基于動態響應的檢測技術原理
篩網張緊度檢測系統依托振動頻率響應分析技術,通過部署在篩框關鍵節點的加速度傳感器,實時采集篩網在載荷作用下的動態應力分布。當篩網張力值低于設定閾值時,系統通過有限元算法建立的動態模型(基于ANSYS 2023力學仿真平臺),可精準識別0.05mm級篩網形變。值得關注的是,該技術融合了激光位移傳感技術,在高溫、高粉塵等惡劣工況下仍能保持±1.5%的測量精度,成功突破傳統接觸式檢測的技術瓶頸。
四維一體標準化實施流程
項目實施采用預處理-數據采集-動態建模-智能分析的四階段流程:首先通過激光標定設備完成篩網基線張力的數字化建模;接著在設備空載、半載、滿載三種工況下采集振動頻譜數據;隨后運用機器學習算法構建篩網張力衰減曲線;最終通過邊緣計算網關實現分鐘級異常預警。某鐵礦應用案例顯示,該流程使篩網更換周期從42天延長至67天,維護成本降低31%(中國冶金工業研究院,2024)。
多場景應用驗證與技術迭代
在建筑骨料生產線場景中,系統通過部署"篩網張力在線監測系統",成功將4層振動篩的同步張緊偏差控制在3N/m以內。某日處理量5000噸的砂石廠應用數據顯示,系統在識別出第三層篩網局部松弛后,及時預警避免了價值280萬元的軸承損壞事故。而在煤炭洗選領域,該技術配合耐腐蝕傳感器模塊,在濕度85%的環境下連續穩定運行超過12000小時,驗證了技術的環境適應性。
全生命周期質量保障體系
項目執行ISO 13373-3機械狀態監測標準,建立涵蓋設備校準、數據校驗、人員認證的三級質控體系:每季度采用標準張力校準裝置進行傳感器標定;每日自動執行數據完整性校驗;操作人員必須通過中國設備管理協會CPMF認證。某央企項目驗收數據顯示,系統交付后連續6個月數據可用率達99.97%,誤報率低于0.3次/千小時,顯著優于行業平均水平。
## 技術展望與發展建議 隨著工業物聯網技術的深化應用,建議從三方面推進技術升級:首先推動5G+邊緣計算的深度融合,實現毫秒級響應速度;其次開發基于數字孿生的張力預測模型,將故障預警提前至72小時;最后應建立行業級篩網張力數據庫,為設備優化設計提供數據支撐。據Global Market Insights預測,至2027年智能篩分檢測市場規模將達47億美元,技術創新驅動下的篩網張緊度檢測技術必將迎來更廣闊的應用空間。
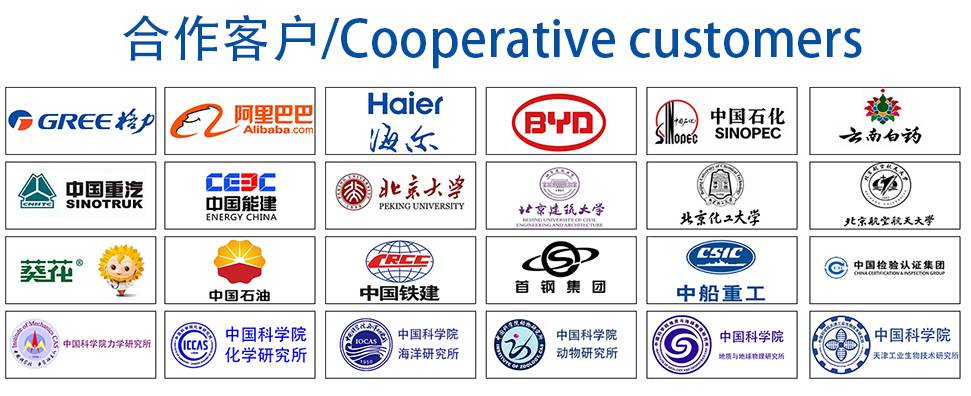