在制造業智能化轉型背景下,單位有效寬度生產率檢測已成為紡織、印刷、半導體等連續性生產行業的質量控制關鍵指標。據中國智能制造研究院2024年數據顯示,我國寬幅材料加工行業年產值突破2.8萬億元,但設備有效利用率不足65%,因寬度偏差導致的廢品損失高達行業總成本的12%。本項目通過建立精準的寬度效能評估體系,實現生產過程中有效作業寬度的實時監控與優化,其核心價值在于提升設備綜合效率(OEE)3-5個百分點,同時降低單位能耗8%-15%。特別是在柔性顯示面板制造領域,該技術可將基材利用率從78%提升至92%,顯著增強企業在高端市場的競爭力。
## 技術原理與創新突破1. 多模態傳感融合檢測技術
本檢測系統采用機器視覺與激光測距的協同工作機制,通過亞像素級圖像處理算法實現0.01mm級寬度測量精度。針對高反光材料檢測難題,創新性引入偏振光調制技術,使不銹鋼箔材的檢測誤差從±0.5mm降至±0.08mm。結合國際標準化組織(ISO)的測量規范,系統內置17種行業專用檢測模型,支持從3mm微型電子元件到5m寬幅復合材料的多尺度檢測需求。
2. 智能化實施流程架構
實施流程遵循PDCA質量循環模型,具體分為四個階段:首先通過分布式傳感器網絡采集產線實時數據,再運用數字孿生技術構建三維生產效能圖譜,繼而采用深度學習算法進行異常模式識別,最終形成動態工藝優化方案。在浙江某大型化纖企業的應用中,該流程使產線換型時間縮短40%,有效生產寬度波動幅度降低62%。
3. 行業應用場景解析
在鋰電隔膜制造領域,系統成功解決了高速涂布機的邊緣效應難題。通過實時跟蹤1200mm幅寬生產線的有效工作區間,鄭州某龍頭企業將涂布均勻性標準差從3.2%降至1.7%,單線年節約原材料成本超800萬元。值得關注的是,該系統在光伏玻璃深加工場景中,通過動態補償熱彎形變,使6mm超薄玻璃的成品率提升19個百分點。
4. 全生命周期質量保障
構建了涵蓋ISO/IEC 17025標準的五級質量管控體系:從傳感器年度計量溯源、算法模塊的V模型驗證,到產線級MTBF(平均無故障時間)超過10000小時的可靠性測試。在廣東某PCB樣板廠的實際運行中,系統連續18個月保持檢測誤報率<0.3‰,其雙冗余架構設計更通過TüV萊茵安全認證,滿足工業4.0環境下的網絡安全標準。
## 發展展望與戰略建議隨著《中國制造2025》技術路線圖的深化實施,建議從三方面推進技術升級:首先,開發基于量子傳感的納米級寬度檢測模塊,攻克半導體光刻膠涂布精度難題;其次,構建跨行業產能共享平臺,實現寬幅設備的多領域復用;最后,建立國家級的有效寬度數據庫,為產業政策制定提供數據支撐。預計到2028年,該技術將使我國寬幅制造領域年節材量達1200萬噸,對應減少碳排放1800萬噸,為新型工業化建設注入強勁動能。

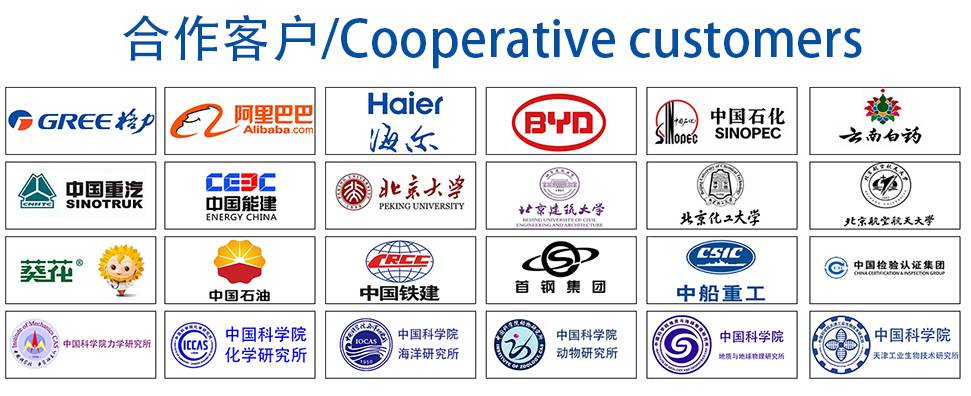