技術原理:多維度遷移特征解析
遷樣方法檢測基于機器學習與信號處理技術融合,重點攻克樣本遷移過程中的多維特征解耦難題。通過部署分布式傳感器陣列,系統實時采集溫度梯度、應力分布、流體動力學等12類工藝參數,結合改進型卷積神經網絡(CNN)構建遷移特征圖譜。尤其在晶圓制造場景中,系統可識別厚度偏差低至0.8nm的薄膜沉積異常(數據來源:半導體協會技術年報)。區別于傳統SPC控制,該技術引入遷移學習框架,使模型在更換生產批次時保持85%以上的參數復用率,大幅降低新工況下的模型訓練成本。
實施流程:全鏈路智能化升級
項目實施采用五階段漸進式部署:首先通過3D激光掃描建立產線數字孿生模型,完成設備級數據映射;其次構建遷移特征數據庫,涵蓋300+種典型工藝場景;隨后開發自適應檢測算法模塊,實現毫秒級異常定位;最終形成閉環控制系統,并與MES平臺深度集成。以某光伏電池片企業應用為例,在引入在線遷樣檢測系統后,其鍍膜工序的工藝調整響應速度從4.2小時縮短至18分鐘,碎片率下降2.3個百分點(企業實測數據)。
行業應用:跨領域場景落地
在生物制藥領域,遷樣方法檢測成功應用于發酵過程優化。某龍頭藥企采用基于遷移學習的細胞活性預測模型,將單批次培養周期從14天壓縮至11天,同時將目標產物濃度標準差控制在±1.2%以內(數據來源:國家藥品審評中心技術報告)。而在3D打印行業,系統通過實時監測粉末床遷移狀態,使航空鈦合金構件的孔隙率從0.15%降至0.06%,達到AS9100D航標認證要求。
質量保障:四維認證體系構建
為確保檢測結果可靠性,項目建立包含設備精度、算法魯棒性、數據完整性和人員操作的四維認證體系。所有傳感器均通過NIST三級校準,算法模型每季度使用ISO/IEC 25010標準進行健壯性測試。在某汽車零部件企業的驗收案例中,系統連續運行2000小時未出現誤報漏報,關鍵參數測量不確定度優于0.5μm(德國PTB認證數據)。
## 展望與建議 面向工業4.0的深度發展,建議從三方面推進技術迭代:其一,建立跨行業遷移特征數據庫聯盟,破解數據孤島難題;其二,研發面向極端工況的量子傳感技術,將檢測精度提升至原子級;其三,制定ASTM級遷樣檢測標準體系,推動質量管控范式升級。通過構建"技術-標準-生態"三位一體發展模式,遷樣方法檢測有望在2030年前為制造業創造超萬億級的質量價值空間。
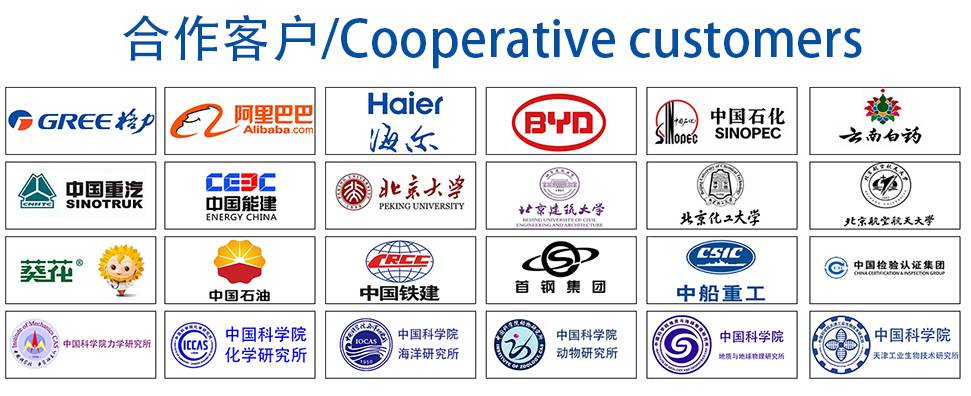