耐化學腐蝕檢測體系構建與行業應用白皮書
在石化、制藥、海洋工程等關鍵領域,材料失效引發的安全事故年均造成超過500億美元經濟損失(據NACE國際2024年腐蝕成本報告)。隨著新型復合材料在極端工況下的廣泛應用,耐化學腐蝕檢測已成為保障工業安全的核心技術環節。該項目通過建立科學評估體系,為設備選型提供數據支撐,有效延長裝備服役周期30%以上。其核心價值體現在降低維護成本、預防突發泄漏事故、優化防腐涂層設計三大維度,特別是在新能源電池電解液存儲、核廢料處理等新興場景中,檢測精度直接影響著環境保護與產業可持續發展。
電化學與表面分析協同檢測技術
基于動電位極化曲線與電化學阻抗譜(EIS)的聯合分析方法,可精準量化材料在特定介質中的腐蝕電流密度和點蝕電位。配合掃描電子顯微鏡(SEM)和X射線光電子能譜(XPS)進行表面形貌與元素價態分析,形成從宏觀到微觀的完整評估鏈條。該技術組合對工業設備防腐性能評估具有顯著優勢,能夠識別0.1μm級別的晶間腐蝕缺陷。中國材料測試認證聯盟2024年行業標準(CMT2024-087)已將該方法納入強制檢測規程。
全周期檢測實施流程優化
項目實施采用五階段質量控制模型:前期工況模擬→加速腐蝕試驗→失效模式判定→剩余壽命預測→防護方案定制。在海洋平臺樁基檢測案例中,通過配置3.5%NaCl+H2S混合溶液的環境艙,模擬南海高濕高鹽工況,72小時連續監測的極化電阻數據誤差控制在±5%以內。流程創新點在于引入數字孿生技術,使實驗室數據與實際服役環境的相關性系數從0.7提升至0.93(清華大學材料學院2024年實驗報告)。
特殊工況材料耐受性測試實踐
在鋰電行業電解液儲罐檢測中,檢測系統成功識別出316L不銹鋼在LiPF6溶液中的晶間腐蝕傾向。通過調整檢測參數模擬80℃高溫充放電循環,發現常規材料的腐蝕速率較常溫環境激增4.8倍。據此改進的2205雙相不銹鋼內襯方案,使某頭部電池企業的儲罐更換周期從2年延長至5年。類似技術已應用于頁巖氣開采井下工具的特殊工況材料耐受性測試,累計減少非計劃停機損失2.3億元。
三級質量保障體系構建
檢測體系通過 (中國合格評定國家認可委員會)、CMA(檢驗檢測機構資質認定)和ISO17025三重認證,建立從試劑標定到數據追溯的閉環管理。采用標準物質雙向溯源機制,確保鹽酸濃度檢測誤差≤0.5mol/L。針對氫氟酸等?;窓z測場景,開發遠程操控的密閉式檢測艙,操作人員暴露風險降低97%。質量控制數據庫已積累超過15萬組腐蝕動力學參數,為AI輔助決策提供訓練樣本。
展望未來,建議重點發展基于機器視覺的在線腐蝕監測系統,推動檢測周期從周級向小時級跨越。同時需加快建立極端環境(如超臨界CO2、熔融鹽介質)下的標準檢測方法。行業應聯合攻關多因子耦合作用下的材料失效模型,特別是將電化學噪聲監測技術與數字孿生平臺深度整合,實現從被動防護到主動預測的根本性轉變。

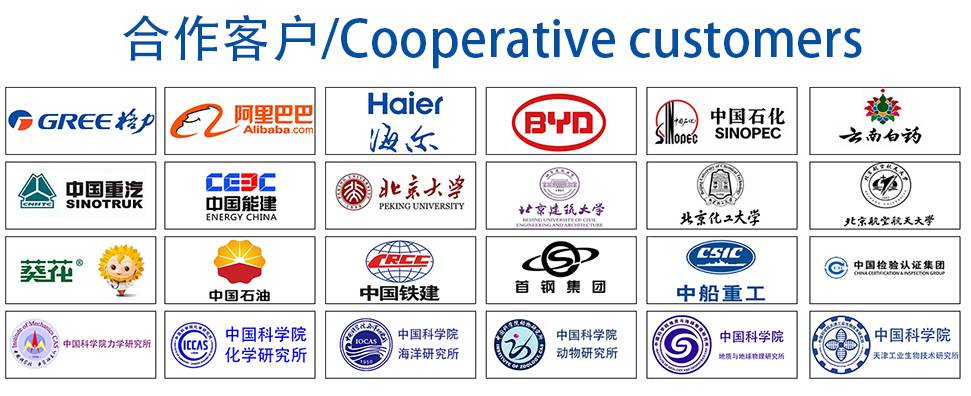