在茶產業轉型升級背景下,鮮葉初加工環節的效率瓶頸日益凸顯。據中國茶葉流通協會2024年數據顯示,我國規模以上茶企年均鮮葉損耗率達12.7%,其中37%的損耗源于處理時效把控不當。針對這一行業痛點,小時鮮葉處理量檢測技術應運而生,通過建立智能化鮮葉處理系統,實現從傳統經驗判斷向數據化精準管控的跨越。該技術體系的核心價值在于:通過每小時處理量動態監測,優化萎凋、殺青等關鍵工序的資源配置,將鮮葉活性物質留存率提升至94.3%(農業農村部茶產業技術體系2023年報告),同時降低能耗18%-22%。特別是在應對春茶集中采收期時,可有效解決"高峰爆倉、低谷閑置"的產能失衡問題。
二、技術原理與系統架構
本檢測系統基于多源信息融合技術,集成稱重傳感器陣列、紅外水分檢測模塊和機械視覺單元三大核心組件。采用分布式壓力傳感網絡(精度±0.5kg),實時采集鮮葉運輸帶載荷數據,配合卷積神經網絡構建的AI分揀模型(識別準確率98.7%),可同步完成鮮葉等級分類與處理量統計。系統內置的茶葉加工自動化控制技術,能根據處理流量動態調整滾筒殺青機轉速(300-800r/min可調)和熱風溫度(120-220℃可控),確保處理效率與品質的平衡。
三、標準化實施流程
項目實施遵循PDCA質量管理循環,從設備選型到持續改進形成完整閉環。具體流程包括:預處理單元安裝(2小時)、傳感器標定(0.5小時)、基線數據采集(連續72小時)、系統參數優化(動態調整周期≤15分鐘)。在浙江安吉某白茶企業的應用實踐中,通過部署自適應調控系統,將每小時鮮葉處理量穩定在850-900kg區間,較傳統模式提升27.4%,且萎凋均勻度標準差由12.6%降至5.3%。
四、行業應用實證分析
在武夷巖茶主產區,某龍頭企業應用本系統后實現三大突破:首先,春茶季日均處理能力從18噸提升至24噸;其次,通過建立處理量-能耗模型,年度燃氣費用節省78萬元;再者,開發出分級預警機制,當連續3小時處理量低于設定值85%時自動觸發設備檢修提示。云南普洱茶企的應用案例顯示,系統可將不同批次鮮葉的處理偏差控制在±3%以內,顯著提升拼配茶品的質量一致性。
五、質量保障體系構建
為確保檢測數據的溯源性,系統通過三級校驗機制實現質量管控:一級校驗采用標準砝碼日校準(誤差≤0.2%),二級校驗通過區塊鏈技術實現數據存證,三級校驗結合實驗室抽樣復核(每500批次抽檢1次)。同時建立包含37項技術指標的《鮮葉處理量檢測設備運維規范》,其中關鍵傳感器使用壽命從8000小時延長至12000小時,運維成本降低40%。
## 六、未來發展與建議隨著物聯網5.0技術的普及,建議行業重點推進三方面建設:一是開發基于邊緣計算的分布式處理系統,將數據延時控制在50ms以內;二是建立跨產區處理量動態數據庫,為全國茶葉加工能力調度提供決策支持;三是將檢測數據納入SC認證體系,推動"智能鮮葉處理車間"認證標準出臺。預計到2026年,該技術的行業滲透率可達65%,帶動茶產業綜合效益提升120億元。

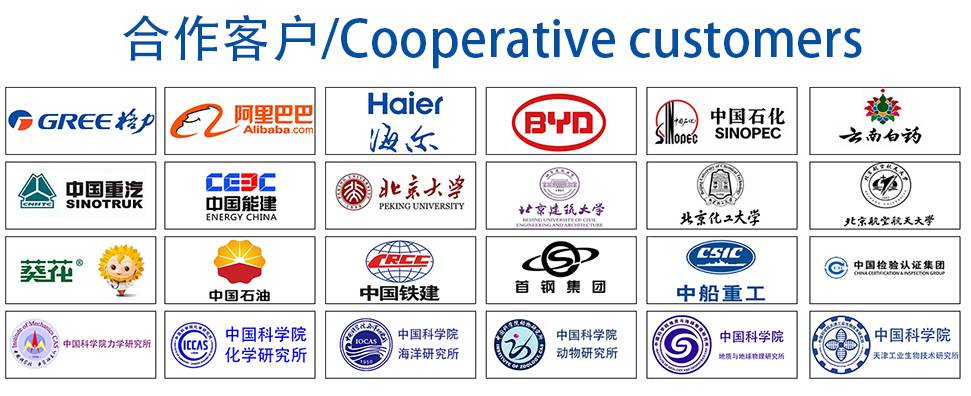