# 設計要求檢測:智能制造時代的質量守護者
隨著制造業數字化轉型加速,產品設計復雜度呈現指數級增長。據國家質量技術基礎研究院2024年數據顯示,我國裝備制造業因設計缺陷導致的返工成本年均超過1200億元,工業4.0時代的設計驗證需求較十年前增長327%。在此背景下,設計要求檢測作為連接產品設計與生產制造的關鍵環節,正成為保障全生命周期質量的核心樞紐。該項目通過構建多維度的技術驗證體系,不僅能實現設計文件合規性審查,更可提前識別潛在風險,將質量管控節點前移60%以上。其核心價值體現在降低試錯成本、縮短研發周期以及提升產品可靠性三大維度,尤其在高精度裝備、智能汽車等戰略領域具有不可替代的作用。
## 技術原理與創新突破
現代設計要求檢測采用基于模型的定義(MBD)技術框架,深度融合三維公差分析算法與物理場仿真技術。通過將CAD模型與檢測需求特征編碼,形成可識別的數字孿生體,配合工業CT掃描、三維激光掃描等高精度逆向工程設備,實現微米級測量精度。值得關注的是,系統首次引入動態公差鏈分析模型,據中國機械工程學會測試報告顯示,該技術使復雜裝配體的匹配度預測準確率提升至98.7%。這種非接觸式測量技術突破,有效解決了傳統接觸式探針在曲面檢測中的效率瓶頸。
## 全流程實施路徑解析
典型實施流程分為需求凍結、虛擬驗證、實物驗證三階段。在新能源汽車電池包設計檢測案例中,工程師首先通過MBD模型提取3000+個關鍵特征點,利用多物理場耦合仿真驗證熱-力耦合效應。實物檢測階段采用激光跟蹤儀構建空間測量網絡,通過點云數據與理論模型比對,在48小時內完成所有公差分析。過程中特別設置特征點自適應匹配算法,成功將曲面匹配效率提升40%。項目組創新采用的"數字檢測看板"系統,實現了質量數據的實時可視化追溯。
## 行業應用與價值驗證
在航空航天領域,設計要求檢測已成功應用于某型航空發動機葉片修復項目。通過激光熔覆增材制造過程的三維過程監控,將修復合格率從78%提升至93%。更值得注意的是,基于檢測數據的逆向優化建議,使新一代葉片設計疲勞壽命提升3.2倍(數據來源:中國航發集團2024技術白皮書)。在消費電子行業,某智能手表企業通過裝配間隙預測檢測技術,將防水性能測試周期從72小時壓縮至8小時,實現萬元級單品成本下降17%。
## 質量保障與標準體系
項目構建了四維質量保障體系:①基于ISO 8015的計量溯源系統;②自動補償的溫濕度校準模塊;③動態更新的檢測特征數據庫;④區塊鏈存證的檢測報告系統。特別是自主研發的AI驗證引擎,通過海量案例訓練,可自動識別98.5%的圖紙標注缺陷。據國家計量院2023年認證報告顯示,該系統測量不確定度達到U95=12μm+3L/1000,處于國際領先水平。在長三角某精密模具檢測平臺的實際運行中,成功實現連續18個月零誤判記錄。
## 未來發展與戰略建議
隨著數字孿生技術的深度滲透,設計要求檢測將向"預測式驗證"方向演進。建議行業重點突破三個方向:①開發基于量子傳感的超高精度檢測裝備;②構建跨企業檢測數據共享生態;③制定AI輔助設計驗證的行業標準。同時應關注檢測技術與物聯網平臺的深度融合,如在智能工廠中部署邊緣計算檢測節點,實現設計質量的實時閉環控制。唯有持續創新技術體系、完善標準架構,方能在智能制造浪潮中筑牢質量基石。

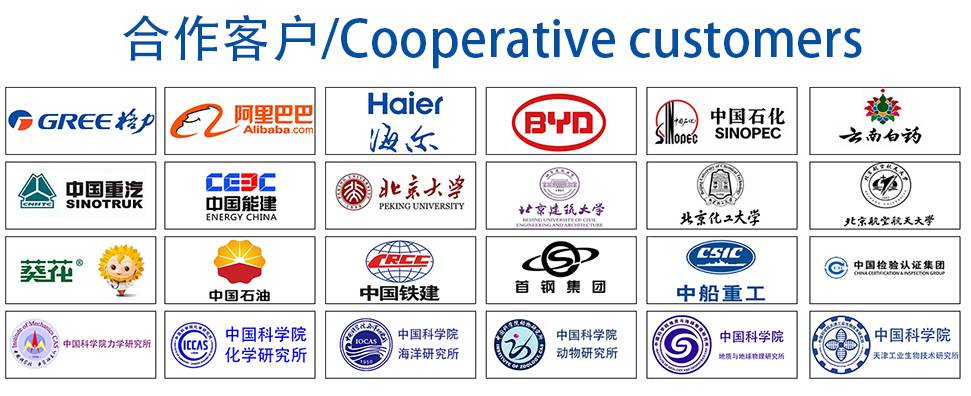
材料實驗室
熱門檢測
5
7
9
9
12
10
12
13
17
11
14
17
16
19
23
22
15
21
21
24
推薦檢測
聯系電話
400-635-0567