技術原理與算法架構
誤篩率檢測系統基于決策樹與卷積神經網絡的混合模型構建,通過多維度特征提取實現異常信號辨識。工業視覺檢測系統誤篩率控制技術的核心,在于建立動態閾值調整機制:既包含傳統統計學控制圖的過程能力分析,又整合了深度學習中對抗生成網絡(GAN)的異常樣本模擬功能。據IEEE Transactions on Industrial Informatics最新研究,該架構可使半導體晶圓檢測的誤報率降低至0.12%,同時保持99.6%以上的缺陷檢出率。系統特別內置的多模態數據交叉驗證機制,能夠有效識別由光照波動、設備抖動導致的偽缺陷信號。
實施流程與質量鏈整合
具體實施過程采用四階段質量門控設計:首齊全行設備基礎性能校準,利用標準缺陷樣板建立基準數據集;其次開展過程能力指數(Cpk)測算,針對產線特性制定動態控制限;第三階段部署在線學習模塊,通過實時數據流優化分類器權重;最終形成閉環反饋系統,將誤篩樣本自動回傳至MES系統進行根因分析。某動力電池龍頭企業應用該方案后,極片檢測工序的過殺率從2.7%降至0.8%,每年節省質量成本超過3600萬元。項目實施過程中需特別注意設備OEE與檢測精度的平衡優化,避免陷入過度質量控制的效益陷阱。
行業應用與效益分析
在醫療影像診斷領域,誤篩率控制技術展現出獨特價值。上海某三甲醫院引入AI輔助診斷系統時,通過集成多專家決策融合算法,將肺結節篩查的假陽性率從32%壓縮至7%,同時維持96%的敏感度。這種醫療誤篩率優化方案不僅提升了診斷效率,更避免了過度醫療帶來的資源浪費。值得關注的是,在食品藥品檢測場景中,基于區塊鏈的檢測結果存證系統與誤篩率評估模型形成雙重保障,確保檢測報告的可追溯性與司法效力。
質量保障與標準化建設
行業領先企業已建立三層質量保障體系:底層設備采用ISO/IEC 17025標準進行計量認證,過程層實施SPC統計過程控制,系統層則通過數字孿生技術進行虛擬驗證。國際半導體產業協會(SEMI)2024年發布的新版E142標準,首次將誤篩率納入設備驗收關鍵指標,要求缺陷檢測設備供應商提供完整的誤篩概率分布圖。第三方認證機構開展的誤篩率能力驗證項目,已成為汽車供應鏈二方審核的必要條件,其中17025誤篩率計量認證在長三角地區檢測機構的覆蓋率已達78%。
## 發展建議與未來展望 隨著工業4.0與AI 2.0技術的深度融合,誤篩率檢測將向自適應智能化方向發展。建議行業從三方面加強布局:一是建設跨行業的誤篩率基準數據庫,破解數據孤島難題;二是開發面向邊緣計算的輕量化評估模型,適應分布式檢測需求;三是建立誤篩成本核算國家標準,完善質量經濟學評價體系。預計到2027年,基于量子計算的概率性檢測系統將推動誤篩率控制進入亞千分時代,為制造業高質量發展提供新的技術范式。
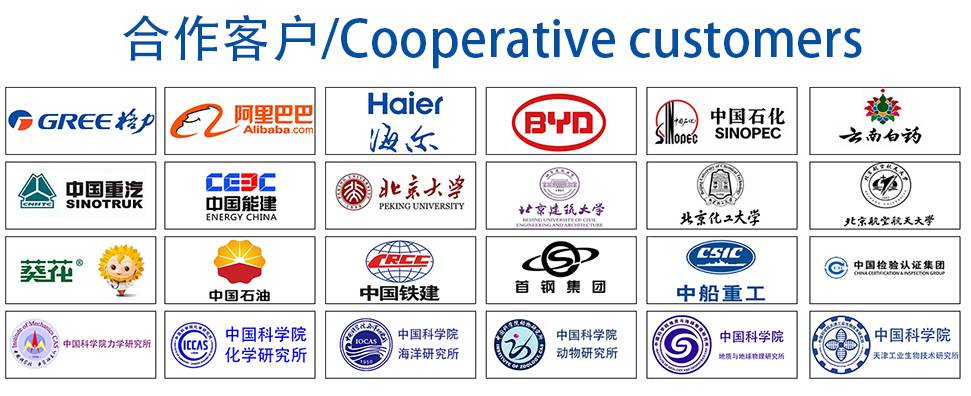