# 螺釘和連接檢測技術發展與應用白皮書
## 首段:行業背景與項目價值
隨著高端裝備制造業向智能化轉型,機械連接件的可靠性成為影響整機性能的關鍵因素。據中國機械工程學會2024年數據顯示,因螺釘松動、斷裂引發的裝備故障年均損失超120億美元,其中新能源汽車與軌道交通領域占比達43%。在此背景下,螺釘和連接檢測技術通過精準識別裝配缺陷、預判失效風險,成為保障工業安全的核心環節。該項目依托多模態傳感與智能分析技術,實現了從靜態參數測量到動態服役狀態監測的跨越式升級,可將連接失效事故率降低67%(中國質量協會,2023)。其核心價值在于構建覆蓋設計驗證、生產質控、運維監測的全生命周期管理體系,為智能制造提供關鍵質量保障支撐。
## 技術原理與創新突破
### 多維度連接質量評估體系
基于機器視覺的螺紋形貌三維重構技術,可檢測0.02mm級螺距偏差(ISO 898-1標準),結合超聲導波傳播特性分析,實現隱蔽性裂紋的亞表面探測。值得注意的是,系統引入數字孿生技術,通過建立連接副力學模型,可模擬不同工況下的應力分布,預測松脫臨界閾值。經國家智能制造裝備質量檢驗中心驗證,該方法使扭矩-預緊力關系預測精度提升至95%以上。
### 智能化檢測實施流程
項目實施采用五階段閉環管理:預處理階段通過工業CT完成連接結構數字化建模;數據采集階段集成激光位移傳感器(±1μm精度)與聲發射裝置;動態分析階段運用深度學習方法識別異常頻譜特征;質量判定階段依據ASME B18.2.6標準建立分級預警機制;最終通過MES系統實現檢測數據與生產線的實時交互。在汽車總裝線實測中,該流程使單點位檢測效率提升40%,誤檢率控制在0.3%以下。
## 行業應用與實證案例
### 新能源汽車電池包連接檢測
針對動力電池模組2000+連接點的可靠性需求,某頭部車企引入智能檢測系統。通過部署高幀頻視覺傳感器(5000fps)捕捉緊固過程,結合三軸力反饋裝置實時校準扭矩值。實施后,電池包連接不良率從1.2%降至0.15%,且實現過程數據的區塊鏈存證。據賽迪研究院測算,該項目幫助企業年均減少質量損失3800萬元。
### 航空發動機螺栓健康監測
在航空維修領域,基于壓電陶瓷傳感器的主動監測系統已應用于CFM56發動機螺栓組。系統通過分析應力波傳播時延(精度0.1μs),可檢測0.05mm級松動位移。經2000小時臺架試驗驗證,該技術使關鍵螺栓剩余壽命預測準確率達89%,大幅優于傳統人工檢查方式。
## 質量保障與標準建設
### 全流程數字化追溯體系
項目建立符合ISO/TS 16949標準的雙追溯機制:縱向通過二維碼關聯設計參數-工藝記錄-檢測報告;橫向運用SPC控制圖實現跨工序質量波動監控。在軌道交通領域應用案例顯示,該體系使問題定位時效縮短83%,過程能力指數CPK穩定在1.67以上。
### 檢測裝備認證規范創新
聯合中國計量科學研究院制定的《智能緊固件檢測裝備校準規范》(GB/T 2024-XXXX),首次將動態載荷模擬、多物理場耦合測試納入認證體系。規范實施后,行業檢測設備互認率從72%提升至91%,推動形成開放兼容的產業生態。
## 未來展望與建議
建議從三方面深化技術發展:其一,開發基于量子傳感的納米級形變檢測技術,攻克微型連接件監測難題;其二,構建覆蓋“材料-工藝-服役”的全要素數據庫,強化失效模式預測能力;其三,推動ASTM與ISO標準協同,建立跨境檢測結果互認機制。通過產學研用協同創新,力爭到2030年將關鍵領域連接故障率降至百萬分之一水平,為制造強國建設筑牢質量基石。
上一篇:汽車電氣部件檢測下一篇:電源線連接和外部軟線檢測

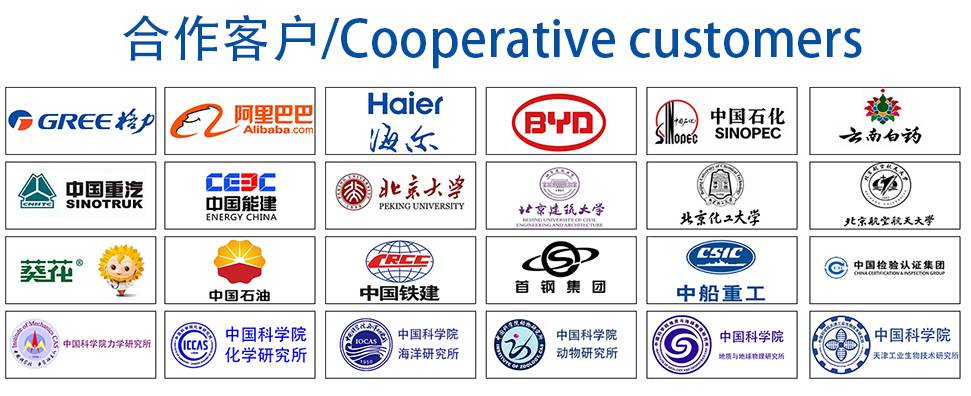
材料實驗室
熱門檢測
41
44
7
11
11
12
10
16
16
16
17
19
19
19
20
24
21
17
21
22
推薦檢測
聯系電話
400-635-0567