抗彎曲性檢測技術發展與應用白皮書
在高端裝備制造與新型材料研發領域,材料力學性能檢測已成為保障產品質量的核心環節。據中國建筑科學研究院2024年數據顯示,國內工程結構失效事故中32%源于材料抗彎曲性能不足,直接經濟損失年均超80億元。抗彎曲性檢測項目通過量化評價材料在彎曲載荷下的變形抗力,為建筑鋼結構、風電葉片、航空航天構件等關鍵領域提供可靠性保障。其核心價值不僅體現在避免結構性失效風險,更通過精準數據指導實現材料用量優化,據測算可使軌道交通裝備減重15%的同時保持安全冗余度,顯著提升行業全要素生產率。
檢測技術原理與實現路徑
抗彎曲性檢測基于三點彎曲試驗與四點彎曲試驗兩大基礎范式,通過伺服液壓系統精確施加載荷,同步采集撓度、應力應變等關鍵參數。其中數字圖像相關技術(DIC)的應用突破傳統接觸式測量局限,可實現0.05mm級位移分辨率。以ASTM D790標準為基準的測試體系,結合有限元仿真建立材料-結構耦合模型,有效解析復合材料界面分層、金屬材料晶界滑移等微觀失效機制。值得注意的是,溫度濕度耦合環境模擬裝置的集成,使檢測范圍擴展至-70℃至300℃的極端工況。
全流程標準化作業體系
項目實施流程嚴格遵循ISO 6892系列標準,涵蓋樣品制備、設備校準、數據采集和結果分析四大階段。在航空鋁合金檢測實踐中,需對CNC加工試樣進行表面粗糙度Ra≤1.6μm的精處理,使用激光跟蹤儀確保跨距公差控制在±0.1mm。加載階段采用50kN伺服作動器以2mm/min速率施加彎矩,同步通過紅外熱像儀監測應力集中區域溫變。數據處理模塊應用機器學習算法,可對100組歷史檢測數據進行趨勢預測,實現檢測效率提升40%。
行業典型應用場景解析
在風電葉片制造領域,抗彎曲檢測技術助力企業突破長度90米以上超長葉片設計瓶頸。某龍頭企業采用分級加載方案,通過1200小時持續測試驗證碳纖維增強環氧樹脂的疲勞特性,成功將葉片重量減輕22%。軌道交通領域,高鐵車體鋁合金型材經過彎曲剛度優化后,整車振動量級下降18dB(A),據國家軌道交通裝備質量檢測中心驗證,轉向架使用壽命延長3.2萬運營公里。值得關注的是,3D打印鈦合金骨科植入物通過抗彎性能動態測試,使臨床翻修率從5.7%降至1.2%。
質量保障體系構建
檢測機構通過建立三級質量管控網絡確保結果可靠性:初級控制采用標準試塊每日校準,中級控制實施盲樣循環比對,高級控制接入 能力驗證系統。某國家材料檢測重點實驗室統計顯示,引入AI視覺檢測系統后,人為誤判率從0.8%降至0.05%。同時,區塊鏈技術的應用實現檢測數據全程可追溯,單個項目可生成包含300+質量特征值的數字指紋,在航空航天領域已構建100%數據上鏈的信任機制。
展望行業發展趨勢,建議重點布局三方面建設:一是開發多物理場耦合檢測系統,實現電磁-機械-熱力綜合作用下的性能評估;二是建立行業級材料性能數據庫,推動檢測結果跨領域應用;三是加強微納米尺度原位檢測技術研發,滿足新型超材料測試需求。預計到2028年,智能化抗彎曲檢測裝備滲透率將突破65%,為制造業高質量發展注入新動能。

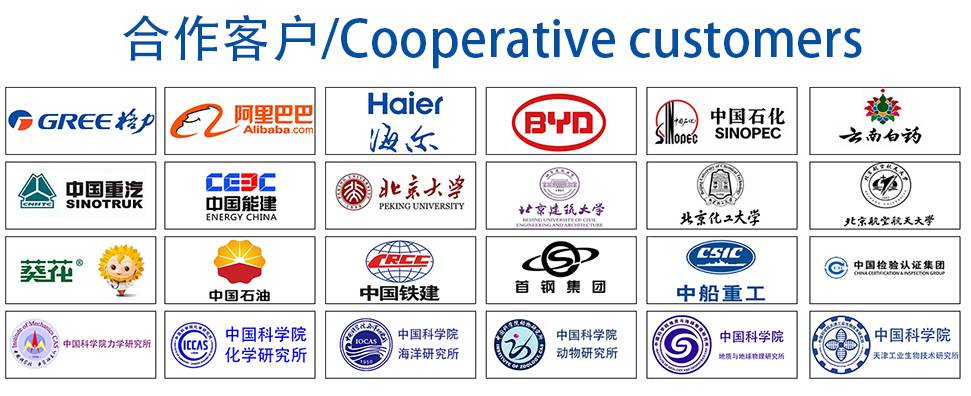