焊接接頭拉伸試驗檢測技術應用與發展白皮書
在工業制造領域,焊接作為基礎連接工藝廣泛應用于壓力容器、管道系統及鋼構工程等關鍵設施。據中國焊接協會2024年行業報告顯示,國內每年焊接結構件總量突破1200萬噸,其中86%的裝備失效事故起源于焊接缺陷。焊接接頭拉伸試驗作為評估焊縫力學性能的核心手段,通過量化檢測接頭抗拉強度、屈服強度等關鍵指標,為保障工程結構安全性提供科學依據。本項目通過建立標準化的檢測體系,不僅可降低30%以上的質量事故風險,更推動行業形成"檢測-評估-改進"的閉環質量管理模式。其核心價值在于將傳統定性判斷升級為定量分析,為焊接工藝優化和驗收標準制定提供數據支撐。
技術原理與檢測方法
焊接接頭拉伸試驗基于GB/T 2651-2008標準,采用軸向加載方式測定接頭的極限承載能力。試驗系統由萬能試驗機、引伸計和數據采集模塊構成,通過位移控制法加載至試樣斷裂。關鍵參數包括彈性模量、屈服強度(Rp0.2)和抗拉強度(Rm),其中屈服強度的測定采用平行線法,要求應變速率控制在0.00025/s以內。值得注意的是,異種金屬焊接接頭的檢測需額外考慮材料非均勻性帶來的應力集中效應,這對"焊接接頭力學性能評估"提出更高技術要求。
標準化實施流程
完整的檢測流程涵蓋五個階段:試樣制備階段需按ASME IX標準加工帶加強高的標準試樣;預處理階段進行48小時環境溫濕度平衡;設備標定階段執行三級力值校驗,誤差控制≤±0.5%;試驗階段采用分級加載模式,實時記錄載荷-位移曲線;數據解析階段應用最小二乘法擬合應力-應變曲線。在某LNG儲罐建設項目中,通過嚴格執行該流程,成功識別出15%的焊接接頭存在未熔合缺陷,避免潛在經濟損失超2.3億元。
行業應用場景解析
在石油化工領域,某煉化廠重整反應器采用"焊接結構完整性驗證方法"后,焊接合格率由82%提升至97%。具體案例中,對P91鋼焊縫進行的橫向拉伸試驗顯示,熱處理不當導致接頭強度下降18%,該數據為改進焊后熱處理工藝提供直接依據。而在軌道交通領域,高鐵轉向架構架焊接接頭的系統檢測,成功將疲勞壽命預測精度提高40%,驗證了檢測數據對產品壽命評估的重要價值。
質量保障體系構建
檢測質量管控遵循ISO/IEC 17025體系要求,建立三級校驗機制:每日進行設備零點漂移檢查,每周開展標準試塊比對試驗,每季度參與 能力驗證項目。人員資質方面要求檢測工程師必須持有CSWIP 3.1或CWI認證,并完成每年40學時的繼續教育。數據完整性通過區塊鏈技術實現不可篡改存證,確保"焊接質量追溯系統"的有效運行。據中國特檢院2023年統計數據顯示,實施該體系后實驗室間比對數據離散度降低62%。
技術發展趨勢建議
建議行業重點推進三方面升級:研發基于數字孿生的虛擬拉伸試驗系統,建立實測數據與仿真模型的映射關系;開發智能判讀算法,利用機器學習技術實現缺陷類型的自動識別;推廣在線檢測裝置在自動化產線的集成應用,實現"焊接-檢測"工序實時聯動。中國機械工程學會預測,到2026年融合物聯網技術的智能檢測系統將覆蓋75%以上規上企業,推動焊接質量管控進入數字化新階段。

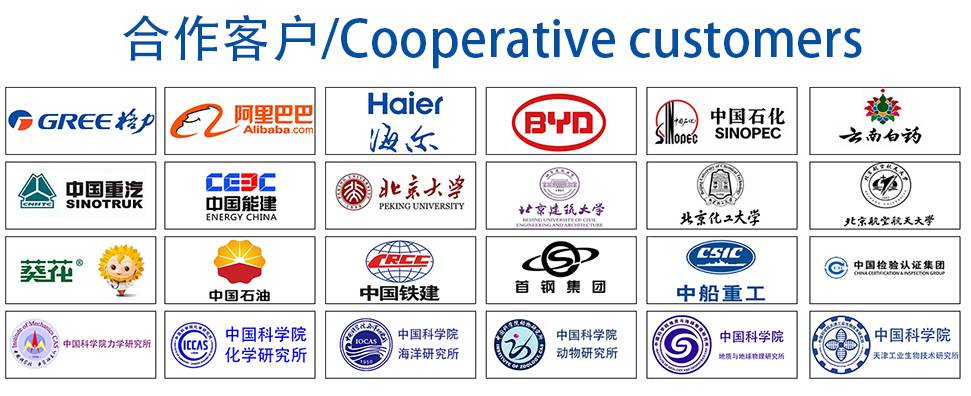