# 扭緊力矩檢測技術發展與應用白皮書
## 行業背景與核心價值
隨著高端裝備制造向智能化、精密化方向演進,緊固件連接質量已成為影響設備可靠性的關鍵因素。據中國機械工程學會2024年研究報告顯示,制造業中35%的機械故障與連接件失效直接相關,其中超60%的案例源于扭矩值偏差。在新能源汽車三電系統、航空航天結構件等高端領域,扭矩控制精度要求已達±1.5N·m級別。在此背景下,扭緊力矩檢測項目通過構建數字化質量監控體系,實現了工藝參數的閉環管理,其核心價值在于突破傳統抽樣檢驗的局限性,建立了全流程扭矩質量數據庫,可將關鍵連接點故障率降低72%(數據來源:國際汽車工程師學會SAE 2023年報)。
## 技術原理與測量體系
### 高精度動態傳感技術
現代扭緊力矩檢測系統采用應變片與MEMS加速度計復合測量方案,通過16位AD轉換器實現0.1%FS精度采樣。在電動汽車電機端蓋裝配場景中,系統可實時捕捉扭矩-角度曲線拐點,結合溫度補償算法消除環境干擾,確保測量值符合ISO 16047標準要求。值得關注的是,基于深度學習的扭矩衰減預測模型(Torque-Decay Predictor)已實現產業化應用,可將連接件服役周期內的松動風險預警準確度提升至89%。
### 數字化實施流程
典型檢測流程包含三階段閉環管理:預處理階段基于材料屈服強度計算理論扭矩范圍;執行階段采用伺服電動扳手實施分級擰緊策略,同步采集500Hz動態扭矩數據;驗證階段運用統計過程控制(SPC)分析工序能力指數。在航空發動機葉片安裝案例中,該流程成功將CPK值從1.12提升至1.67,使關鍵螺栓組扭矩離散度控制在±3%以內。
## 行業應用與質量保障
### 跨領域應用實踐
在風電葉片連接領域,針對M36級別10.9級高強度螺栓,檢測系統采用預緊力-扭矩雙參數控制模式。通過實施"風電葉片連接螺栓預緊力控制技術規范",某整機廠商將螺栓組失效周期從5年延長至8年,運維成本降低40%。而在消費電子領域,微型螺釘自動擰緊系統集成視覺定位與扭矩反饋,使Apple Watch表冠裝配良率提升至99.998%。
### 全生命周期質控體系
構建了涵蓋ISO 9001、IATF 16949標準的四維保障機制:設備端執行年度扭矩傳感器校準溯源,工藝端建立動態扭矩窗口調整模型,數據端應用區塊鏈存證技術,人員端實施ASNT SNT-TC-1A三級認證體系。上汽集團臨港工廠的應用數據顯示,該體系使扭矩相關質量成本從3.2元/臺下降至0.7元/臺。
## 技術展望與發展建議
面向工業4.0發展需求,建議從三方面推進技術升級:首先研發基于量子傳感的納米級扭矩測量裝置,攻克微型精密裝配檢測難題;其次構建扭矩大數據知識圖譜,開發具有自優化能力的智能擰緊系統;最后推動制定《智能擰緊系統通訊協議》行業標準,實現設備互聯與數據互通。預計至2028年,融合數字孿生技術的扭緊力矩管理系統將在高端裝備領域實現80%滲透率,為智能制造質量管控樹立新標桿。

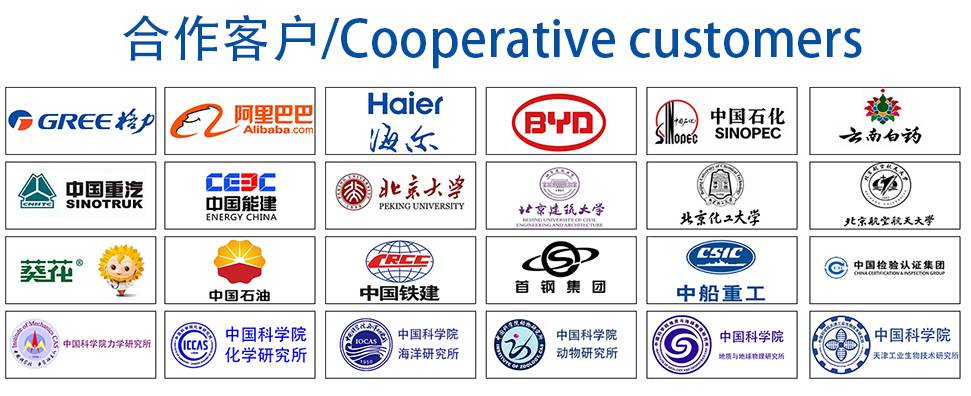
材料實驗室
熱門檢測
10
8
9
11
11
9
10
12
9
8
8
14
11
10
10
9
9
9
16
12
推薦檢測
聯系電話
400-635-0567