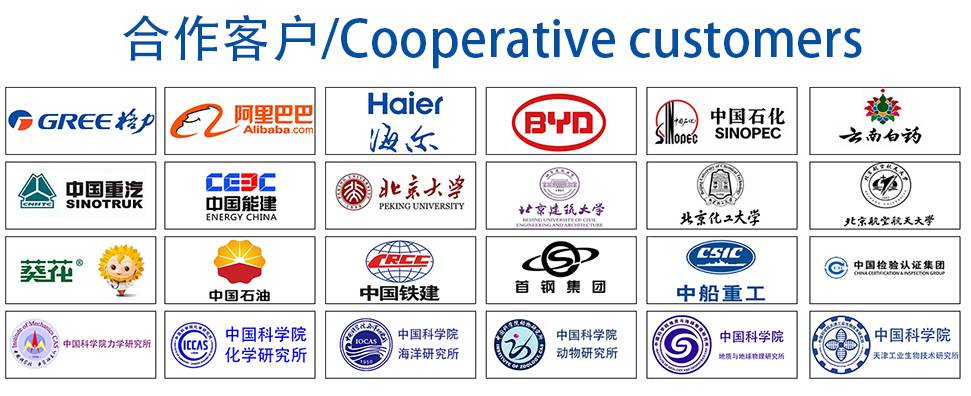
材料實驗室
熱門檢測
21
14
16
23
15
16
13
20
14
17
15
18
24
16
22
24
22
22
21
19
推薦檢測
聯系電話
400-635-0567