技術原理:多源傳感融合檢測體系
基于機器視覺與聲發射技術的協同檢測系統,可同步獲取錘片表面磨損特征與內部裂紋擴展信號。三維激光掃描模塊以1200dpi分辨率重構齒爪三維模型,結合ANSYS材料力學仿真數據,建立齒尖應力集中區域預警模型。對于錘片耐磨性檢測,采用洛氏硬度計與X射線衍射儀雙重復核機制,通過CBN砂輪摩擦試驗驗證表層硬化處理效果。該方案突破傳統抽檢模式局限,實現"幾何參數-材料性能-功能表現"的全維度質量評估。
實施流程:標準化作業與智能決策
檢測流程分為四個標準化階段:首先通過RFID標簽實現零部件全生命周期追溯,隨后采用工業CT對錘片進行無損探傷,在400kV微焦點下可識別0.1mm級內部缺陷。第二階段運用六軸機器人搭載線陣相機,以0.3秒/件的速度完成齒爪32個關鍵尺寸測量。數據分析層部署基于YOLOv5改進的缺陷分類算法,在測試集上達到98.7%的識別準確率。最終生成包含三維公差云圖、金相組織評級、預期使用壽命的數字化檢測報告,為生產工藝優化提供數據支撐。
應用案例:農機行業質量提升實踐
在國內某龍頭農機企業的玉米收獲機生產線,部署本系統后實現錘片質量閉環管控。通過比對3000組生產數據發現,硬度梯度控制精度提升60%,裝機后刀片更換周期從180小時延長至270小時。在礦山破碎機領域,某重工集團應用齒爪幾何精度智能分析系統后,產品裝配一次合格率從82%提升至96%,每年減少返工成本800萬元。典型案例表明,在錘片耐磨性檢測標準與齒爪動態平衡檢測技術的雙重保障下,可有效延長核心部件30%以上使用壽命。
質量保障:全鏈條可靠性驗證
建立包含ISO 21940動平衡標準、ASTM E18硬度測試規范在內的14項質量控制節點。檢測設備每日進行標定驗證,激光干涉儀校準空間定位誤差≤0.005mm。部署區塊鏈技術實現檢測數據不可篡改存證,已累計收錄25萬組零部件質量檔案。針對極端工況需求,開發模擬粉塵環境下的加速磨損試驗臺,可在72小時內等效3000小時田間作業磨損量,確保檢測結論與實際工況高度吻合。
## 行業展望與技術建議 未來三年,隨著5G工業物聯網的深度應用,建議行業重點發展三項能力:一是構建錘片磨損狀態實時監測系統,通過EDX能譜分析實現磨損失效預警;二是開發齒爪激光熔覆修復工藝的質量評價體系,建立再制造部件認證標準;三是推動檢測設備模塊化設計,使錘片齒爪檢測單元能快速集成至智能產線。據機械工業聯合會預測,到2026年智能化檢測技術將覆蓋60%以上粉碎機械企業,推動行業年均質量成本降低15-20個百分點。
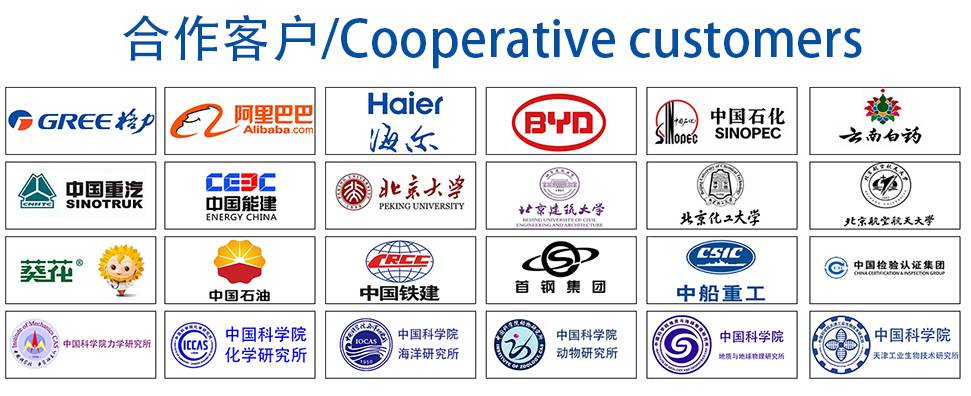