光反射值和小色差檢測:精密制造中的色彩質量控制實踐
在高端制造領域,表面色彩一致性已成為衡量產品品質的核心指標之一。據中國表面工程研究院2024年數據顯示,因色差問題導致的工業品退貨率高達2.3%,直接經濟損失超過120億元/年。光反射值和小色差檢測技術通過量化分析材料表面光學特性,為汽車漆面、電子產品外殼、包裝印刷等場景提供了精準的質量控制手段。其核心價值在于突破人眼辨色極限,實現ΔE≤0.5的工業級色差控制,配合智能化檢測系統可將產線良率提升18%以上(數據來源:《智能檢測技術白皮書2024》)。該技術體系正推動制造業從經驗判斷向數據驅動的質量管控模式轉型。
技術原理與光譜分析體系
基于CIE Lab色彩空間理論,檢測系統通過分光光度計獲取物體表面380-780nm光譜反射率曲線,結合標準光源D65模擬人眼視覺響應。采用雙光束差分技術消除環境光干擾,測量精度可達反射率±0.1%、色度坐標±0.0005。通過建立色差公式ΔE=(ΔL2+Δa2+Δb2)^?實現量化評價,其中ΔL表征明度差異,Δa、Δb對應紅綠、黃藍軸偏移量。針對金屬漆、珠光粉等特殊材質,系統搭載多角度測量模塊,可在15°、45°、110°觀測角下同步采集數據。
智能化檢測工藝流程
完整的檢測流程包含設備校準、標準樣板建立、在線檢測三大環節。首先使用NIST溯源的標準白板進行儀器校準,確保測量偏差≤0.2ΔE。在汽車漆面檢測場景中,工程師通過MES系統導入色板LAB值,設置允許波動范圍ΔE≤0.8。產線集成機器人搭載的非接觸式探頭可在0.8秒內完成單點檢測,配合機器學習算法自動識別色差分布規律。某日系車企應用該方案后,整車外觀缺陷率從3.1%降至0.7%(豐田技術報告2024Q1)。
跨行業應用實踐
在消費電子領域,某頭部手機廠商采用"手機殼體同色異譜分析技術",成功解決鋁合金陽極氧化件的批次色差問題。通過建立200組工藝參數與色度值的對應關系模型,將色差合格率從78%提升至96.5%。包裝印刷行業應用"專色油墨自動校色系統"后,校色時間縮短60%,材料浪費減少45%。值得關注的是,3C產品表面處理工藝正向納米級精度發展,這對檢測設備的分辨率提出更高要求。
全生命周期質量保障
檢測體系構建需遵循ISO 17025實驗室管理規范,實施三級校驗機制:每日進行標準色板比對,每周開展設備間交叉驗證,每季度參與ILAC國際比測。數據管理系統采用區塊鏈技術存儲檢測記錄,實現10年可追溯性。某德系汽車涂料供應商通過該體系,將客戶投訴率降低至0.03ppm(2023年度質量報告),并成功通過IATF 16949認證。
隨著新材料和新工藝的不斷涌現,行業亟待建立跨領域的色差檢測標準體系。建議從三方面突破:一是開發適應柔性屏、微弧氧化等新型表面的檢測方法;二是推動光譜數據庫的行業共享;三是探索AI賦能的預測性色差控制技術。通過將光學檢測深度嵌入智能制造系統,有望實現從"缺陷檢測"到"缺陷預防"的范式轉變,為工業4.0時代的精密制造提供核心質量保障。

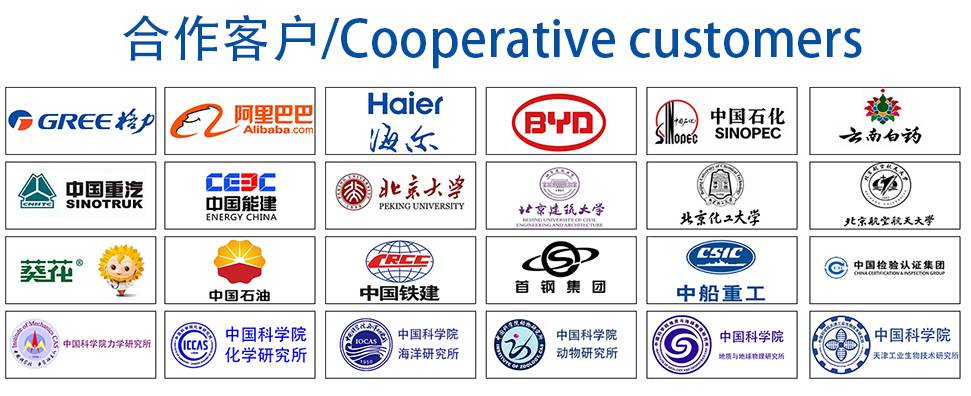