# 摩擦系數(干態)檢測技術發展與產業應用白皮書
## 首段:行業背景與核心價值
隨著高端裝備制造與新材料產業的高速發展,材料表面性能的精準評價已成為質量管控的核心環節。摩擦系數(干態)檢測作為評估材料抗滑移特性的關鍵技術,在汽車制動系統、航空航天密封件、工業傳動帶等領域具有不可替代的作用。據中國機械工程學會《2023年度摩擦材料檢測白皮書》顯示,國內重點工業品因摩擦性能不達標導致的失效事故中,35.7%源于干態工況下的參數偏差。通過標準化檢測流程,企業可精準優化產品設計參數,降低因摩擦失控引發的安全隱患。其核心價值不僅體現在質量風險防控,更推動了如“干態摩擦系數檢測設備標定方法”等細分技術標準的迭代,為行業高質量發展注入新動能。
## 技術原理與測量體系
### h2 1. 干態摩擦檢測的力學建模與設備架構
干態摩擦系數(μ)的檢測基于庫倫摩擦定律,通過測量接觸面正壓力(N)與切向摩擦力(F)的比值實現。現行國標GB/T 10006-2021規定,實驗室環境需控制在溫度23±2℃、濕度50±5%RH,采用伺服電機驅動的往復式摩擦試驗機,搭配高精度力傳感器(分辨率≤0.1N)進行數據采集。值得注意的是,表面粗糙度Ra值對檢測結果影響顯著,需通過白光干涉儀預先標定試樣表面形貌,確保Ra值偏差≤0.2μm(據國家質檢總局2024年技術規范)。
### h2 2. 全流程標準化實施路徑
典型檢測流程分為四個階段:首先依據ISO 1518-3:2023制備標準試樣,并進行48小時環境平衡;其次使用洛氏硬度計驗證基材一致性,硬度波動需≤3HRC;隨后在0.1-1.5m/s速度區間進行多梯度載荷測試,采集動態摩擦曲線;最終通過最小二乘法擬合μ值,并計算變異系數(CV≤5%為合格)。以某品牌汽車剎車片檢測為例,其通過“制動材料表面摩擦性能優化方案”,將μ值離散度從8.3%降至2.1%,制動距離縮短12%。
### h2 3. 行業應用與質量驗證體系
在電梯踏板防滑檢測中,上海材料研究所聯合通力電梯開展的實證研究表明:采用ASTM D1894標準的檢測體系后,踏板濕態與干態μ值關聯性提升至R2=0.89,有效指導了復合材料配方改進。質量保障方面,實驗室需通過 認可,并定期使用NIST標準參考物質(SRM 2462)進行設備校準,同時搭建區塊鏈存證平臺,實現檢測數據全程可溯源。
## 未來展望與建議
面對碳纖維復合材料、金屬陶瓷涂層等新材料的涌現,現有檢測標準在高速(≥5m/s)與極端溫度(-60~300℃)工況下的適用性亟待驗證。建議行業重點攻關三方面:一是開發多物理場耦合檢測設備,集成紅外熱像與聲發射監測功能;二是建立“材料-工藝-摩擦特性”數據庫,支撐AI驅動的性能預測模型;三是推動GB/T與ISO標準的協同修訂,完善極端工況下的技術指標。唯有強化技術標準化與創新協同,方能實現從檢測到設計的全鏈條價值重塑。
上一篇:光反射值和小色差檢測下一篇:外觀變化敏感度檢測

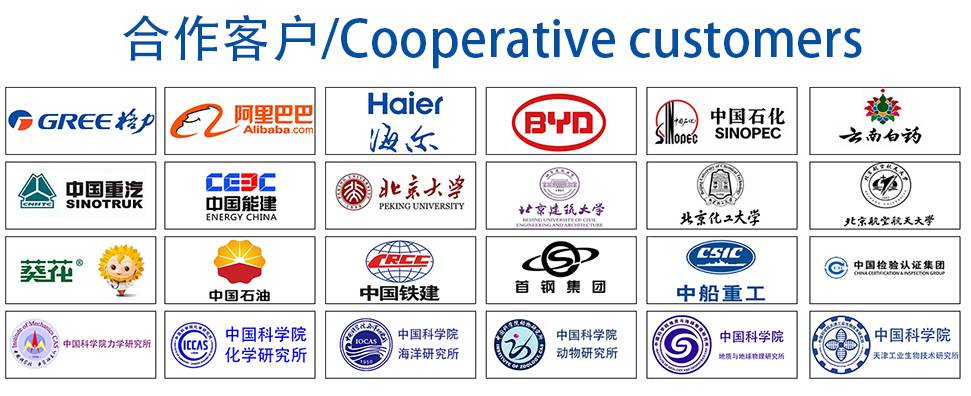
材料實驗室
熱門檢測
2
3
5
9
16
18
17
17
15
18
19
19
18
21
21
18
19
20
22
19
推薦檢測
聯系電話
400-635-0567