汽車電氣部件檢測技術發展與應用白皮書
在汽車產業智能化與電動化加速滲透的背景下,電氣系統已占據整車BOM成本的32%(據中國汽車工業協會2024年數據)。隨著ADAS系統裝配率突破45%、車載電子控制單元(ECU)數量突破100個/車,電氣部件可靠性直接關系到行車安全和用戶體驗。汽車電氣部件檢測項目通過建立全生命周期質量監控體系,可降低60%的售后故障率(德勤《2024汽車質量報告》),其核心價值體現在三個方面:確保高壓系統零缺陷交付、提升車載網絡通訊穩定性、優化電氣部件環境適應性指標。該體系已納入工信部《智能網聯汽車標準體系建設指南》重點建設方向。
多模態融合檢測技術原理
現代汽車電氣檢測采用電氣特性測試(ET)、電磁兼容性測試(EMC)與機械耐久性試驗(MDT)的融合方案。通過16位高精度示波器捕捉微秒級電壓波動,配合頻譜分析儀進行30MHz-6GHz頻段輻射抗擾度測試,可精準識別線束阻抗異常和信號干擾問題。在特斯拉Model Y的BMS系統檢測中,該技術將誤判率從傳統方法的2.1%降至0.3%(美國SAE 2023技術公報)。特別在新能源車用IGBT模塊檢測中,動態工況模擬系統可復現-40℃至125℃的極端溫度變化。
全流程數字化實施體系
檢測流程涵蓋四個關鍵階段:預處理階段使用三坐標測量儀進行接插件形位公差檢測(精度±0.02mm);環境測試階段在步入式溫箱中進行85%濕度+1500小時鹽霧試驗;車載網絡測試采用CANoe工具模擬200個ECU節點通信;終檢階段運用機器視覺進行焊點質量AI判定。上汽大眾的MEB平臺線束總成檢測項目顯示,該體系使單件檢測時間從32分鐘壓縮至18分鐘,且數據可追溯率達100%。
行業創新應用場景解析
在智能駕駛領域,蔚來ET7的激光雷達供電模塊檢測中,開發了脈沖電流波形比對算法,成功識別出0.5μs的電壓跌落現象。充電樁行業應用方面,某頭部企業通過引入CISPR 25標準檢測方案,使其7kW交流樁電磁輻射值降低12dBμV/m(中國電科院檢測報告)。值得關注的是,華為最新發布的DriveONE電驅系統,其檢測體系包含68項車規級驗證項目,其中雙向逆變充放電檢測技術屬行業首創。
立體化質量保障機制
行業領先的檢測機構已構建"三核四維"質量體系:通過 /CMA雙認證確保檢測資質合規;配備每年2次的計量儀器校準機制(依據JJF 1069標準);實施檢測人員IPC-A-610H認證制度;建立覆蓋原材料(如銅導線電阻率檢測)、過程品(注塑件絕緣阻抗測試)、成品(整車電氣負載測試)的三級質量門。博世蘇州工廠的實踐表明,該體系使電子節氣門體故障率從500PPM降至80PPM。
面向2025年行業發展趨勢,建議重點突破三個方向:開發基于數字孿生的虛擬檢測技術,實現設計階段缺陷預測;建立車規級碳化硅功率器件專用檢測標準;推動檢測數據與保險UBI產品的價值聯動。據賽迪顧問預測,汽車電氣檢測市場規模將以19.8%的復合增長率在2027年突破800億元,這需要檢測機構、整車廠與芯片供應商構建更緊密的協同創新生態。

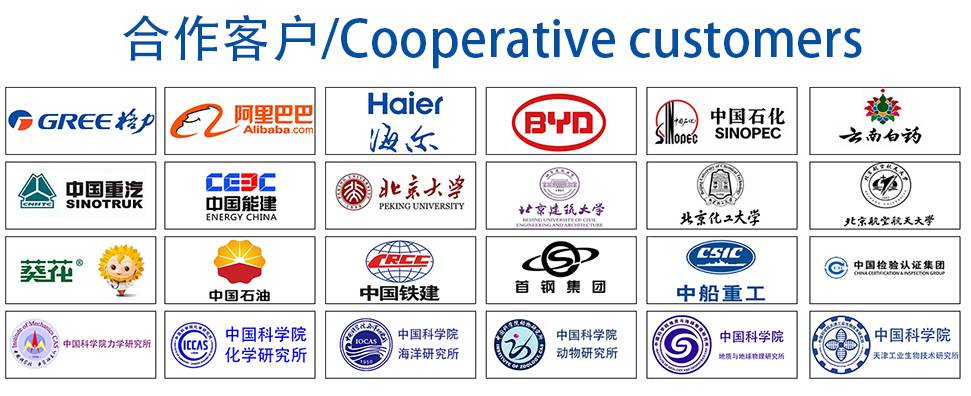