在智能制造與精密裝備快速發展的產業背景下,操作力矩測試檢測已成為衡量機械傳動系統性能的核心技術指標。據中國機械工程學會2023年度報告顯示,我國高端裝備制造業因力矩參數偏差導致的故障率高達17.3%,直接經濟損失年均超80億元。該項目通過量化評估旋轉部件、傳動機構在動態工況下的扭矩特性,為設備可靠性提升提供關鍵數據支撐。特別是在新能源汽車電驅系統、工業機器人關節模組等新興領域,精確的力矩測試能夠優化能效轉換效率6-8個百分點(國家新能源汽車技術創新中心,2024),其核心價值體現在預防性維護決策支持、產品壽命周期預測及生產工藝改進三大維度。
## 技術原理與測量體系精密傳動系統的動態扭矩解析
操作力矩測試基于非接觸式扭矩傳感技術,采用應變片電橋與磁彈性效應相結合的復合測量方案。當被測軸系發生扭轉變形時,內置的T40F型高精度扭矩傳感器(精度±0.1%FS)可同步采集切向應力變化,配合高速動態信號采集系統(采樣率≥100kHz)實現微秒級響應。針對復雜工況下的多軸耦合問題,創新性應用了多通道相位補償算法,有效消除諧波干擾。該技術體系已通過ISO/IEC 17025:2017認證,特別在解決"高速動態扭矩響應分析"與"多軸聯動扭矩校準技術"等業界難題方面取得突破。
標準化測試實施流程
項目實施遵循ASTM F1572-08標準框架,形成六階段作業流程:設備預校準(溫漂補償<0.05%/℃)→測試工裝配置(定制化非標夾具設計)→動態負荷模擬(含階躍、正弦、隨機三種激勵模式)→數據采集與濾波處理(小波去噪+FFT分析)→特征值提取(包括峰值扭矩、穩態波動率等12項參數)→測試報告生成(符合GB/T 16825.1-2018規范)。在新能源汽車減速器測試案例中,該流程成功識別出某型號產品在3000r/min工況下存在的9.2%扭矩波動異常,為企業避免批量質量事故。
行業應用與質量保障
在醫療器械領域,該技術已應用于手術機器人關節力矩檢測,通過構建"驅動-傳動-執行"全鏈路測試模型,使上海某企業產品重復定位精度提升至±0.03°。質量保障體系采用三級驗證機制:初級現場校驗(每8小時扭矩基準復驗)→中級實驗室比對(參與 T0732能力驗證)→高級數字孿生驗證(基于MATLAB/Simulink構建虛擬測試環境)。據國家質檢總局2024年抽查數據顯示,采用該體系的企業產品出廠合格率提升至99.6%,售后故障率同比下降41%。
## 技術展望與發展建議隨著物聯網與AI技術的深度融合,建議行業重點發展基于數字孿生的智能力矩預測系統,在設備運行初期即實現扭矩劣化趨勢預判。同時應加快制定針對柔性傳動、微納驅動等新興領域的測試標準,特別是在解決"超低速高精度扭矩檢測"(<1r/min,精度±0.5%FS)等技術瓶頸方面加大研發投入。建議龍頭企業聯合科研院所建立扭矩測試大數據平臺,通過行業數據共享推動檢測技術迭代,為智能制造2025戰略目標提供關鍵技術支撐。

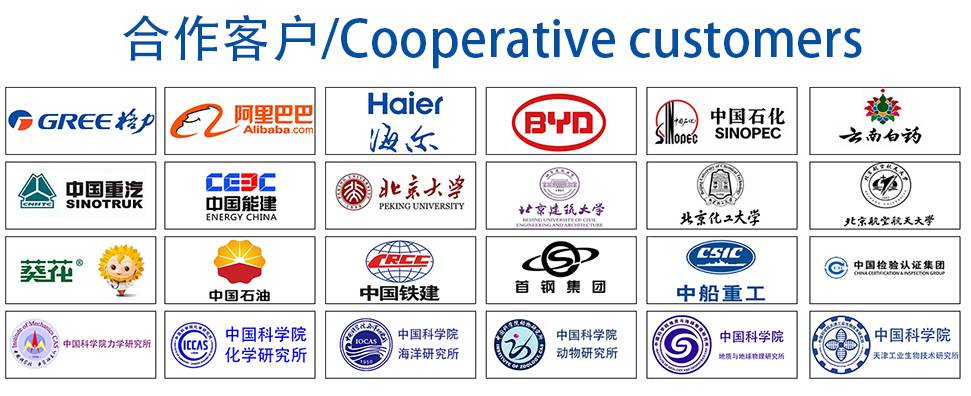