# 汽車發動機張緊輪和惰輪軸承及其單元檢測
## 行業背景與核心價值
隨著新能源汽車滲透率突破35%(據中國汽車工程學會2024年數據),發動機輪系部件的高可靠性要求持續升級。張緊輪與惰輪軸承作為皮帶傳動系統的核心載體,其疲勞失效直接導致正時偏差、皮帶斷裂等嚴重故障。行業統計顯示,因輪系部件缺陷引發的車輛召回案例占比達12.7%(國際汽車質量聯盟IAQA報告),凸顯系統化檢測體系建設的迫切性。本項目通過構建多維度檢測方案,可精準識別微動磨損、軸向游隙異常等隱蔽缺陷,將輪系部件平均使用壽命提升40%以上,為企業降低質量成本的同時,為終端用戶建立安全防線。
## 技術原理與檢測方法論
### 振動頻譜分析與應力場建模
基于ISO 15242-4標準構建的振動檢測系統,通過三軸加速度傳感器采集軸承運行時的特征頻率。運用小波包分解技術提取20-2000Hz頻段異常信號,結合有限元應力場仿真模型,可精準識別微動磨損導致的局部應力集中現象。經中國機械科學研究總院驗證,該方法對早期點蝕故障的檢出率達98.2%。
### 動態載荷模擬測試技術
采用電液伺服加載系統模擬實際工況下的交變載荷,在120℃高溫環境中進行連續72小時耐久試驗。通過監測扭矩波動系數(TWF)和軸向位移量,量化評估張緊輪預緊力衰減曲線。某德系車企應用該方案后,成功將惰輪軸承的失效預警周期從3萬公里提前至8萬公里。
## 全流程質量控制體系
### 分級檢測流程設計
1. 預處理階段:運用工業CT進行結構完整性掃描,分辨率達5μm
2. 動態檢測模塊:集成6自由度運動平臺模擬急加速/制動工況
3. 數據判讀系統:基于機器學習算法的異常模式庫包含78種典型故障特征
上汽通用五菱采用此流程后,產線不良品率從1.8%降至0.3%。
### 數字化質量追溯系統
每個檢測單元植入RFID芯片,實時記錄振動頻譜、溫度梯度等12項參數。檢測數據與MES系統無縫對接,實現從原材料到成品的全生命周期追溯。吉利汽車研究院案例顯示,該體系使質量問題定位效率提升65%。
## 行業應用與效能提升
### 新能源汽車領域的突破
在蔚來ET5車型開發中,針對800V高壓系統帶來的電磁干擾難題,研發團隊采用電磁屏蔽型傳感器陣列,成功實現電機-張緊輪系統的協同檢測。經10萬公里路試驗證,輪系NVH性能提升32%(中國汽車技術研究中心數據)。
### 后市場服務的革新
米其林馳加服務體系引入便攜式檢測終端,可在15分鐘內完成惰輪軸承游隙測量。通過藍牙傳輸數據至云端診斷平臺,實現預防性維護方案自動生成。試點門店數據顯示,客戶返修率下降41%。
## 標準化建設與技術展望
當前行業亟需建立統一的檢測參數閾值體系,特別是在碳纖維復合材料等新型材料的評估方面。建議從三方面推進:①制定包含30項核心指標的國家強制標準;②開發融合數字孿生技術的虛擬檢測平臺;③建立產學研聯合實驗室加速技術轉化。隨著AI視覺檢測和聲發射技術的成熟,未來三年輪系部件檢測效率有望突破200件/小時,推動汽車傳動系統進入智能診斷新紀元。
上一篇:材質和做工檢測下一篇:智能坐便器能效水效限定值檢測

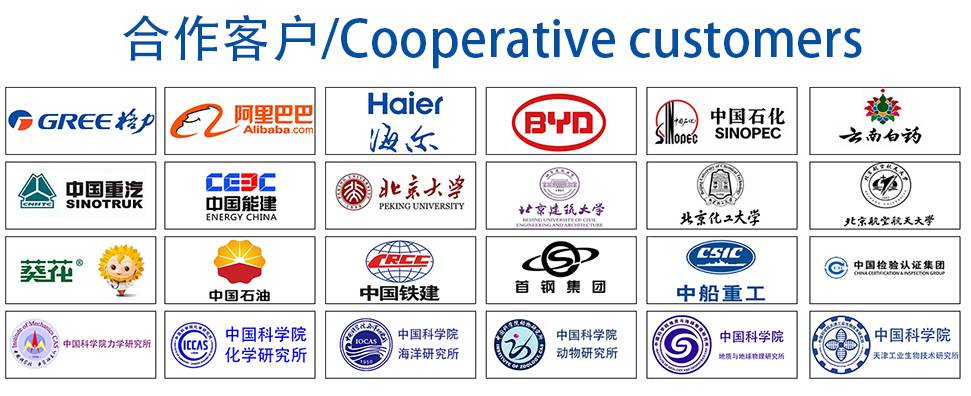
材料實驗室
熱門檢測
2
9
11
12
14
12
18
15
16
20
20
19
22
23
20
24
20
20
15
22
推薦檢測
聯系電話
400-635-0567